- Wydajna i niezmieszana separacja tworzyw sztucznych o cząstkach mniejszych niż 1 mm
- Przekształca mieszane tworzywa sztuczne w czyste, gotowe do wprowadzenia na rynek materiały dzięki precyzyjnej separacji
- Efektywność kosztowa: brak konieczności odwadniania oraz niskie koszty wody i energii
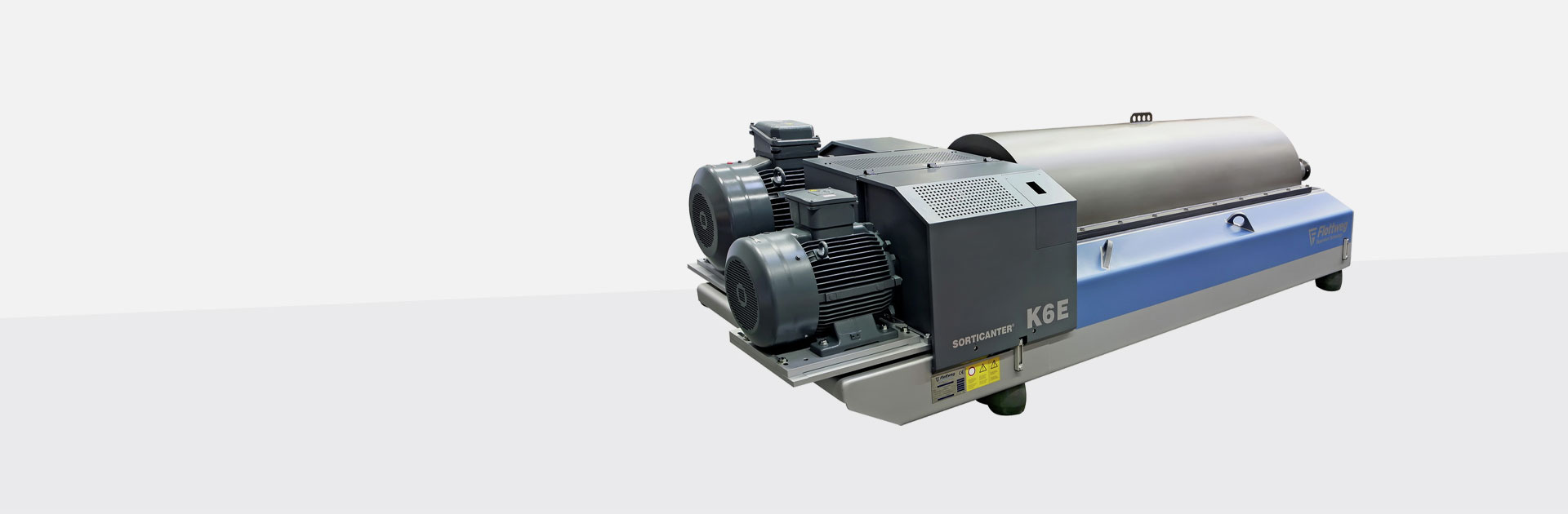
![[Translate to Polish:] sorticanter-stage-mobile.jpg](/fileadmin/user_upload/data/product_lines/product-stages-and-teaser/sorticanter-stage-mobile.jpg)
Flottweg Sorticanter®
Dekanter do recyklingu firmy Flottweg
Innowacyjna technika wirówki do recyklingu tworzyw sztucznychOchrona środowiska i recykling coraz częściej są kluczowymi aspektami dla przedsiębiorstw, które wymagają nowych i innowacyjnych rozwiązań. Dla firmy Flottweg był to powód zaprojektowania wirówki Sorticanter® do przetwarzania tworzyw sztucznych.
Surowce naturalne, takie jak rośliny, węgiel, gaz ziemny i ropa naftowa stanowią podstawę produkcji tworzyw sztucznych. Surowców tych nie można odzyskać za pomocą operacji chemicznych w procesie przetwarzania. Recykling tworzyw sztucznych to temat, który budzi zainteresowanie wszystkich ludzi o rozwiniętej świadomości ekologicznej. Sorticanter® przyczynia się do ochrony środowiska zgodnie z zasadami ekologii i ekonomii.
Dzięki wytwarzanej sile odśrodkowej Sorticanter® może oddzielać od siebie różne rodzaje tworzyw sztucznych. W ten sposób użytkownicy mają zapewnioną największą możliwą czystość odmianową (czyli stopień posegregowania) tworzyw sztucznych. Zbieranie i przetwarzanie tworzyw sztucznych zmniejsza ponadto koszty utylizacji oraz ilość śmieci na wysypiskach.
Od 1995 roku wirówki Sorticanter® firmy Flottweg przetwarzają najróżniejsze tworzywa sztuczne. Sorticanter® charakteryzuje się wydajnością oraz zachwyca doskonałą jakością i trwałością.
Zakres zastosowania: przetwarzanie tworzyw sztucznych
Jak działa Sorticanter®?
Podczas przetwarzania tworzyw sztucznych (odpadów, włókien z tworzyw sztucznych i lekkich opakowań) ważne jest, aby poszczególne tworzywa sztuczne były „czyste odmianowo”. Wiele tworzyw sztucznych różni się gęstością. Dlatego wydajna okazała się tak zwana flotacyjno-sedymentacyjna metoda oddzielania. W tej metodzie stosowana jest oddzielająca faza ciekła (najczęściej woda), przy czym ciężar właściwy fazy ciekłej mieści się w zakresie między ciężarem obydwu oddzielanych gatunków tworzywa sztucznego.
W jednym zbiorniku „ciężkie” tworzywo sztuczne o większej gęstości opada na dno, natomiast „lżejsze” tworzywo sztuczne o mniejszej gęstości pływa po fazie ciekłej.
Taka sama zasada jest stosowana również w wirówce. W zbiorniku następuje oddzielanie pod wpływem siły ciężkości (1 g), natomiast w wirówce tworzywa sztuczne są oddzielane przez siłę odśrodkową (wielokrotność przyspieszenia grawitacyjnego). Sortowanie w wirówce przebiega dlatego znacznie szybciej, a posortowane fazy tworzywa sztucznego są znacznie bardziej suche. „Ciężka” faza tworzywa sztucznego jest odrzucana do ściany bębna, a stamtąd prowadzona przez ślimak dekantera do wychodu (faza ciężka). „Lekkie” tworzywo sztuczne gromadzi się na fazie ciekłej. Faza ciekła spływa wzdłuż ślimaka i zabiera przy tym lekkie cząstki tworzywa sztucznego. Specjalna konstrukcja ślimaka powoduje, że również lekka faza jest transportowana w kierunku wychodu fazy stałej (faza lekka) i odwadniana. Faza ciekła wypływa przez tarczę skórującą pod ciśnieniem.
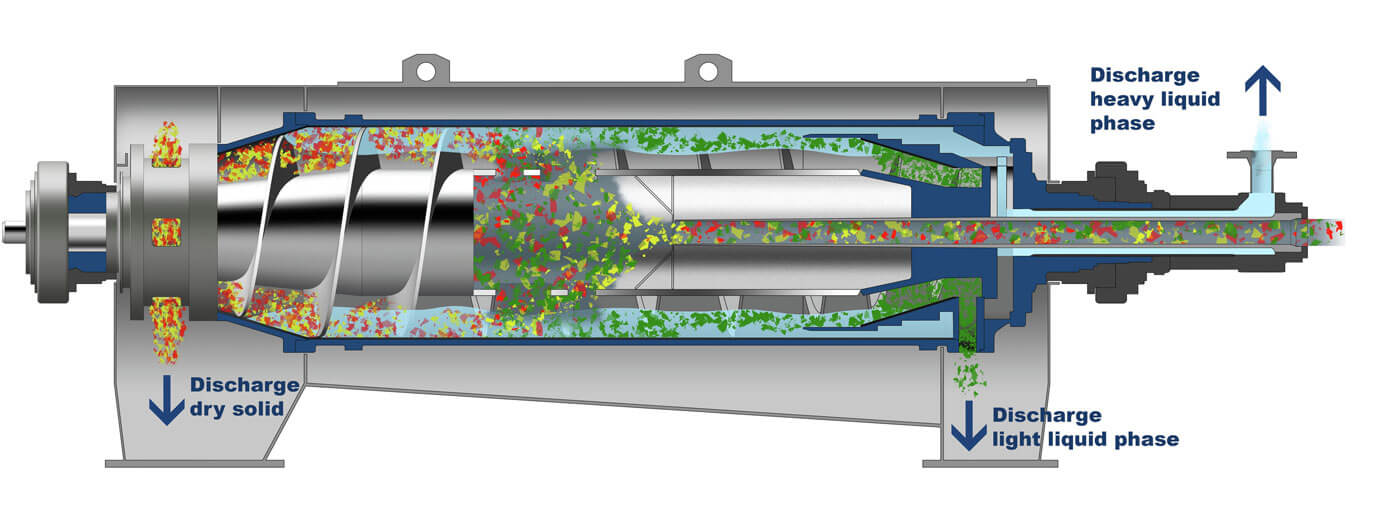
Cechy produktu
Wydajność
Pod wpływem wysokich przeciążeń w Sorticanters® oraz unikalnej konstrukcji ślimaka wyprowadzane cząstki tworzywa sztucznego są znacznie suchsze niż w przypadku stosowania innych metod. Tworzywa sztuczne mogą być zatem oddzielane skuteczniej i z większą czystością odmianową. Zwiększa to jakość produktu, a tym samym wartość produktu końcowego. Ponadto Sorticanter® może oddzielać cząstki o średnicy poniżej 1 mm oraz mieszanki materiałów lub włókien, które nie nadają się do oddzielania statycznego. W porównaniu z innymi metodami zapewnia to większą dokładność separowania.
- Lepsza jakość produktu, a tym samym większa wartość produktu końcowego
- Separacja mieszanek materiałów nieprzystosowanych do oddzielania statycznego (włókna)
- Separacja cząstek mniejszych niż 1 mm
Oszczędność kosztów
Dzięki wysokiej dokładności separowania i odwadnianiu tworzyw sztucznych do odwadniania uzupełniającego nie jest potrzebne wirowanie. Zmniejsza to niezbędne wydatki. Ponieważ Sorticanter® wymaga do obsługi mniejszej liczby pracowników, można oszczędzić koszty eksploatacji. Również mniejsze zużycie świeżej wody oraz energia termiczna korzystnie wpływają na koszty eksploatacji. Ponieważ tworzywa sztuczne są już odwadniane mechanicznie, powoduje to oszczędność kosztów odwadniania termicznego.
- Brak dodatkowego odwadniania uzupełniającego (wirowanie)
- Mniejsze zużycie świeżej wody
- Minimalna potrzebna liczba pracowników, przekładająca się na oszczędność kosztów dla użytkownika
- Mniejsze zużycie energii termicznej
Bezpieczeństwo procesu
Wirówki Sorticanter® firmy Flottweg pracują z reguły 8000 godzin w roku. Ten fakt oraz wieloletnie doświadczenie firmy Flottweg zapewniają wysokie bezpieczeństwo procesów oraz dyspozycyjność maszyn. Ponadto nasze wirówki Sorticanter® są projektowane i produkowane wyłącznie w Niemczech. Zapewnia to wysoką jakość naszych maszyn i części oraz umożliwia długą eksploatację. Przez dodanie oddzielającej fazy ciekłej wymywany jest na przykład pył z powierzchni tworzyw sztucznych. Pęcherzyki powietrza oraz efekty na powierzchni nie mają wpływu na separację, co z kolei zapewnia wysoką dyspozycyjność.
- Roczny czas pracy z reguły 8000 godzin
- Wysoka dyspozycyjność
- Jakość Made in Germany i wysokie kompetencje inżynierskie
- Brak oddziaływania przez pęcherzyki powietrza oraz inne efekty zakłócające separację
Operação
Wysokogatunkowe materiały naszych wirówek Sorticanter® zmniejszają nakłady na prace konserwacyjne i związane z utrzymaniem ciągłości eksploatacji. Maszyną można łatwo sterować i konserwować ją oraz w prosty sposób wymieniać części eksploatacyjne. Zmniejsza to nakład pracy dla personelu obsługi. Parametry robocze można regulować przejrzyście z poziomu interfejsu użytkownika. Ponieważ Sorticanter® – tak jak inne wirówki dekantacyjne – tworzy zamknięty system, personel obsługi jest narażony tylko na minimalne nieprzyjemne zapachy.
- Minimalna liczba pracowników
- Mniejsze nakłady na konserwację
- Mniej nieprzyjemnych zapachów ze względu na zamknięty system
K4D
Wymiary [mm]* | 3400x1300x1100 |
Masa [kg]* | 3050 |
K6E
Wymiary [mm]* | 5100x1800x1300 |
Masa [kg]* | 9750 |