2021-05-23
Safe Processing for Combustible Materials with an Explosion-proof Centrifuge
Obtaining a specialized ingredient that goes into a finished product usually involves multiple steps of extraction, purification, and sometimes solvent separation techniques. The challenge is to maximize the amount of the ingredient produced while maintaining high quality or purity. Many companies choose to accomplish this with a decanter centrifuge.
When working with combustible media; however, safety must come first. In order to avoid an explosion, it’s necessary to prevent exposure to oxygen within the centrifuge itself and in the vicinity of operation. Let's take a look at how Flottweg’s gas purge decanter centrifuges helps customers produce a high-purity product without risking safety:
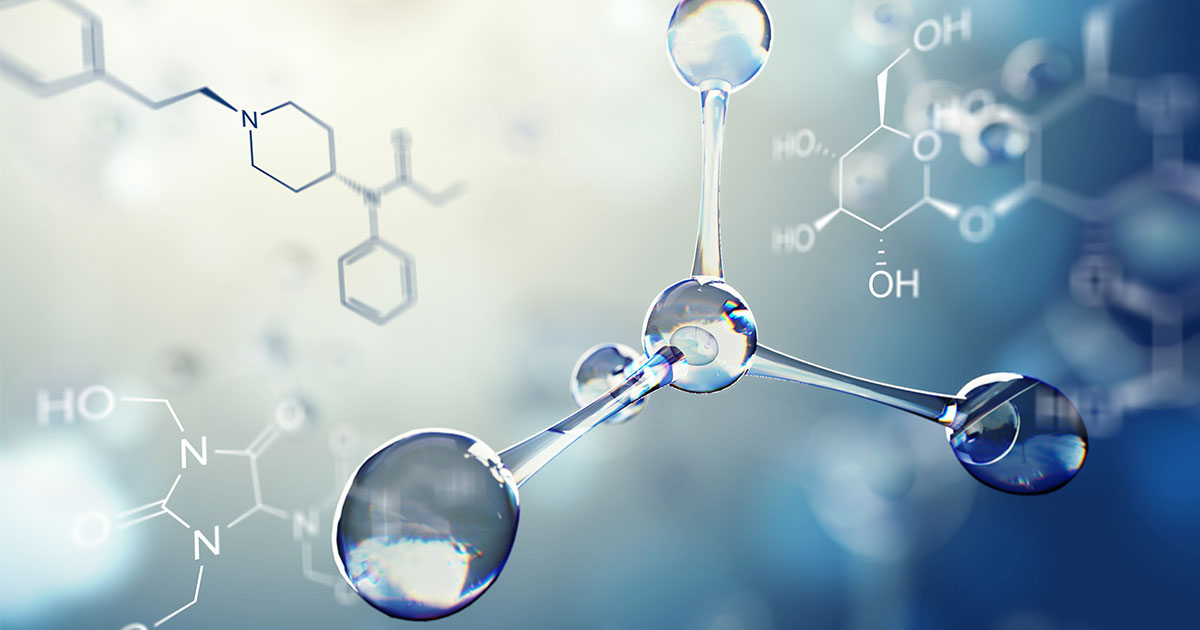
Separating the Crystals from the Solvent
In chemistry, a monomer is a molecule that can react with other monomers to form a larger chain or network in a polymer via a process called polymerization. Many monomers occur in nature (e.g. simple sugars, fats, amino acids, nucleotides) and are components in polymers like collagen, DNA, rubber, or wool. Monomers are also used in the creation of polymers that make up plastics and additives for paint, coatings, adhesives, and more.
One of Flottweg's customers, Solvay Specialty Polymers USA, LLC in Augusta, GA produces one such specialty monomer. Solvay’s Eric Hunter explains that part of the process includes several purification steps that result in monomer crystals mixed with a hydrocarbon solvent. The crystals must then be separated from the solvent, and this liquid waste is recovered and treated for reuse.
The solvent used in monomer production is flammable, so it’s necessary to keep oxygen out of the system and the surrounding environment. To accomplish this, Solvay chose a Flottweg gas purged centrifuge system, which uses nitrogen gas to seal the machine. In addition, hydrocarbon monitors are placed in the room with the centrifuges (as a best practice) to check for leaks.
Blanket Protection with Inert Nitrogen Gas
In order to keep oxygen out and avoid combustion or explosion, the appropriate limiting oxygen concentration (LOC) must be met. This is the amount of oxygen below which combustion is not possible. The exact limit varies based on the current temperature and pressure in the immediate environment.
Flottweg’s systems use continuous flow purging to create a tight seal between the inside of the bowl and the outside environment. Inert gas - nitrogen, in this case - is fed into one area of the system and released at a separate point. A continuous inflow of gas maintains proper pressure and a closed system during operation.
The first step is a pre-purge. The centrifuge is flushed with nitrogen before it’s started. The machine is filled in excess of 0.290 PSI, then it continues to fill with gas until the flow of nitrogen has replaced the interior volume of the centrifuge multiple times over, or until an oxygen sensor indicates a non-hazardous concentration of oxygen. This generally takes less than 30 minutes.
The next step is nitrogen blanketing. Once the machine is running, the system is “blanketed” with gas and held in a constant slight overpressure in order to keep the seals at each end at the proper pressure. This continuous flow purging method relies on pressurized sealing rings, flow meters, flow switches, and pressure sensors to ensure that pressure is always correct.
All of Flottweg’s continuous flow gas purged centrifuge systems are built to Class 1, Div. 1 [USA (NEC 500)] standards. In addition, these systems are also permitted within all Class 1, Div. 2 applications.
Stand-out Protection and Performance
Flottweg is among the small number of OEMs that make sealed centrifuge systems. Hunter explains that the company sets itself apart with “test units that are readily available that we can bring in. We were able to actually see [the] unit in action and see its performance. [Flottweg] then used that data to help give us a guarantee of performance.”
Currently, Solvay performs two crystallization steps in producing the monomer; although there are plans to add another Flottweg centrifuge for a third crystallization in order to maximize yield and increase purity.
Hunter also appreciates the maintenance guidance that accompanies the equipment. They follow Flottweg’s timing recommendations for rebuilds of the rotating assembly. He notes they can simply pull the assembly according to the schedule and send it to the US facility in northern Kentucky for inspection and maintenance. Solvay also follows the provided lubrication schedule for bearings. What’s more, Flottweg’s trained technicians were present at commissioning and are readily available for ongoing support, troubleshooting, and fine adjustments.
Separation equipment is a big investment. It’s good to have a partner who can analyze your needs, provide on-site test units, and stand behind your equipment purchase with technical expertise and responsive service. If you’re in the market for explosion-proof separation equipment, please contact us!

Would you like to learn more about our explosion-proof centrifuges?
Talk to us or write to us!