01.06.2021
Podróż w czasie – separator marki Flottweg i jego historia
Od ponad 20 lat w asortymencie marki Flottweg znajduje się separator. W rozmowie z nami Frank Giegler, inżynier procesów w firmie Flottweg, oraz Christoph Hobmeier, inżynier ds. rozwoju w firmie Flottweg, opowiadają ekscytującą historię separatora marki Flottweg oraz wyjaśniają, w jaki sposób postęp w technologii systemowej pomógł inżynierom skuteczniej oddzielać materię stałą od cieczy.
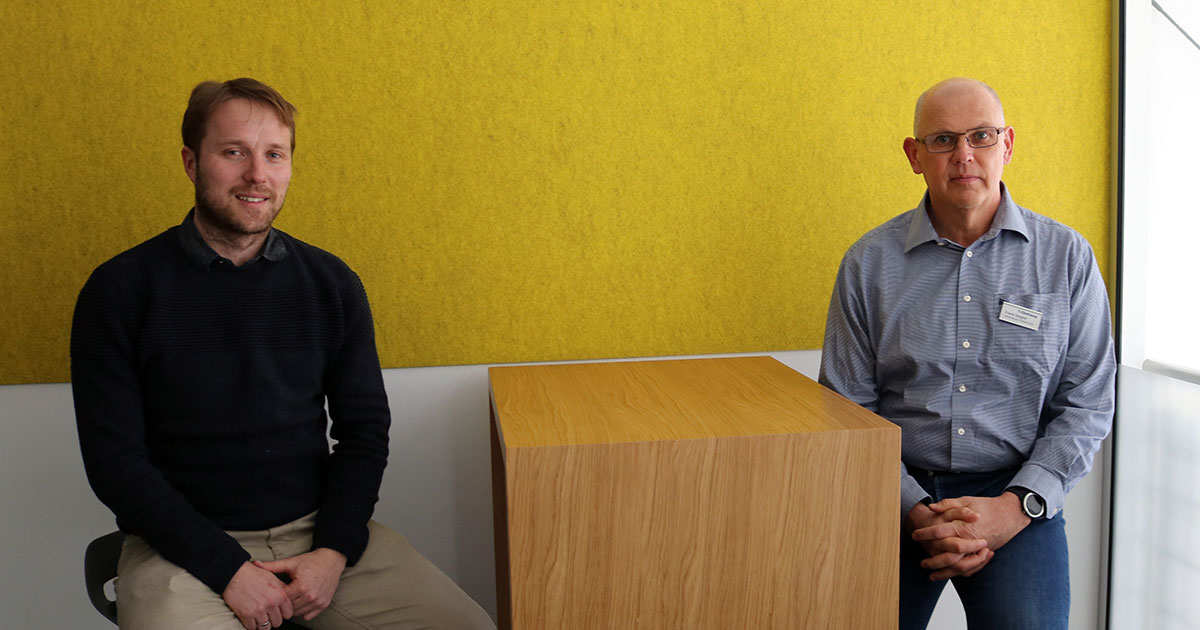
Od ponad 20 lat w asortymencie marki Flottweg znajduje się separator. Jak to się wszystko zaczęło?
Frank:
Historia separatorów marki Flottweg jest nieco dłuższa, niż sądzi się większość ludzi. Na przełomie lat 60. i 70. zaczęły się pierwsze przymiarki do opracowania separatora. Pod koniec lat 80. firma Flottweg rozpoczęła współpracę z firmą Veronesi z Bolonii we Włoszech. Firma Veronesi została później spółką zależną koncernu Flottweg. Firma Flottweg poszerzyła swoją ofertę o separatory marki Veronesi, aby móc zaoferować jednostkę oddzielającą na dalszym etapie procesu za dekanterem. Zakład produkcyjny firmy Veronesi nie nadawał się do planowanego uruchomienia produkcji modelu AC2500 (maszyna o większej wydajności), więc w 1998 r. podjęto decyzję o przeniesieniu produkcji do Vilsbiburga. Tak zaczęła się moja historia w firmie Flottweg. Model AC2500 został opracowany z myślą o zaspokojeniu potrzeb branży soków owocowych i wina. Po przezwyciężeniu kilku przeszkód rok później w naszym centrum technicznym uruchomiony został prototyp. Maszyna była następnie doskonalona w latach 1999 i 2000. W 2001 r. nadszedł wreszcie długo wyczekiwany moment: nasz obecny rzecznik zarządu, Fritz Colesan, sprzedał nasz pierwszy separator zakładowi winiarskiemu. Urządzenie pracuje tam od września 2001 r.
Co się zmieniło od czasów, w których stawiałeś tu pierwsze kroki?
Christoph:
Znacząco rozszerzyła się oferta produktowa. Zaczynaliśmy od modelu AC2500. Kolejny był model AC2000. Maszyna ta jest nieco mniejsza i oferuje o połowę mniejszą przepustowość. W toku dalszych prac powstały kolejne mniejsze modele: AC1500 i AC1200. Do dziś skonstruowaliśmy wiele wersji separatora, ale wszystko zaczęło się od dwufazowego klarownika soków owocowych. Stopniowo doszliśmy do separatorów trójfazowych, a nawet do maszyn z uszczelnieniami hermetycznymi, które są szczególnie przydatne w produkcji piwa. Obecnie możemy zaoferować szeroką gamę separatorów zaspokajających różne potrzeby. Oferujemy na przykład maszyny o wyższej odporności na korozję, pod kątem materiałów o wyższej gęstości materii stałej lub pod kątem produktów o wyższej lepkości. Pod kątem eksploatacji w strefach zagrożonych wybuchem opracowane zostały wersje z podzespołami elektronicznymi i certyfikatami EX. Są one wyposażone w nasze systemy przedmuchiwania gazem obojętnym. Urządzenia te mogą być pomocne nie tylko w zapobieganiu wybuchom podczas przetwarzania produktów potencjalnie wybuchowych, ale także w zapobieganiu utlenianiu niektórych produktów spożywczych. Od czasu wprowadzenia dużego klarownika nasza oferta jest systematycznie rozszerzana. Aktualnie oferujemy systemy modułowe, które można dostosować do około 70 różnych konstrukcji maszyn.
W jakich zastosowaniach są wykorzystywane poszczególne konstrukcje maszyn?
Frank:
Swobodny przelew po stronie oleju lub tłuszczu jest wykorzystywany głównie w przypadku wysokich temperatur, np. z tłuszczami zwierzęcymi lub olejem rybnym. Swobodny przelew po stronie wodnej jest wykorzystywany na przykład w przypadku oliwy z oliwek. Hermetyczną hydroszczelność wykorzystujemy głównie w przypadku piwa, a częściowo także wina. Zależy to całkowicie od wymagań klienta.
Nasze separatory są już dostępne w wariantach przystosowanych do wielu zastosowań. Jak już wspomniano, pierwszy separator pracuje w winnicy od ponad 20 lat. Kolejne konstrukcje obejmowały separatory do przetwarzania soków owocowych, pektyny cytrusowej, kawy, kofeiny, herbaty, mleka sojowego, oleju cytrusowego, soku pomarańczowego, pektyny jabłkowej, piwa, serwatki, oliwy z oliwek, oleju rybnego, biodiesla, tłuszczu zwierzęcego, alkoholu spożywczego, zużytego oleju i farmaceutyków, a także do zbioru glonów.
Christoph:
Ogólna zasada przedstawia się następująco: Mamy obecnie cztery różne rozmiary pod kątem różnych zakresów wydajności. Są one zasadniczo niezależne od obszaru zastosowania. Produkt decyduje o dalszych modyfikacjach systemu: wybór klarownika do separacji dwufazowej lub separator do separacji trójfazowej; wybór maszyny o większej odporności na korozję lub wykonanej z materiału standardowego; wybór wariantu pod kątem materiałów o wyższej gęstości materii stałej. Dostosowaliśmy maszyny tak, aby mogły obsługiwać szeroką gamę produktów bez względu na gęstość materii stałej oraz właściwości korozyjne.

W jaki sposób rozpoczyna się każdy projekt i czy w tym celu powoływany jest specjalny zespół w firmie Flottweg?
Christoph:
Formalnie w dziale rozwoju pracuje jeden zespół ds. separatorów. Jednak wszyscy inżynierowie mają wiedzę i kompetencje niezbędne do projektowania takich systemów. Złożony z kilku inżynierów zespół ds. rozwoju separatorów jest jednym z czterech zespołów ds. rozwoju w firmie Flottweg, których funkcjonowanie ma wysoce interdyscyplinarny charakter. Poza stałymi członkami projektu w fazie koncepcyjnej angażowany jest również personel działów rozwoju, projektowania i inżynierii procesowej. Na tym etapie określamy charakterystykę produktu, który maszyna będzie przetwarzać, i staramy się opracować koncepcję konstrukcji systemu. Za zakupy, planowanie produkcji i planowanie projektu również odpowiadają stali członkowie zespołów rozwojowych. Oprócz tego angażowany jest zespół tymczasowy, który nie jest potrzebny przez cały czas trwania projektu, ale odgrywa ważną rolę. Na przykład: dział sprzedaży uczestniczy na samym początku i na końcu projektu, jeśli chodzi o zewnętrzne testy prototypów. Zespoły produkcji i montażu są angażowane w projekt na etapie produkcji lub montażu prototypów. Dobra komunikacja jest tu kluczowa. Określone fazy projektu wymagają również kontroli i dokumentacji. Dział dokumentacji wprowadzany jest zazwyczaj pod koniec projektu w celu opracowania odpowiednich instrukcji i podręczników pod kątem prób eksploatacyjnych oraz prawidłowego utrzymania. Nowy projekt wymaga zaangażowania niemal całej firmy, jeśli uwzględni się wszystkich pracowników biorących udział w jego realizacji. Należy podkreślić, że sfinalizowanie projektu może trwać nawet od roku do trzech lat w przypadku całkowicie nowego projektu.
Jak przebiega proces zamawiania separatora?
Christoph:
Ani dział rozwoju ani dział inżynierii procesowej nie są zaangażowane z zwykłą produkcję seryjną maszyn. Jeśli wniosek został już zatwierdzony, dział sprzedaży może samodzielnie sprzedać maszyny.
Po otrzymaniu zamówienia na separator dział sprzedaży współpracuje z działem projektowym w celu określenia specyfikacji maszyny, a następnie przekazuje projekt do realizacji przez dział logistyki zamówień. W ten sposób powstaje zamówienie produkcyjne, które jest podstawą rozpoczęcia produkcji i zatwierdzenia maszyny. Następnie maszyna jest dostarczana do klienta lub jest przekazywana do naszego działu konstrukcji instalacji w celu montażu podstawy, szafy sterowniczej itp.
Jak często pojawiają się pytania dotyczące nietypowych zastosowań?
Frank:
Nietypowe potrzeby i specyfikacje są dość powszechne, szczególnie w branżach chemicznej i farmaceutycznej. Często muszą zostać spełnione specjalne wymagania w zakresie odporności, gęstości lub jakości produktów bądź separacji. Jesteśmy gotowi zapewnić pomoc w opracowaniu rozwiązania do każdego z takich zastosowań.
Christoph:
Podstawą naszych zaleceń są próby wykonalności. Dział sprzedaży może uznać, że potrzeb klienta nie jest w stanie zaspokoić żadna z 70 konstrukcji, które są obecnie oferowane. Kieruje wówczas wniosek o przeprowadzenie próby wykonalności do działu technologicznego. Działy inżynierii procesowej i rozwoju szacują, ile wysiłku potrzeba, aby spełnić wymagania klienta. Podejmowana jest następnie decyzja o ewentualnym podjęciu tego wysiłku i zobowiązania wobec klienta.
Jakie projekty były do tej pory najbardziej ekscytujące lub niezwykłe?
Frank:
Jednym z najbardziej ekscytujących projektów testowych był projekt realizowany dla browaru z Monachium. Fizyczne umieszczenie maszyny w zakładzie było dość trudne. Wszyscy mieliśmy nadzieję, że nigdy nie będzie konieczne wyniesienie maszyny z głębi piwnicy, ponieważ byłoby to jeszcze trudniejsze niż jej wniesienie. Najpierw przetestowaliśmy wszystkie najpopularniejsze receptury piwa producenta z wykorzystaniem separatora. Piwo przetworzone zarówno z wykorzystaniem separatora, jak i bez niego zostało zabutelkowane. Następnie było ono próbkowane przez trzy miesiące, aby ustalić, czy nastąpiła zmiana smaku. Dopiero po ustaleniu, że tak się nie stało, separator mógł zostać ponownie uruchomiony. Później minęły kolejne trzy miesiące, zanim urządzenie zostało sprzedane, a my mogliśmy wreszcie wypić toast na lokalnym festiwalu piwa.
Podobny przebieg miał projekt realizowany u producenta pektyny jabłkowej. Gdy po raz pierwszy odwiedziłem zakład, znajdowały się tam tylko separatory konkurencji. Od tego czasu klient wymienił niemal wszystkie jednostki na maszyny marki Flottweg.
Christoph:
Dla mnie najbardziej ekscytującym projektem był ten związany z opracowaniem modelu AC1200, ponieważ w wielu obszarach mogliśmy zastosować nowe lub odmienne podejście. Maszyna została całkowicie zmodyfikowana pod względem wyglądu i konstrukcji. Był to także pierwszy przypadek zastosowania interdyscyplinarnego podejścia. Projekt miał wyjątkowo duży walor edukacyjny – szczególnie dla mnie.
W niektórych obszarach separator marki Flottweg jest wciąż postrzegany jako nowość. Dlaczego tak jest Twoim zdaniem?
Christoph:
Mamy w ofercie wiele modeli maszyn, a nasze separatory doskonale sprawdzają się w wielu branżach i zastosowaniach. Jednak niektórzy producenci są na rynku od ponad 20 lat. W porównaniu z nimi jesteśmy wciąż uważani za nowicjuszy w niektórych obszarach.
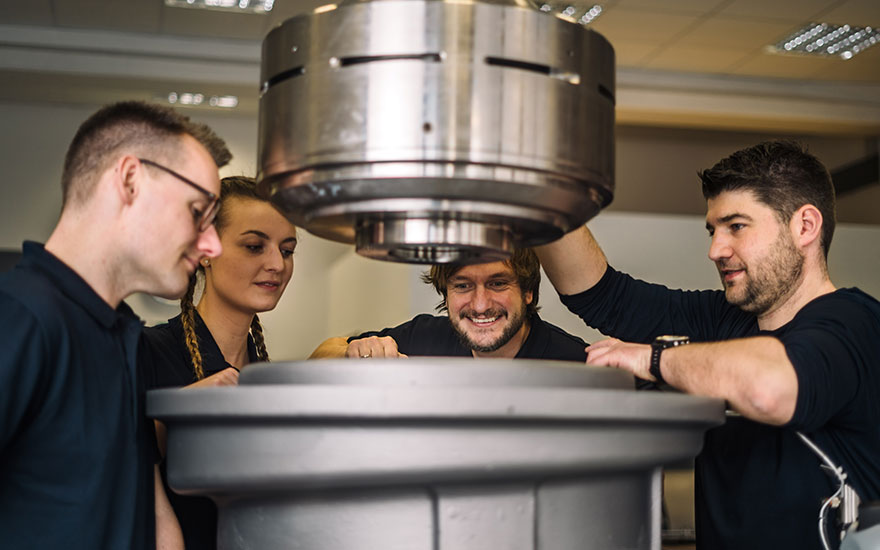
Co wyróżnia separator marki Flottweg? Jakie są nasze zalety w porównaniu z konkurencją?
Frank:
Po pierwsze nasze separatory są niezwykle wydajne. Ponadto doskonale radzą sobie z wahaniami parametrów procesu. Jak wspomnieliśmy wcześniej, klient wytwarzający pektynę korzystał wcześniej z separatorów od konkurencji. Gdy klient zwrócił się o opinię do pracowników działu utrzymania ruchu, okazało się, że są oni bardzo zadowoleni z naszego separatora. Mówili, że jest on o wiele prostszy, tańszy i szybszy w utrzymaniu. Z kolei operatorzy maszyn przyznali, że nasze urządzenie lepiej radzi sobie z wahaniami lub zakłóceniami w procesie produkcyjnym niż inne modele.
Christoph:
Nasza maszyna jest bardzo trwała i łatwa w utrzymaniu. Dwie wykwalifikowane osoby mogą szybko rozłożyć separator na jego główne podzespoły w celu określenia, gdzie może występować problem, lub przeprowadzenia wymiany części serwisowych. Pod tym względem poruszamy się dość szybko. Dla wielu klientów ważnym aspektem jest możliwość szybkiego i łatwego wykonania prac konserwacyjnych oraz błyskawicznego uruchomienia maszyny.
Dodatkowo separatory marki Flottweg charakteryzują się zastosowaniem systemu odprowadzania. Oprócz prostej konstrukcji i łatwości utrzymania system oferuje również korzyści związane z zastosowaniem technologii SoftShot®, która istotnie zmniejsza hałas towarzyszący opróżnianiu. Rozwiązania mechaniczne, które za nią stoją, są znacznie prostsze niż w wielu maszynach innych producentów, ale wciąż dają one możliwość przeprowadzenia częściowego lub całkowitego opróżniania.
Czego możemy się spodziewać w przyszłości?
Christoph:
Obecnie realizujemy wiele ciekawych projektów rozwojowych. Jednym z nich jest model AC1500, w którym wykorzystamy konstrukcję modelu AC1200 ze zmianą niektórych komponentów i zespołów. Zbliżamy się również do zakończenia prac nad nowym rozmiarem pośrednim. Chodzi to model AC1700, który pod względem wielkości znajduje się między modelami AC1500 i AC2000. W oparciu o nowy rozmiar będziemy mogli lepiej reagować na oczekiwania klientów w zakresie wydajności produkcyjnej.
Kolejnym bardzo obiecującym projektem są prace wokół separatora dyszowego. Ma to być nowa jednostka do separacji marki Flottweg. Gdy rozmawiamy o separatorach, mamy na myśli przede wszystkim separatory samoczyszczące z hydraulicznym mechanizmem otwierania. Konstrukcja separatora dyszowego obejmuje dużą liczbę zainstalowanych na obwodzie bębna dyszy, przez które odprowadzana jest materia stała. Trwają obecnie różnego rodzaju próby eksploatacyjne prototypów. Ponieważ testy wstępne zakończyły się powodzeniem, pierwsze maszyny zostały już dostarczone klientom. Ponadto nadal jesteśmy w trakcie realizacji projektu systemu modułowego. Planujemy opracowanie nowej wersji modelu AC1500, tak aby móc przetwarzać materię stałą o większej gęstości. Ponadto powstają modele AC2500 i AC1200exp (z gazem obojętnym). Realizujemy zatem wiele ciekawych projektów rozwojowych.
Frank:
Wprowadzamy również drobne zmiany i ulepszenia, np. w zakresie ograniczania zużycia energii lub adaptacje tworzone w odpowiedzi na pytania dotyczące wykonalności.
Christoph:
Ogólnie można powiedzieć, że: doskonalimy naszą ofertę produktową i rozszerzamy ją o nowe rozmiary, a dzięki separatorowi dyszowemu wkraczamy na nowe obszary.
O ekspertach
Christoph Hobmeier
Dołączył do firmy Flottweg w 2015 r.
Inżynier ds. rozwoju w zespole MDS (Machine Development Separator).
Frank Giegler
Dołączył do firmy Flottweg w 1998 r.
Rozpoczynał w dziale prób; obecnie pracuje w dziale inżynierii procesowej.

Chcesz dowiedzieć się więcej o Flottweg?
Wystarczy do nas zadzwonić lub napisać!