- Efficient and high purity separation of plastics with particles of less than 1 mm
- Transforms mixed plastics into pure, market-ready materials through precision separation
- Cost-efficient: no need for post-dewatering and low water and energy costs
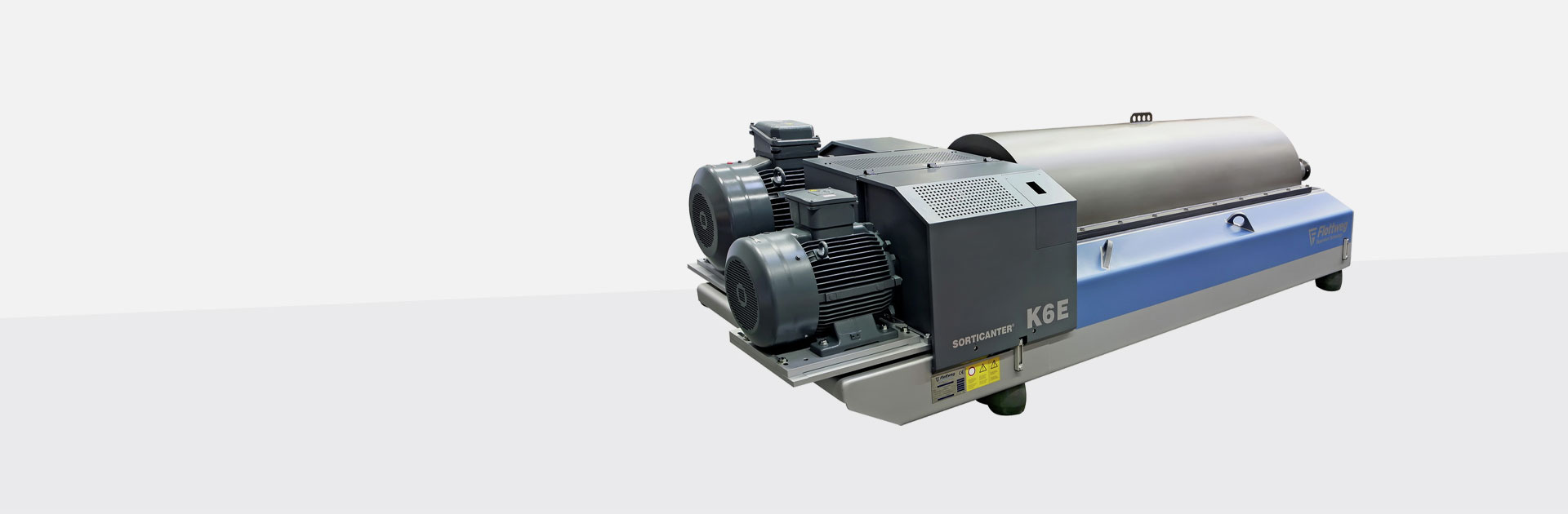
Flottweg Sorticanter®
The recycling decanter from Flottweg
Innovative centrifuge technology for plastics recycling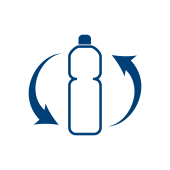
Flottweg's Sorticanter® is designed to tackle the challenging task of recycling plastics by separating them based on their densities. This centrifuge technology excels in processing plastics, including PVC, offering high separation efficiency. The Sorticanter® operates by using a centrifugal force that is much more effective than traditional gravity-based methods. Its capability to separate plastic particles, even those smaller than 1 mm, and achieve a higher dryness level in the output makes it a valuable asset in recycling operations. Additionally, the high g-forces within the Sorticanter® and its specialized scroll design ensure that the discharged plastic particles are much drier than those separated by other processes, enhancing product quality and the value of the end product. The Sorticanter® not only streamlines the recycling process but also contributes to environmental sustainability by reducing waste and the need for new raw materials. Its low consumption of fresh water and energy also reduces operational costs, further underlining its efficiency and cost-effectiveness in recycling applications.
Businesses with an increasing focus on environmental protection and recycling demand new, innovative solutions. This prompted Flottweg to develop the Sorticanter® for the processing of plastics.
Naturally occurring raw materials such as plants, coal, natural gas and crude oil are the basic materials for the production of plastics. These raw materials cannot be recovered through processing in chemical steps. The recycling of plastics is therefore an issue for every environmentally conscious person. The Sorticanter® makes it possible to make a contribution to environmental protection in accordance with the principles of ecology and economy.
The centrifugal force generated enables the Sorticanter® to separate different types of plastic from each other. This enables operators to achieve the highest possible purity of plastics. Collecting and recycling plastics also reduces disposal costs and mountains of waste.
Flottweg Sorticanter® has been processing a wide variety of plastics since 1995. The Sorticanter® has impressing performance and exceptional quality and durability.
Application area: plastics processing
How does the Sorticanter® function?
When processing plastics (waste, plastic fibers and light packaging), it is important that the individual plastics are of a single material type. Many plastics differ in their density. For this reason, the so-called swim-sink separation process has proven to be efficient. In this separation process, a separation liquid is used (usually water), whereby the specific weight of the liquid lies between the weight of the two types of plastic to be separated.
In a container, the "heavy" plastic with the higher density sinks to the bottom, while the lighter plastic with the lower density floats on the liquid.
The same principle is also used in a centrifuge. In the container, separation is by gravity (1 g), while in a centrifuge the plastics are separated by centrifugal force (a multiple of the earth’s gravity). Sorting in a centrifuge is therefore much faster and the sorted plastic phases are much drier. The "heavy" plastic phase is centrifuged onto the bowl wall and from there conveyed by the decanter scroll to the discharge (heavy phase). The "light" plastic collects on the liquid. The liquid flows off along the scroll and takes the light plastic particles with it. A special scroll design ensures that even the light phase is conveyed in the direction of the solids discharge (light phase) and dehumidified. The liquid runs off under pressure via an impeller.
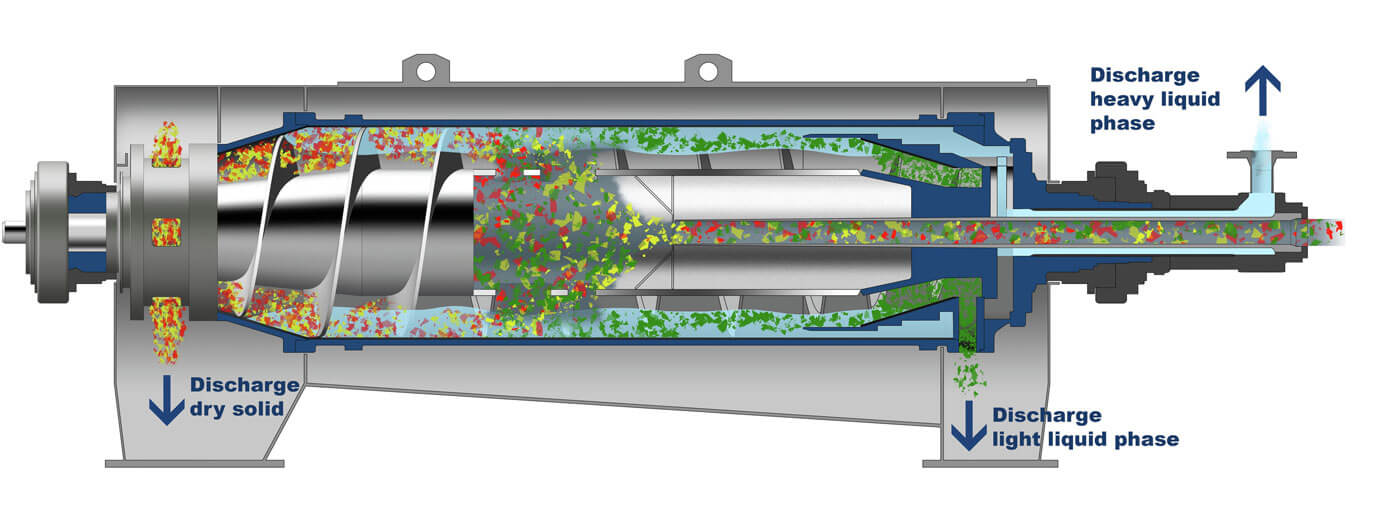
Product features
Efficiency
Due to the high g-forces in the Sorticanter® and the unique scroll design, the discharged plastic particles are considerably drier than with other processes. The plastics can therefore be separated more efficiently and more homogeneously. This increases the product quality and thus also the value of the end product. In addition, the Sorticanter® can separate particles with a diameter of less than 1 mm as well as mixtures of fabric fibers that are unsuitable for static separation. Compared to other processes, it ensures a higher degree of selectivity.
- Better product quality and thus higher value of the end product
- Separation of mixtures of substances which cannot be separated by static separation (fibers)
- Separation of particles that are smaller than 1 mm
Cost saving
Thanks to the high selectivity and dehumidification of the plastics, a subsequent dewatering is not required. This reduces the necessary expenditure. Since the Sorticanter® requires a minimal amount of personnel, operating costs can be saved. The low consumption of fresh water and thermal energy also has a positive effect on operating costs. Since the plastics are already mechanically dewatered, this saves costs in thermal dehumidification.
- Additional post-dewatering (centrifuge) is not required
- Low fresh water consumption
- Minimum personnel expenditure and thus cost savings for the operator
- Low thermal energy consumption
Process reliability
Flottweg Sorticanter® are usually 8000 hours per year in operation. This and Flottweg's many years of experience guarantee high process reliability and machine availability. In addition, our Sorticanter® is developed and manufactured exclusively in Germany. This means that we can maintain the high quality of our machines and components and ensure a long service life. For example, by adding a separating liquid, dust is washed off the surface of the plastics. Air bubbles and surface effects have no influence on the separation, which in turn ensures a high availability.
- Usually 8000 hours operating time per year
- High availability
- Quality Made in Germany and high engineering expertise
- Air bubbles and other disturbing effects do not have an influence on separation
Operation
The high-quality materials of our Sorticanter® reduce the expenditure for servicing and maintenance measures. The machine is easy to control and maintain; worn parts are easy to replace. This reduces the workload on the operating personnel. The operating parameters can be clearly controlled via a user interface. As the Sorticanter® - like other decanter centrifuges - forms a closed system, the operating personnel's exposure to unpleasant odors is minimal.
- Minimum personnel deployment
- Low maintenance requirement
- Low odor nuisance due to closed system
K4D
Dimensions [mm/ft]* | 3400x130x1100 / 11,15x4,1x3,67 |
Weight [kg/lb]* | 3050 / 6710 |
K6E
Dimensions [mm/ft]* | 5100x1800x1300 / 16,79x5,81x4,13 |
Weight [kg/lb]* | 9750 / 21450 |