- Nozzle separators are available in two basic designs (2-phase and 3-phase)
- Continuous high-performance separation with maximum clarification for heavy solids loads
- Robust and compact design with durable and high-quality materials
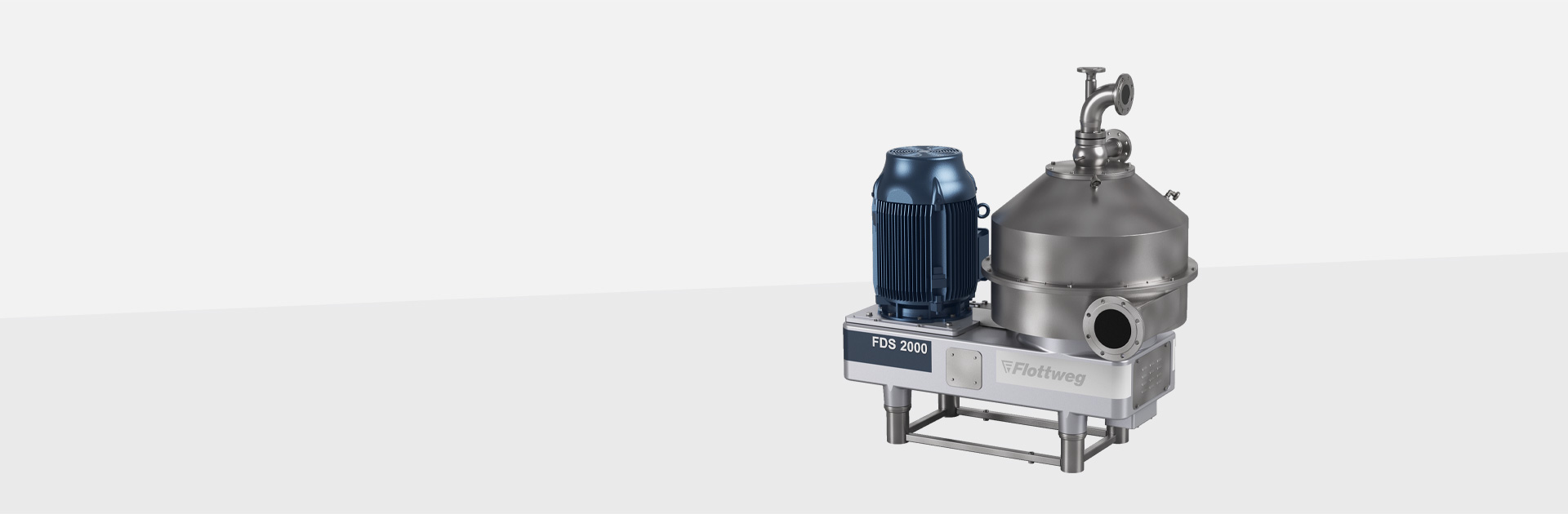
Flottweg Nozzle Separator
Energy-saving, maintenance-optimized and powerful
Nozzle separators for the continuous separation of solids from liquidsIn the starch industry in particular, as well as in many other applications, maximum clarification or separation with high quantities of solids is required.
Experience the power of Flottweg’s German-made Nozzle Separator. Our technology ensures continuous, energy-saving separation of high solids concentrations, ideal for the food and starch industry. With easy maintenance, low energy consumption, and high flexibility, our Nozzle Separator meets hygienic requirements. Its robust, compact design and high performance make it a leading choice in the industry. Discover how Flottweg is optimizing separation processes. Get in touch today to learn more!

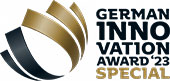
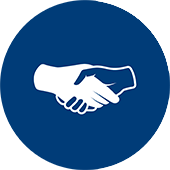
Developed with and for our customers
The Flottweg nozzle separator was specially developed for these applications together with and for our customers.
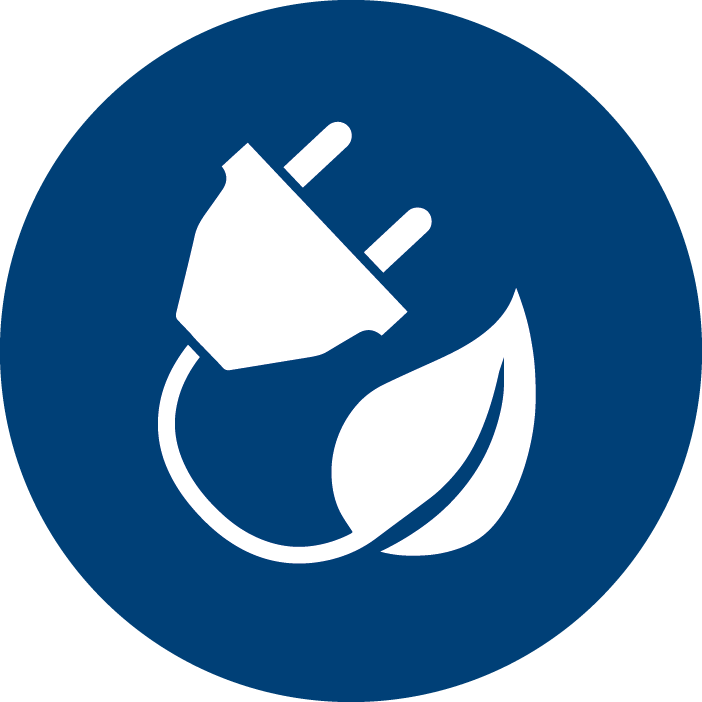
Low energy consumption
Flottweg nozzle separators are characterized above all by high performance and their low energy consumption.
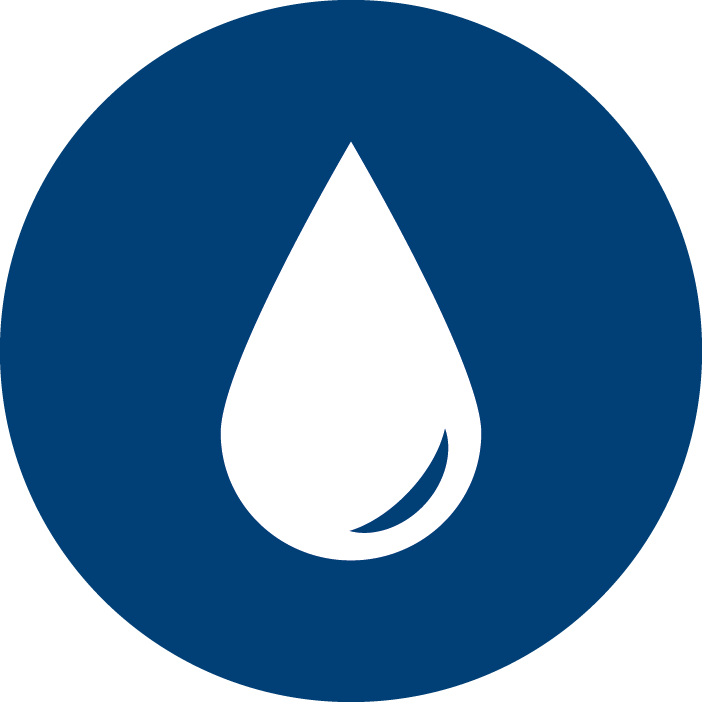
High clarification and separation performance for solids and liquids
Our FDS series nozzle separators have the largest possible clarification area and can process large quantities of solids due to the continuous discharge of solids. Customers receive consistently pure solids in the concentrate phase. At the same time, the clarified phase is optimally cleaned and is ready for subsequent separation processes.
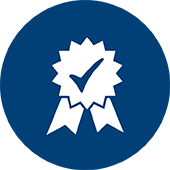
Robust and compact design "Made in Germany"
Flottweg manufactures its machines exclusively in Germany; in addition to low operating costs and high performance, our customers attach great importance to a robust and compact design. By combining durable and high-quality materials, we meet our customers' optimal requirements.
The Flottweg nozzle separators are available in two basic designs
2-phase nozzle separators serve to separate solids from liquids, thus making highly efficient clarification possible.
In addition to separating solids from liquids, 3-phase nozzle separators are used to fractionate different particle sizes.
Fields of application for nozzle separators
How does the Flottweg nozzle separator work?
Flottweg nozzle separators (2- and 3-phase nozzle separators) are used for the continuous separation of solids from liquids and ensure highly efficient clarification or separation. The product to be clarified or separated flows via a stationary inlet pipe into the inside of the bowl and is gently accelerated to operating speed by the distributor.
Large solid particles are separated directly in the centrifugal field of the 2-phase nozzle separator. Finer solids are separated when flowing through the disc stack. The solid particles collect in the bowl’s outer solids chambers. From there, they are continuously discharged via the nozzles. The clarified liquid flows from the disc stack and is discharged under pressure by an impeller.
With 3-phase nozzle separators, larger solid particles are separated as they flow through the disc stack and are directed to the edge of the bowl as a result of the high centrifugal force. There, they collect in the bowl's outer solids chambers and are continuously discharged through the nozzles. The remaining product flow is divided into a fraction and a clarified phase. Solids with a smaller particle size form the fraction, which is discharged under pressure. The remaining liquid flows through the disc stack, creating a nearly clear clarified phase. This is also discharged under pressure via an additional impeller.
The bowl can optionally be equipped with a washing or recirculation device, which is characterized by a contactless and therefore maintenance-free sealing system. This device enables process / washing water or already-concentrated product to be dispensed directly into the solids chambers upstream of the nozzle outlet. This allows the separation result to be improved and allows product fluctuations to be leveled in a process-safe manner.
Characteristics of our nozzle separators
Energy-optimized and low-wear bowl design
Our separation technology experts have developed the Flottweg nozzle separator in collaboration with our customers. The goal: a nozzle separator perfectly tailored to the needs of our customers. The result: an innovative, energy-optimized low-wear design.
Throughout the development of our nozzle separators, the focus was on maximum energy savings, and thus on low energy costs. Our revolutionary bowl design saves drive energy. In addition, the bowl of our nozzle separator is significantly lighter than conventional bowls and therefore requires less drive energy. The separator bowl design ensures reliable and low-vibration operation. Solids chambers integrated into the bowl prevent uncontrolled sediment formation and can avoid vibration. The concentrate can be conveyed out of the bowl via the solids chambers without leaving deposits. The size of the nozzles' outlets is optimally adapted to the respective process and to the product to be processed.
- Machine design adapted to the needs of our customers.
- The innovative interior design of the bowl ensures maximum running smoothness and fulfills hygiene requirements.
- The system can be optimally adapted to the product to be processed by quickly and easily changing the carbide nozzles.
- Low energy consumption thanks to energy recovery and lightweight construction.
High performance
The rapid acceleration of separators depends on a powerful drive with a long service life. Flottweg supplies a standard three-phase AC motor to provide the necessary power. It transmits the power to the bowl spindle by means of a belt and runs very smoothly. The speed can be easily and flexibly adapted to the respective product conditions via a frequency converter. The separator quickly reaches full operating speed. At the same time, the inverter reduces both the power consumption and the mechanical load on the system. A completely closed lubricating circuit system protects the spindle bearings. Full lubrication capacity is available during the start-up and shut-down of the machine, which ensures that the bowl’s bearings have a long service life. A pump unit ensures exact and demand-oriented metering of the lubricating oil.
- Powerful three-phase motor with belt drive.
- Rapid acceleration with extremely smooth running.
- Flexible speed regulation via frequency converter.
- Completely closed, efficient lubrication circuit system.
Simple and fast maintenance
Fast and predictable maintenance makes a decisive contribution to smooth operation. The innovative design of the separator bowl prevents wear. The arrangement of the nozzles creates a natural wear protection of solid material in the bowl. The nozzles of the Flottweg Nozzle Separator are equipped with carbide wear protection for maximum service life. These nozzles can be replaced quickly and easily via a maintenance opening in the housing. The nozzle separator's compact spindle drive is also optimized for minimum downtime during maintenance. This can be removed quickly and easily with little effort. The separator drive belt can be easily retightened or quickly replaced through a maintenance opening. High-quality materials 'Made in Germany' ensure that maintenance intervals are extended. For our customers, this means higher availability and low costs.
Flottweg has a worldwide service network of competent service technicians for maintenance and servicing. This means that your local service partner is quickly available should service be required.
- Closed-loop lubrication system reduces wear.
- Natural wear protection is given to solid material thanks to innovative bowl design.
- Carbide wear protection for long nozzle life.
- Belt drive for high machine availability.
- The compact spindle drive can be dismantled by means of just four screws.
- Extended maintenance intervals for high availability.
- Worldwide service network.
Designed for perfect hygiene
Whether food, biotechnology, or chemicals, Flottweg separators are fully equipped to meet the hygienic requirements in highly regulated industries. They meet all requirements of the applicable centrifuge standard and are constructed according to the principles of "Hygienic Design." The innovative solids chambers in the separator bowl ensure that the concentrate is discharged from the bowl without deposits and that no deposits remain when the machine is shut down. All components of the separator that come into contact with the product are made of high-quality stainless steel. The hygienic design of the Flottweg nozzle separator avoids dead spaces and thus enables easy cleaning of the centrifuge. In the food and biotechnology industries, all components that come into contact with the product are CIP-capable (Clean-in-Place) and can be easily integrated into existing cleaning processes.
- Construction according to the principles of Hygienic Design.
- Deposit-free solids discharge.
- Components that come into contact with the product are made of high-quality stainless steel.
- Easy integration into CIP processes.
Technical data of our Flottweg FDS Nozzle Separators
FDS2000 Concentrator
Dimensions [mm/ft]* | 2000x1200x2200 / 6.56x3.94x7.22 |
Weight [kg/lb]* | 2800 / 6170 |
FDS2000 Clarifier
Dimensions [mm/ft]* | 2000x1200x2200 / 6.56x3.94x7.22 |
Weight [kg/lb]* | 2800 / 6170 |