2024-10-28
Sewage treatment plants as a complete system
Reliability in the sludge thickening process
Treatment plants use different wastewater treatment processes depending on their size. Smaller plants for up to 30,000 residents are often constructed as aeration plants with aerobic sludge stabilization. Larger plants (>30,000 residents), on the other hand, usually employ anaerobic sludge stabilization. During this process, the activated sludge produced during biological purification is withdrawn from the secondary settling tank and returned to the aeration tank. However, a portion of this stream needs to be withdrawn as surplus sludge and fed together with the primary sludge arising from the preclarification stage into the digester for anaerobic sludge stabilization.
The large volume of this surplus sludge presents a considerable challenge. The sludge is drawn off from the secondary settling tank with a very high dilution of only about 5–10 g/liter, and it must therefore be thickened to about 50–85 g/liter to reach the optimal concentration for the digester. The volume is reduced by about 80–90%. There are various methods to accomplish this, including static thickening or straining, but each method has its specific disadvantages. One excellent method – and one with a wide range of advantages – is thickening with decanters.
Although it is technically challenging to operate a digester, it is crucial for the overall process and the resulting operating costs of the sewage treatment plant. This is because an optimal digestion process increases the gas yield and thus reduces energy costs. At the same time, well-digested sludge can be dewatered very well, which also reduces disposal costs. Optimized loading of the digester has a very positive effect on the control of the overall process. The loading must be as uniform and constant as possible. One way to achieve this is with the Flottweg OSE decanter with thickened sludge control.
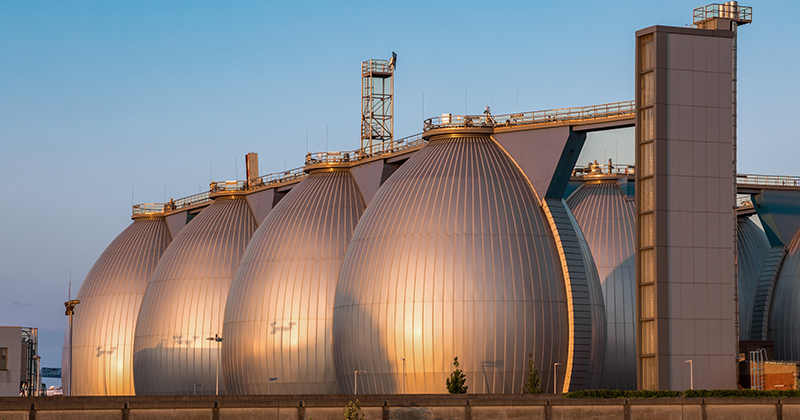
The thickening process and influencing factors
Looking at the overall process, there are some important points and influencing factors to take into account:
- The feed conditions into the sewage treatment plant influence the concentration and volume of the surplus sludge. Heavy rain can play a key role in this.
- The sludge should be drawn from the secondary settling tank in a process-optimized manner, i.e. soon after the sludge has been produced.
- The digester prefers a solid feed with a constant rate and concentration.
- The separation efficiency of the thickening process must be as high as possible in order to keep the return load as low as possible; at least 95% is required. 98% or higher is even better.
- Because polymeric flocculants can interfere with the digestion process, their amounts should be kept as low as possible.
- The more polymer there is in the sludge, the higher the viscosity and the poorer the mixing in the digester. The result is a decrease in gas yield.
The challenge:
The thickening system operates mostly autonomously, without much attention from the operating personnel. But process stability and reliability must be guaranteed. At the same time, both the investment costs and the operating costs need to be kept within reasonable limits. The thickening system can be easily adapted to changes in the overall process or special operating situations.
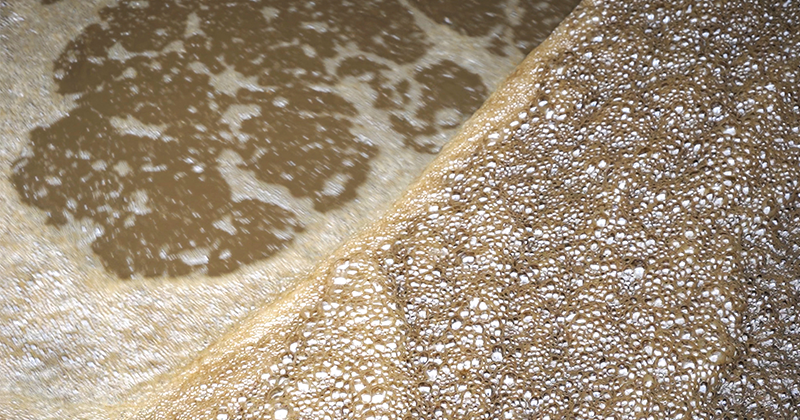
Thickening the surplus sludge with a decanter changes the structure (viscosity) of the sludge. The thickened sludge (TS) has a creamy structure that enables easy pumping even at higher TS concentrations. These sludge properties also have a positive effect in the digester, due to the low foaming and easier escape of the gas bubbles. In contrast, the thickened sludge produced by a belt thickener has a very flaky structure. This sludge is much more prone to foaming in the digester.
With decanter thickening, the solid particles are separated from the liquid by the artificial gravitational field created in the decanter, which is several times stronger than the earth’s gravitational field. Polymeric flocculants (PF) are added in very small amounts only for smoothing the liquid phase.
Taking these influencing factors into account, Flottweg’s OSE decanter was designed to meet the challenges of this process step and has been continuously improved over the years. In addition, its extensive control and regulation technology enables it to operate independently even without supervision by the operating personnel. The decanter’s extensive wear protection ensures a service life of well over 100,000 operating hours, and the machine is designed for 24/7 operation. The specific energy consumption is approx. 0.10 – 0.3 kWh/m³, depending on the sludge properties. The geometry of the bowl and scroll produce unique separation results.
The OSE decanter is a closed system, ensuring that biologically contaminated aerosols are not released into the environment. The low-noise design and low rotor speed ensure low noise emissions.
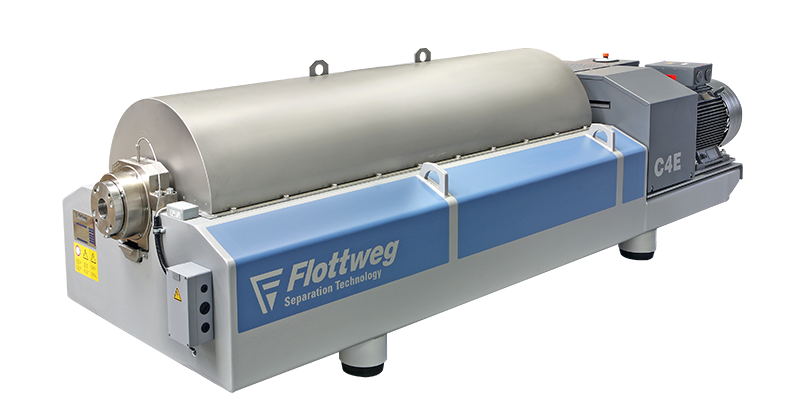
Adding and controlling polymer
The amount of PF required depends on the solids load; in other words, the PF must be regulated according to the load to ensure optimal dosing. For this purpose, a probe is installed in the thin sludge feed to measure the concentration of solids. The load is calculated based on the hydraulic feed and the concentration, and the PF dosing is regulated accordingly. A common PF dose is about 0.5 – 2 kg PF/t TS. The exact value is set by the operator on the operator panel, and then the control system regulates it automatically.
Full flocculation is not necessary when using the decanter, since the PF is only used for smoothing the centrate in order to improve the degree of separation, not for the actual separation itself. As a rule, it is sufficient and, in fact, recommended to use an inexpensive powder product. One key piece of information: in addition to conventional synthetic polymers, you can also use biodegradable polymers based on chitin or starch. And if the sludge properties are good, in some cases you can skip the PF entirely with the OSE decanter.
Thickened sludge control
Changing feed conditions also affects the discharge of thickened sludge. However, it is important for the digester to receive a steady feed of solids as well as constant hydraulic quantity. To ensure these two parameters, the OSE decanter is equipped with an additional control system for regulating the thickened sludge. This system measures the concentration of the thickened sludge with a probe. Using an algorithm in the PLC program, the Simp Drive® unit keeps the concentration of the thickened sludge constant. The operator only has to select the desired value on the operator panel, e.g. 6% TS, and the rest is done by the controller.
Keep an eye on the separation efficiency at all times
The higher the separation efficiency and the cleaner the centrate, the lower the return load for the sewage treatment plant. The OSE decanter can achieve consistent separation efficiencies of >95%, often even >98%. A sensor monitors the quality of the centrate so that operators can keep track of the separation efficiency at all times. This enables you to react immediately in the event of deviations - for example, by adjusting the polymer quantity.
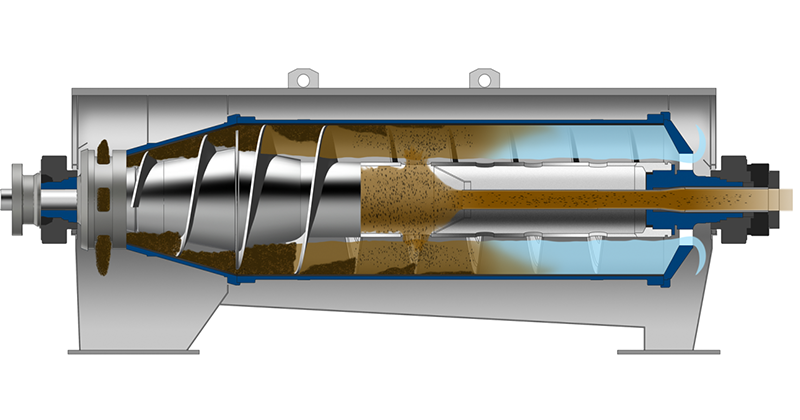
Space requirements and operation of the OSE decanter
This thickening system is very compact. The specific throughput per enclosed space is often much higher than with other systems, especially larger systems. This allows it to be installed in existing buildings, saving on construction costs. Container systems can also be easily implemented.
In addition to the amounts of thin sludge, thickened sludge, and centrate, the system monitors important machine parameters such as speed, vibrations, storage temperature, energy consumption, and pipeline pressures. This enables the operator to keep track of all relevant parameters at all times. The thickening system can be operated and monitored from the operator panel or from the process control station. Apart from occasional inspections, there is no need for on-site intervention.
Easy to maintain and customizable
The Flottweg OSE decanter is designed to be very maintenance-friendly. All important assemblies and components are easily accessible. Maintenance costs are kept to a minimum thanks to extensive and high-quality wear protection in combination with corrosion-resistant stainless steels (V4A and Duplex). Bearings are robust and durable. All wearing parts can be replaced on site, so long downtimes are not expected during the decanter’s service life.
Also no special tools are required, either.
In addition, the service specialists from Flottweg can access the control system – after approval by the operating personnel – and thus provide assistance for operation or maintenance remotely.
In addition to easy maintenance, the system also handles or adapts to changing requirements very well. If, for example, filamentous bacteria (microthrix) appear in the sewage treatment plant and degrade the sludge index, even this bulking sludge can be processed well, despite an SVI of up to 300 ml/g. At most, you can expect increased polymer requirements and/or a somewhat lower throughflow. The system is also well suited to thickening primary or mixed sludge, requiring only optimization of the machine settings. And if additional processes are installed in the future, e.g. thermal hydrolysis, the OSE decanters can be easily adapted.
The constant loading of the digester saves heating costs and improves the digestion process, thereby increasing the gas yield and ultimately improving the energy balance of the sewage treatment plant. 24-hour operation reduces investment costs while simultaneously improving the management of the secondary settling process.
Example of the decanter in use
Customer experience has shown that using the decanter for thickening has improved both the degree of digestion and the dewatering result. What’s more, the fully automatic integration of the thickening decanter into the process management has significantly improved the biologic conditions: The result is lower oxygen consumption, a lower return load due to clean centrate, and a consistently low sludge index (90 – 110). Using the decanter also improves run-off values for NH4-N. Finally, there is a positive impact on dewatering, reducing the energy consumption of the dewatering decanter by about -14%, from 2.47 to 2.12 kWh/m³.
This example and the associated parameters show how the OSE decanter can positively impact the sludge thickening process.
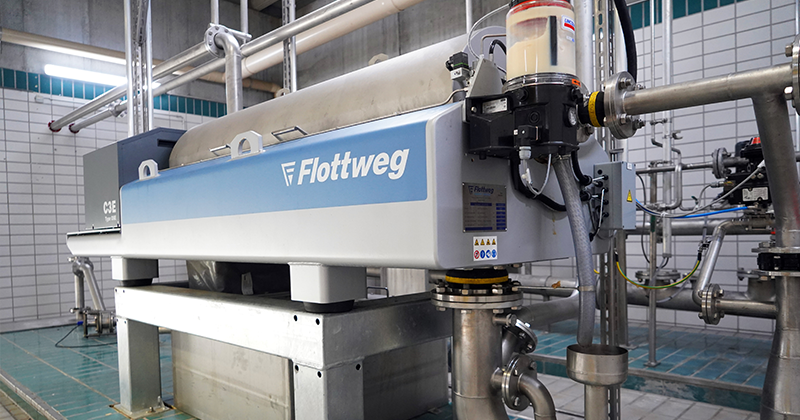
Author: Klaus Peisl, Head of Wastewater and Water Applications, and Alexandra Schlierf, Wastewater and Water Applications Sales Engineer.