29.07.2024
Zakład rekultywacji wody w Ohio osiąga poprawę wydajności i oszczędności na kosztach operacyjnych.
Uzyskanie jednorodnego placka z fazy stałej to tylko jedna z zalet nowej technologii oddzielania w oczyszczalni ścieków, która obsługuje prawie 50 000 osób na północnym zachodzie stanu Ohio. Dodatkową korzyścią związaną z wymianą prasy taśmowej na dekanter z wirówką były znaczące oszczędności na kosztach związane z mniejszym zużyciem środków chemicznych w procesie.
W ciągu zaledwie dwóch lat od rozpoczęcia działalności zakład rekultywacji wody w Middletown zainstalował wirówkę dekantacyjną, która skróciła czas produkcji o dwa dni tygodniowo, zwiększyła wydajność i pozwoliła zaoszczędzić tysiące litrów substancji chemicznych rocznie, co przełożyło się na znaczące oszczędności.
Tło
Oczyszczalnia ścieków przedsiębiorstwa komunalnego w Middletown w stanie Ohio może przyjąć i oczyścić 26 milionów galonów wody (MGD) dziennie. Przedsiębiorstwo chroni zdrowie mieszkańców i środowisko, odzyskując każdego dnia średnio 14,5 miliona galonów ścieków ze wszystkich źródeł: mieszkalnych, komercyjnych i przemysłowych.
Z tego procesu recyklingu pochodzą dwa produkty: czysta woda odprowadzana do rzeki Great Miami oraz około 1500 ton rocznie suchych osadów ściekowych, które są rozrzucane na polach uprawnych jako źródło składników odżywczych i uzdatniających glebę. Przepływ projektowy zakładu rekultywacji wody wynosi 26 MGD. Połączenie systemu pozwala obsłużyć szczytowy przepływ na poziomie do 50 MGD.
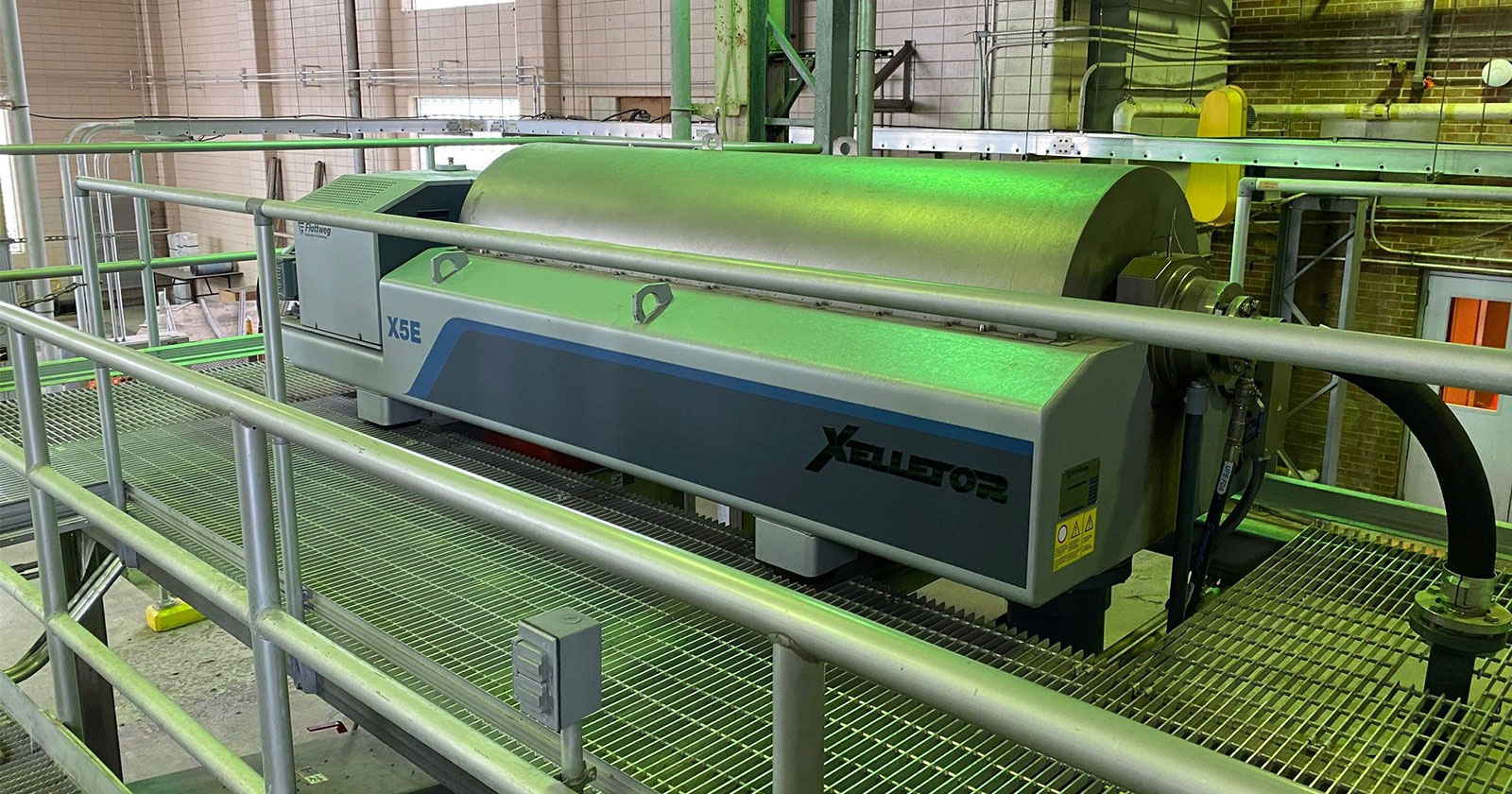
Wyzwanie i rozwiązanie
W zakładzie rekultywacji wody korzystano wcześniej z prasy taśmowej i wirówki, ale urządzenia te nie działały prawidłowo. W 2018 r. firma usunęła prasę taśmową, ponieważ technicy mieli trudności z jej obsługą i produkowała ona zaledwie od 15 do 18% fazy stałej. Zaledwie dwa lata później wirówka wytwarzała około 30% fazy stałej, a jej sprawność została utrzymana.
„Zależało nam na większej jednorodności fazy stałej, co pozwoliłoby obniżyć koszty transportu” — wyjaśnia kierownik Gerry Burris. „Potrzebowaliśmy czegoś podobnego do posiadanej przez nas maszyny, która stwarzała wiele problemów mechanicznych i której producent nie mógł zapewnić właściwej obsługi.
W 2018 r. zakład zainstalował wirówkę Xelletor firmy Flottweg, dzięki czemu skróciliśmy czas produkcji z pięciu do trzech dni w tygodniu (przechodząc z 8 na 10 godzin dziennie). Starsza wirówka została zachowana w rezerwie, natomiast prasa taśmowa została usunięta.
„Dzięki krótszej pracy mogliśmy nadal przemieszczać produkt bez ponoszenia kosztów operacyjnych oraz wykorzystania środków chemicznych pięciu dni eksploatacji tygodniowo” — wyjaśnia Burris. „Obecnie zużywamy mniej paliwa i osiągamy większą wydajność niż wtedy, gdy sprzęt pracował przez pięć dni w tygodniu”.
Jak podkreśla Burris, dzięki samodzielnej instalacji maszyny, która działała bezproblemowo, udało się uzyskać znaczące oszczędności. „Mieliśmy kilka problemów z uruchomieniem, ponieważ operatorzy próbowali obsługiwać maszynę jak wcześniej” — dodaje. „Byli przyzwyczajeni do innych elementów sterowania, ale firma Flottweg wykonała świetną robotę polegającą na zintegrowaniu ekranów, które wyglądały podobnie do dotychczasowych. To ułatwiło przejście”.
Ponadto bardziej wydajny dekanter dał zakładowi możliwość wprowadzenia wielu zmian w ogólnej działalności i wykorzystaniu środków chemicznych. „To było jak niebo a ziemia” — wyjaśnia Burris. „Instalacja dekantera marki Flottweg przyniosła znaczne oszczędności w zużyciu środków chemicznych.Nie zużywamy już tyle polimeru ani chlorku żelaza”.
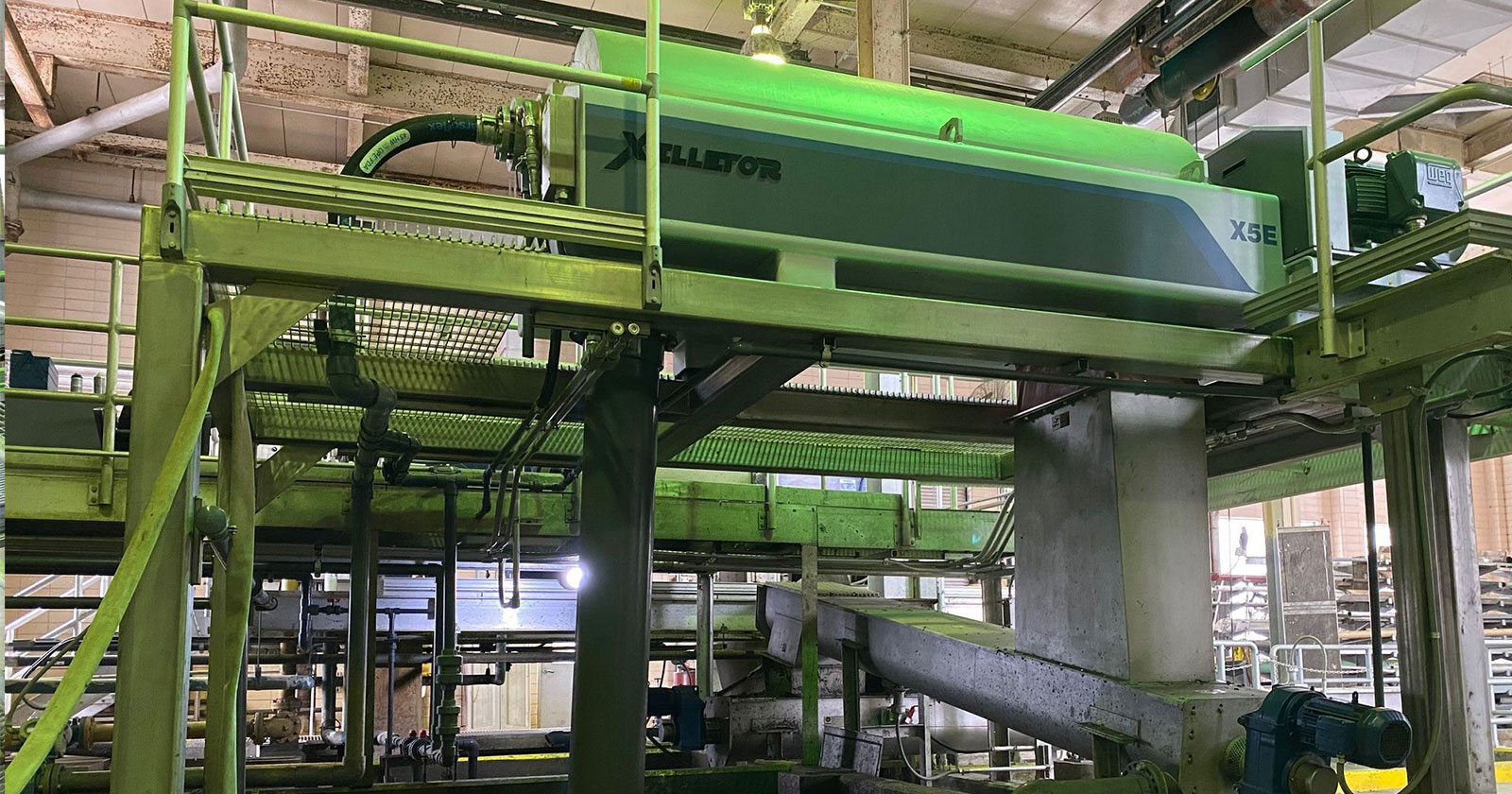
W zakładzie rekultywacji wody korzystano wcześniej z prasy taśmowej i wirówki, ale urządzenia te nie działały prawidłowo. W 2018 r. firma usunęła prasę taśmową, ponieważ technicy mieli trudności z jej obsługą i produkowała ona zaledwie od 15 do 18% fazy stałej. Zaledwie dwa lata później wirówka wytwarzała około 30% fazy stałej, a jej sprawność została utrzymana.
„Zależało nam na większej jednorodności fazy stałej, co pozwoliłoby obniżyć koszty transportu” — wyjaśnia kierownik Gerry Burris. „Potrzebowaliśmy czegoś podobnego do posiadanej przez nas maszyny, która stwarzała wiele problemów mechanicznych i której producent nie mógł zapewnić właściwej obsługi.
W 2018 r. zakład zainstalował wirówkę Xelletor firmy Flottweg, dzięki czemu skróciliśmy czas produkcji z pięciu do trzech dni w tygodniu (przechodząc z 8 na 10 godzin dziennie). Starsza wirówka została zachowana w rezerwie, natomiast prasa taśmowa została usunięta.
„Dzięki krótszej pracy mogliśmy nadal przemieszczać produkt bez ponoszenia kosztów operacyjnych oraz wykorzystania środków chemicznych pięciu dni eksploatacji tygodniowo” — wyjaśnia Burris. „Obecnie zużywamy mniej paliwa i osiągamy większą wydajność niż wtedy, gdy sprzęt pracował przez pięć dni w tygodniu”.
Jak podkreśla Burris, dzięki samodzielnej instalacji maszyny, która działała bezproblemowo, udało się uzyskać znaczące oszczędności. „Mieliśmy kilka problemów z uruchomieniem, ponieważ operatorzy próbowali obsługiwać maszynę jak wcześniej” — dodaje. „Byli przyzwyczajeni do innych elementów sterowania, ale firma Flottweg wykonała świetną robotę polegającą na zintegrowaniu ekranów, które wyglądały podobnie do dotychczasowych. To ułatwiło przejście”.
Ponadto bardziej wydajny dekanter dał zakładowi możliwość wprowadzenia wielu zmian w ogólnej działalności i wykorzystaniu środków chemicznych. „To było jak niebo a ziemia” — wyjaśnia Burris. „Instalacja dekantera marki Flottweg przyniosła znaczne oszczędności w zużyciu środków chemicznych.Nie zużywamy już tyle polimeru ani chlorku żelaza”.
Sposób działania technologii
Odwadnianie osadu ściekowego przynosi operatorom oczyszczalni ścieków ogromne oszczędności. Koszty transportu i utylizacji odwodnionego osadu ściekowego stanowią często nawet 80% kosztów operacyjnych. W zależności od wydajności zakładu o 1% więcej substancji suchej w odwodnionym osadzie ściekowym może oznaczać nawet sześciocyfrową oszczędność kosztów.
W tradycyjnej konstrukcji wirówki mieszanina, która ma zostać rozdzielona, jest doprowadzana do maszyny rurą stacjonarną. Mieszanina przedostaje się do cylindrycznej części misy przez otwory w korpusie ślimaka, a następnie jest przyspieszana. Dzięki działaniu siły odśrodkowej w urządzeniu powstaje pierścień cieczy. Grubość pierścienia nazywana jest głębokością jeziorka. Faza stała, zwana także fazą ciężką, tworzy na ścianie bębna koncentryczną warstwę. Faza stała jest usuwana przez ślimak w stożkowej części maszyny. Oddzielona ciecz jest odprowadzana przez odpływ znajdujący się po przeciwnej stronie.
Kąt stożka, próg i korpus ślimaka ograniczają głębokość jeziorka. Niewielka głębokość jeziorka jest optymalna w przypadku mieszanin zawierających ziarnistą materię stałą, a bardziej stromy stożek lepiej sprawdza się w przypadku materii o neutralnej pływalności, ze względu na którą wymagany jest dłuższy czas pozostawania w urządzeniu w celu oddzielenia. W większości zastosowań związanych ze ściekami dobrze sprawdza się większa głębokość jeziorka.
Otwory w korpusie ślimaka, którymi mieszanina jest wprowadzana do wirówki, obłożone są twardymi okładzinami zwiększającymi odporność na zużycie. Geometria otworów została dostosowana w taki sposób, aby zapewnić łagodny przepływ cieczy, ale mimo to na mieszaninę działa siła ścinająca, co powoduje zmniejszenie skuteczności polimeru, a tym samym również skuteczności separacji.
W przypadku konwencjonalnych wirówek dekantacyjnych korpus ślimaka ogranicza głębokość jeziorka. Konstrukcja urządzenia Xelletor eliminuje te ograniczenia. Po raz pierwszy możliwe jest zastosowanie pogłębionego jeziorka, co korzystnie wpływa na kompresję, strefę oczyszczania, a ostatecznie także na wydajność separacji.
Unikalna koncepcja wirówki została opracowana specjalnie pod kątem wydajnego odwadniania osadu ściekowego. Całkowicie przeprojektowano serce konstrukcji dekantera, tj. wirnik i ślimak. W rezultacie uzyskano ślimak bez korpusu. W tym urządzeniu ciecz jest odprowadzana bezpośrednio do jeziorka w bębnie wirówki. Ciecz jest przyspieszana przy znacznie mniejszym ścinaniu, co skutkuje mniejszym zużyciem flokulantów. W pełni automatyczna regulacja prędkości bębna i prędkości różnicowej przekłada się na zawsze optymalny poziom suchej masy w odwodnionej fazie stałej – nawet w przypadku zmiennych warunków zasilania.
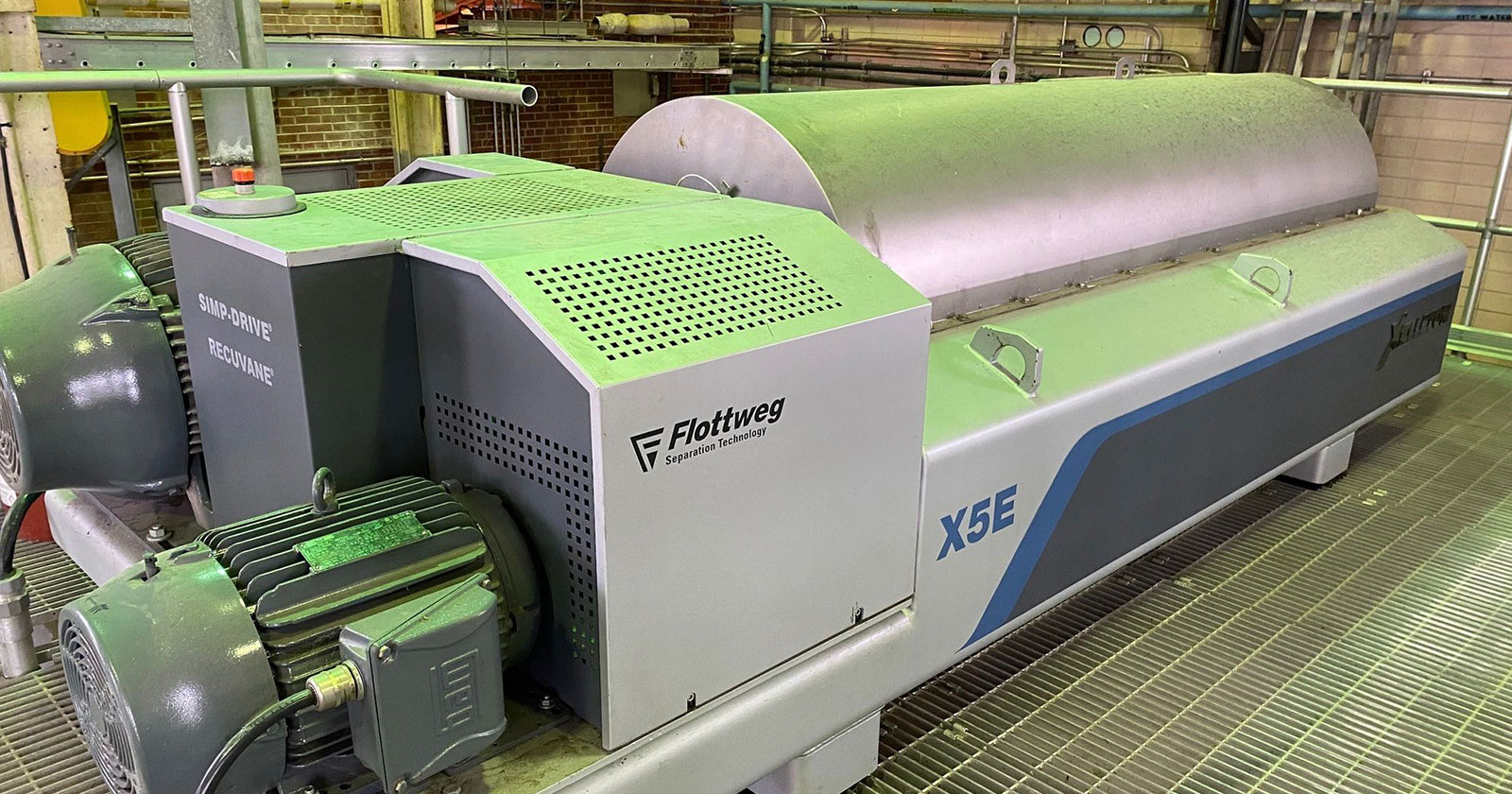
Wyniki
W Middletown, gdzie wirówka z serii Xelletor marki Flottweg wykorzystywana jest od 2018 r., uzyskano istotne oszczędności na kosztach, a także udział placka z fazy stałej na poziomie 28–30%.
„Mieliśmy pewne problemy, ale zespół Flottweg reagował bardzo szybko” – wyjaśnia Gerry Burris, odnosząc się do sytuacji, w której wymagany był montaż specjalnej części. „Rano zadzwoniliśmy do firmy Flottweg, a w ciągu godziny był już u nas jej technik, który przeprowadził montaż nowej części. Maszyna została uruchomiona ponownie jeszcze przed końcem dnia. Byliśmy pod ogromnym wrażeniem poziomu obsługi”.
Wprawdzie poprzednia maszyna pozwalała uzyskać nieco większą zawartość fazy stałej, ale wymagało to użycia znacznie większej ilości środków chemicznych – tylko po to, aby uzyskać wynik lepszy o około 1,5%.
„Musieliśmy zadać sobie pytanie, czy naprawdę potrzebujemy aż 30–31% fazy stałej” – wyjaśnia Burris. „Obecnie średni poziom uzysku fazy stałej z wykorzystaniem urządzenia marki Flottweg wynosi od 28 do 30% przy znacząco mniejszym zużyciu środków chemicznych. Doskonałym posunięciem było sięgnięcie po rozwiązanie firmy Flottweg, która błyskawicznie reaguje na nasze potrzeby. Technik przyjeżdża zawsze, gdy go potrzebujemy, i pozostaje na miejscu aż do przywrócenia właściwej pracy. Dla nas było i jest to ogromnie ważne”.
Konserwacja urządzenia z serii Xelletor nie wymaga wielu czynności. „Po każdym cyklu pracy operatorzy nakładają dwie porcje smaru na koniec łożyska i to wszystko” – dodaje Burris. „Jesteśmy bardzo zadowoleni. Uzyskujemy dobry poziom fazy stałej przy mniejszym zużyciu środków chemicznych i w krótszym czasie. Czy potrzeba nam więcej”?
O autorze
Robert Rhea jest menedżerem sprzedaży w firmie Flottweg Separation Technology, Inc. Można się z nim skontaktować pod adresem rrhea@flottweg.net.