18.04.2024
Rozwiązywanie problemów z wodą w kopalniach i kamieniołomach – zastosowanie technologii wirówki z klarownikiem i stacją dozowania polimerów
W miarę starzenia się kopalni i kamieniołomów górnicy i operatorzy stają przed problemami z wodą niezbędną do płukania i przetwarzania produktów. Problemy te obejmują brak miejsca na osadniki, konieczność prowadzenia prac wydobywczych pod istniejącymi osadnikami, niedobór wody z powodu ograniczeń, limity specyfikacji wody, którą można odprowadzić z powrotem do wód gruntowych, oraz zbyt dużą ilość wody zanieczyszczonej gliną i substancjami ultradrobnymi.
Tradycyjnym rozwiązaniem było stosowanie pras filtracyjnych i osadników. Ta technologia nie tylko wiąże się ze znacznymi inwestycjami kapitałowymi, ale wymaga również dużej przestrzeni i stałej obecności operatora oraz generuje stałe koszty operacyjne związane z mediami filtracyjnymi. Prasy i osadniki nie są przenośne, a związane z nimi koszty budowlane/konstrukcyjne zwiększają nakłady inwestycyjne. Z drugiej strony składowanie odpadów przeróbczych w osadnikach nie jest preferowanym rozwiązaniem, ponieważ powoduje kwarantannę znacznej części kopalni.
Niezawodną i opłacalną alternatywą może być omawiana w niniejszym opracowaniu technologia, badana w dwóch instalacjach pilotażowych, składających się z klarownika z jednostką dozowania polimerów oraz wirówki dekantacyjnej, zaprojektowanej specjalnie z myślą o trudnych warunkach w górnictwie. Zakład pilotażowy pracował równolegle z prasą filtracyjną o równoważnej wielkości w jednej lokalizacji przez jeden tydzień i w oddzielnej lokalizacji przez kolejny tydzień. Oba testy wykazały imponującą suchość fazy stałej, minimalne zużycie polimerów i klarowny odciek.
Wstęp
W lipcu i sierpniu 2022 r. przeprowadzono operacje pilotażowe w dwóch oddzielnych, niezależnych myjniach piasku i żwiru w południowo-wschodnim Wisconsin, USA. Zakład nr 1 znajdował się w kopalni Lisbon w firmie Lannon Stone Products, Inc. w Sussex (Wisconsin) i jest tutaj określany jako „Lannon”. Reprezentatywny dla tego regionu teren kopalni charakteryzuje się typową mieszanką materiałów morenowych, obejmującą osady, glinę i kamienie pokrywające wapień dolomityczny. Wapień zawiera różne ilości rogowca i gliny.
Kopalnia Lannon produkuje wielkogabarytowy kamień budowlany oraz piasek i żwir. Żwir obejmuje kamień łamany, żwir grochowy i kruszywo. Piasek jest klasyfikowany w różnych klasach zastosowania, tj. piasek płukany do betonu, piasek murarski, piasek podsypkowy, piasek na pola golfowe i ultradrobny piasek płukany. W Lannon zużyta woda płucząca trafia do klarownika. Po dodaniu polimerów, dozowanych przez stację Clearwater Industries Inc., woda jest pozostawiana do wytrącenia osadu w klarowniku.
Przelew klarownika jest kierowany bezpośrednio z powrotem do myjni, a osady denne są przesyłane w dwóch kierunkach. Prawie połowa osadów dennych jest przekazywana bezpośrednio do nowej komorowej prasy filtracyjnej 2 m x 2 m, a reszta do tradycyjnych osadników/stawów retencyjnych. To właśnie te osady denne stanowią materiał doprowadzany do wirówki.
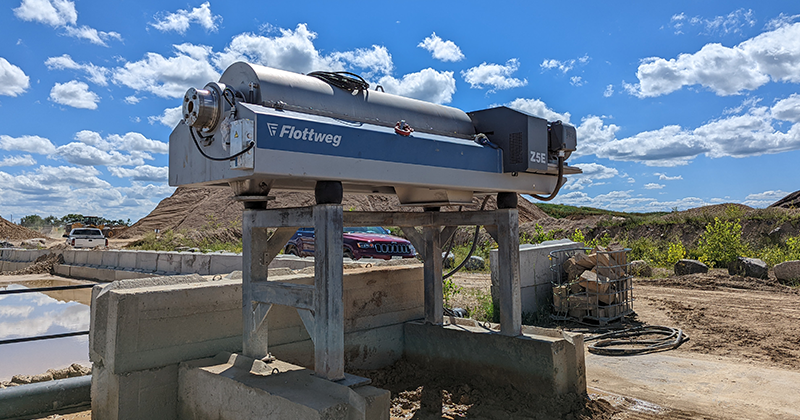
Zakład nr 2 znajdował się w centralnej myjni firmy Tri-County Paving, Inc. w Arlington w stanie Wisconsin (USA) i jest tutaj określany jako „Tri-County”. W zakładzie tym odbywają się ogólne operacje odbioru, przechowywania, mieszania i mycia dla wielu kamieniołomów i kopalni – zarówno w ramach działalności Tri-County Paving, jak i poza nią. W związku z tym zakres minerałów jest nieco szerszy niż w Lannon, ale geologia regionalna dyktuje, że większość przetwarzanych materiałów nadal składa się z podstawowej mieszanki charakterystycznej dla warstwy morenowej pokrywającej wapień dolomityczny.
Zaawansowane urządzenia do mieszania i załadunku w Arlington umożliwiają firmie Tri-County oferowanie klientom produktów o bardzo rygorystycznych specyfikacjach i wąskich tolerancjach. Woda z myjni piasku przechodzi przez jednostkę dozowania polimerów Clearwater Industries, a następnie przekazywana jest do klarownika Clearwater. Woda odzyskana z przelewu klarownika jest zwracana do zbiornika retencyjnego wody płuczącej, natomiast osady denne są kierowane bezpośrednio do jednej z dwóch zapór osadowych, aby odsączyć nadmiar wody. Osady denne z klarownika są pobierane i podawane do wirówki. Procentowy udział fazy stałej był znacznie wyższy niż w zakładzie w Lannon (zazwyczaj blisko 55% masy DS).

W obu przypadkach (Lannon i Tri-County) istniała taka sama potrzeba separacji – z wody użytej do płukania piasku trzeba było usunąć cząstki gliny i ultradrobnych osadów, aby mogła zostać ponownie wykorzystana. Cały piasek jest płukany w myjni, zaś w rezultacie tego procesu woda płucząca jest zanieczyszczona materiałem organicznym, pozostałościami z robót strzałowych, gliną i ultradrobnymi cząstkami.
Przechowywanie zanieczyszczonej wody w osadnikach w celu odparowania było nieopłacalne, a osadniki zajmowały przestrzeń, która mogłaby być bardziej rentownie wykorzystana do przyszłego wydobycia. Ponadto w obecnej postaci wody nie można było odprowadzić z powrotem do wód gruntowych. W obu przypadkach właściciele kopalni wybrali klarownik podłączony do jednostki dozowania polimerów firmy Clearwater Industries, aby zapewnić dokładne dozowanie flokulantu.
Cel badań pilotażowych
Głównym celem projektów pilotażowych było zademonstrowanie, że łącząc wirówkę z odpowiednim klarownikiem i prawidłowo skalibrowaną stacją dozowania polimerów można:
- odzyskać wodę płuczącą do ponownego użycia,
- wytworzyć fazę stałą wystarczająco suchą, aby mogła być rozładowywana zamiast wypompowywana,
- zaoszczędzić lub całkowicie wyeliminować konieczność rezerwowania miejsca na osadnik, a jednocześnie
- działać w opłacalny sposób przy minimalnym nadzorze.
W obu próbach jednostka pilotażowa osiągnęła optymalną wydajność operacyjną w ciągu kilku godzin od instalacji, przekraczając parametry docelowe badania. Wykorzystano możliwość przetestowania różnych scenariuszy z zastosowaniem różnych prędkości podawania oraz prędkości obrotowych bębna i ślimaka wirówki. Celem było ustalenie, czy można pomyślnie osiągnąć różne optymalne kombinacje podawania / prędkości różnicowej pomiędzy bębnem a ślimakiem wirówki.
Zbadano również różnice w dozowaniu polimerów, aby sprawdzić, czy istnieje więcej niż jedno optymalne ustawienie produkcji dla każdego scenariusza objętości/prędkości. Przejrzystość powstałego odcieku (odprowadzanej cieczy) i suchość fazy stałej (DS) mierzono w odniesieniu do podawanego materiału przy każdym ustawieniu. Zarówno stację dozowania w klarowniku, jak i wirówkę można szybko ponownie skalibrować, co pozwala na zrealizowanie 18 oddzielnych scenariuszy w każdej lokalizacji.
Metodologia
Wybrana wirówka dekantacyjna marki Flottweg, model Z5E-4/451, została wyposażona w pakiet chroniący przed zużyciem w warunkach górniczych, aby zapewnić ochronę bębna, ślimaka oraz wszystkich punktów wlotowych i wylotowych urządzenia przed zużyciem ślizgowym, które towarzyszy typowemu materiałowi górniczemu znajdującemu się w osadach dennych z klarownika.
Testy pilotażowe obejmowały wirówkę dekantacyjną, stalowy podest i panel sterowania. Obejmowały również pompę zasilającą z magazynu producenta OEM, która została dostarczona wraz z małym zbiornikiem retencyjnym. Pompa zasilająca jest ważna dla utrzymania nadciśnienia w strumieniu podawanego materiału. Mały zbiornik retencyjny (choć zwykle nie jest wymagany do celów testowych) był praktyczny, ponieważ miał dostęp od góry i umożliwił członkom zespołu łatwe wizualne monitorowanie podawanego materiału w celu potwierdzenia odczytów gęstościomierza.
W linii podawania materiału do wirówki zamontowano następujące urządzenia: -
- gęstościomierz rejestrujący procentową zawartość substancji stałych zawieszonych w podawanym materiale;
- przepływomierz rejestrujący liczbę galonów amerykańskich na minutę całkowitego strumienia podawanego materiału; oraz
- przepływomierz rejestrujący liczbę galonów amerykańskich na minutę roztworu polimeru podawanego do strumienia materiału. Ta ostatnia linia była również monitorowana przez jednostkę dozowania polimerów Clearwater Industries Inc, która bardzo precyzyjnie dozowała polimer do tej linii, a tym samym do strumienia materiału.
Panel sterowania wirówki jest podłączony do wszystkich przyrządów i monitoruje wszystkie aspekty operacji. Natychmiastowe i automatyczne korekty uwzględniają zmiany objętości lub gęstości podawanego materiału – sterowniki nadrzędne wybierają wszelkie wymagane zmiany prędkości obrotowej bębna i ślimaka, ich różnicowej prędkości obrotowej, a także ilości dozowanego polimeru, aby utrzymać stan stabilny. Łożyska są monitorowane pod kątem wszelkich zmian drgań, podobnie jak zasilanie elektryczne.
W przypadku utraty zasilania wirówka automatycznie odcina podawanie i opróżnia bęben z substancji stałych. Przywrócenie zasilania w dowolnym momencie spowoduje automatyczny powrót urządzenia do stabilnego stanu produkcji, niezależnie od tego, która część cyklu została przerwana.
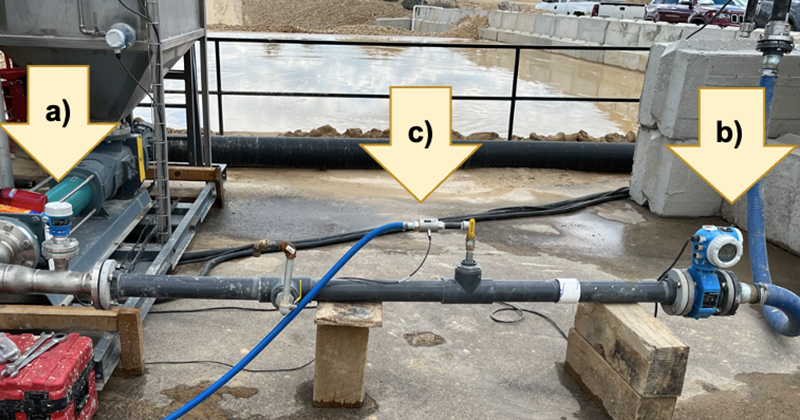
Analiza
W każdym zakładzie utworzono terenowe laboratorium do analizy fazy stałej (DS) w pobranych próbkach podawanego materiału, odcieku i placka. Pobrano również duplikaty próbek do badań w laboratoriach Flottweg, które przeprowadziły dodatkowe analizy, w tym całkowitej zawartości zawiesin substancji stałych (TSS) w próbkach podawanego materiału i odcieku. Próbkę podawanego materiału i odcieku z zakładu Tri County w USA przesłano do laboratorium badawczego Clark w celu przeprowadzenia analizy rozkładu wielkości cząstek, zaś próbki z zakładu Lannon zostały w tym celu przebadane we własnym laboratorium Flottweg w Niemczech.
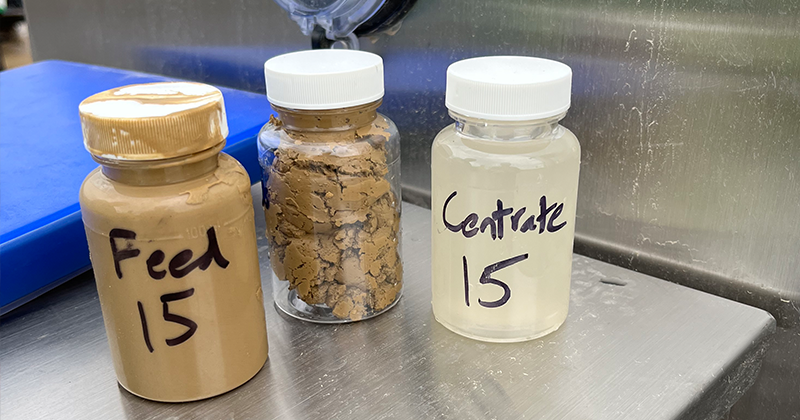
Osady denne były wyprowadzane z klarownika do prostego zbiornika retencyjnego, aby umożliwić operatorowi wizualną kontrolę podawanego materiału – jak wspomniano wcześniej, zbiornik ten nie jest zwykle wymagany, ale został zastosowany w instalacjach pilotażowych po prostu dlatego, że zbiornik był już zamontowany na podstawie pompy zasilającej. Zawartość tego zbiornika retencyjnego była następnie stale odpompowywana z punktu poboru na linii. Ciśnienie podawania było nieznaczne, zastosowano nie więcej niż jeden lub dwa bary (15–30 psi) ciśnienia dodatniego, aby upewnić się, że w wirówce nie brakuje materiału wejściowego.
Wirówka grawitacyjnie odprowadza strumienie ciał stałych i cieczy. W odpowiednich istotnych punktach instalacji okresowo pobierano próbki podawanego materiału, fazy stałej i odcieku. Próbki zostały również przesłane do laboratorium zewnętrznego w celu uzyskania danych dotyczących rozkładu wielkości cząstek (PSD), jak poniżej:
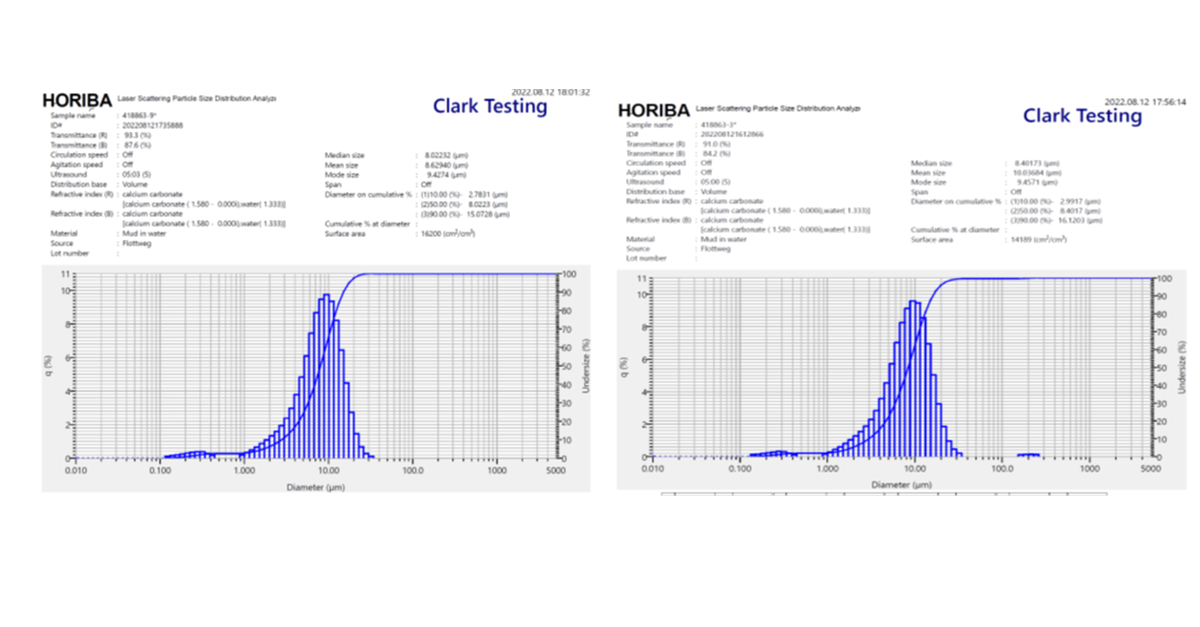
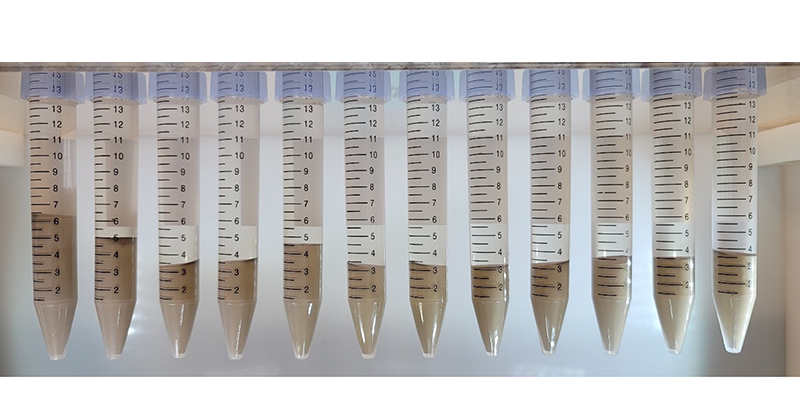
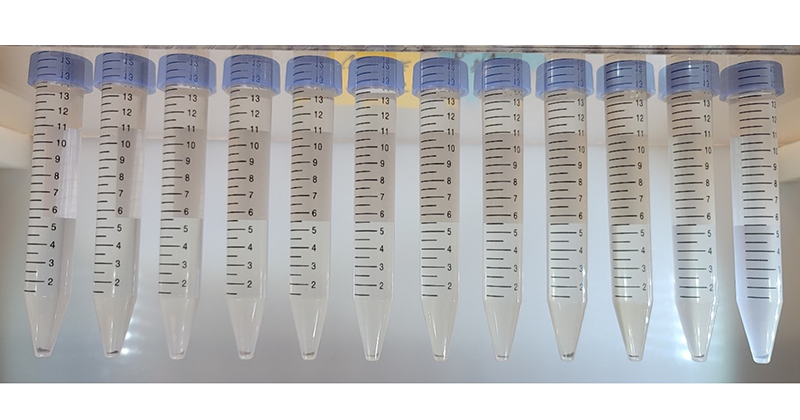
Przygotowanie polimerów
Polimery przygotowano przy użyciu systemu Clearwater. Zastosowano suchy polimer CW95V w Tri County i CW16 w Lannon. Przygotowano roztwór polimerów o aktywnym stężeniu 0,25%, który został użyty podczas wszystkich badań instalacji pilotażowych. Następnie obliczono zużycie polimerów na podstawie natężenia przepływu roztworu polimerów i prędkości podawania fazy stałej. Jednostką zużycia polimerów jest funt aktywnego polimeru na suchą tonę podawanego materiału (lb ap/suchą tonę).
Jakość separacji
Jakość oddzielania mechanicznego jest oceniana na podstawie odzysku zawiesin, procentowej zawartości całkowitej substancji stałych w odwodnionym placku i zużycia polimerów. Jakość tych kryteriów zależy od dostosowania parametrów roboczych. Jakość odzysku cząstek stałych można ocenić wizualnie. Szybkie informacje zwrotne umożliwiają optymalizację w celu uzyskania możliwie najsuchszej fazy stałej z dopuszczalną jakością odcieku.
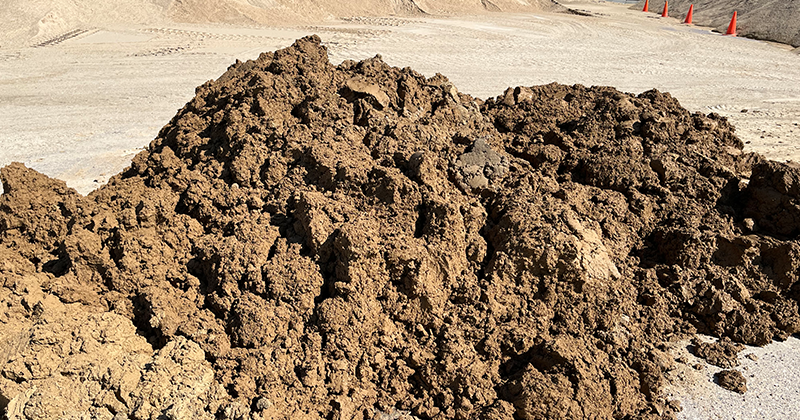
Wyniki
Zakresy parametrów i osiągane wyniki przedstawiono w tabelach 1 i 2. Wszystkie wyniki poszczególnych badań znajdują się w załączniku. Należy zauważyć, że badanie 8 w Tri County miało widocznie słabą jakość odcieku, a badanie 13 w tym samym zakładzie wykazało błąd odczytu DS i próbki nie zostały pobrane.
Tabela 1. Zakresy parametrów roboczych.
Prędkość/przyspieszenie bębna | 1292 - 1838 | rpm |
494 - 999 | x g | |
Prędkość podawania (min.–maks.) | 26 - 90 | gpm |
1578 – 18 739 | sucha masa lb/godz. |
Tabela 2. Zakresy osiąganych wyników.
Odciek z wirowania | 0,040 – 0,221 | % TS |
0,001 – 0,155 | % TSS | |
Placek | 69,3 – 77,1 | % TS |
Odzysk (TSS) | 99,9 – 100 | % |
Siła g
Wpływ siły g na wydajność jest badany poprzez regulację prędkości bębna przy jednoczesnym utrzymaniu stałych warunków i parametrów pracy. Następnie moment obrotowy jest regulowany w celu uzyskania jak najsuchszego placka. Suchość placka mieściła się w przedziale od 69,3 do 77,1% masy TS, przy czym suchszy placek obserwowano przy wyższej sile g. Wyniki przedstawiono poniżej:
Dozowanie polimerów
Ponieważ polimer wiąże ze sobą cząstki stałe, ilość dozowanego polimeru ma wpływ na osiągalną separację. Zmieniając ilość polimerów przy jednoczesnym utrzymaniu stałych parametrów i warunków pracy można ustalić krzywą polimerów i określić optymalny zakres dozowania polimerów. Stwierdzono, że optymalna dawka polimerów wynosi 0,20–0,27 lb ap/suchą tonę, natomiast po zwiększeniu dawki polimerów do ponad 0,35 lb ap/suchą tonę wystąpiło niewielkie zmniejszenie uzyskiwanej suchości placka.
Ta bardzo mała objętość polimerów potrzebna do konsekwentnego wytwarzania uzyskiwanego % suchej masy stałej była mile widzianym potwierdzeniem, że zazwyczaj bardzo wysokie dawki stosowane w branży przy wspomaganiu separacji są zbędne, a zbyt wysokie dawki utrudniają separację. Staranne testy podczas pierwszej instalacji zapewnią doskonałą separację przy niskiej dawce.
Wnioski
Wirówka dekantacyjna w połączeniu z klarownikiem i jednostką dozowania polimerów jest bardzo ekonomicznym i skutecznym rozwiązaniem, pozwalającym zaoszczędzić 90% miejsca przeznaczanego na osadniki, a nawet więcej. Umożliwia też odzyskanie do 90% wody używanej do płukania. Uzyskana faza stała jest na tyle sucha, że można ją przenosić łopatą i nadaje się do transportu przenośnikiem lub ciężarówką. Niezwykle dobrze sprawdza się odzyskiwanie wody pochodzącej z procesu mycia piasku i żwiru za pomocą wirówki dekantacyjnej chronionej przed zużyciem w połączeniu z klarownikiem/odpowiednią jednostką dozowania polimerów. Wyniki uzyskane podczas tych testów w Stanach Zjednoczonych korelują w 100% z wynikami uzyskanymi w wielu obecnych instalacjach w Europie.
Prawie wszystkie (+99,9%) zawiesiny są usuwane z wody płuczącej, a uzyskana faza stała nadaje się do przenoszenia łopatą i może być usuwana za pomocą przenośnika taśmowego, przenośnika ślimakowego lub ciężarówki. W stanie stabilnym można spodziewać się typowej suchości od ≥69% aż do 77% (masa DS).
Ilość polimerów wymaganych do wspomagania separacji była minimalna. Zazwyczaj oczekuje się od 500 g do nawet 2 kg polimerów na tonę suchego materiału. Wirówka była w stanie osiągnąć odzysk substancji stałych +99,9% i odwodnić placek do suchości 69%–77% TS przy dawkach polimeru 0,17–0,44 lb ap/suchą tonę (77 g–199 g na suchą tonę). Osiągnięto stałe prędkości podawania w zakresie od 26 do 90 galonów na minutę (98–341 litrów na minutę). Oznacza to od 5,9 do 20,4 m³/godz.
Odciek jest czysty i w pełni nadaje się do ponownego użycia jako woda płucząca, co pozwala kopalni zaoszczędzić nawet 90% zapotrzebowania na wodę do płukania. Zapotrzebowanie na energię elektryczną jest stałe i przewidywalne. Wymagania w zakresie nadzoru operatora i okresowej konserwacji są bardzo niewielkie, a system jest zabezpieczony przed awarią, aby zapewnić brak negatywnego wpływu nagłego wzrostu ilości ciał stałych w podawanym materiale, awarii podajnika lub przerw w zasilaniu.
Eric Gentis, Flottweg Separation Technology i Andrew Gralton, Clearwater Industries Inc.
[Wkład innych autorów] W opracowaniu tego raportu pomogli Stefan Ecker, Joe Lamb, Terry Ostrom, Martin Eckl, Robert Klug, Tony Kramer i Dustin Miller z Flottweg Separation Technology oraz właściciele i zespoły z Lannon Stone Products, Inc. w Sussex (Wisconsin, USA) oraz Tri-County Paving Inc w DeForest (Wisconsin, USA)