2025-02-04
“The customer is at the center of our considerations” – interview with Stefan Bichlmeier on Flottweg’s new process center
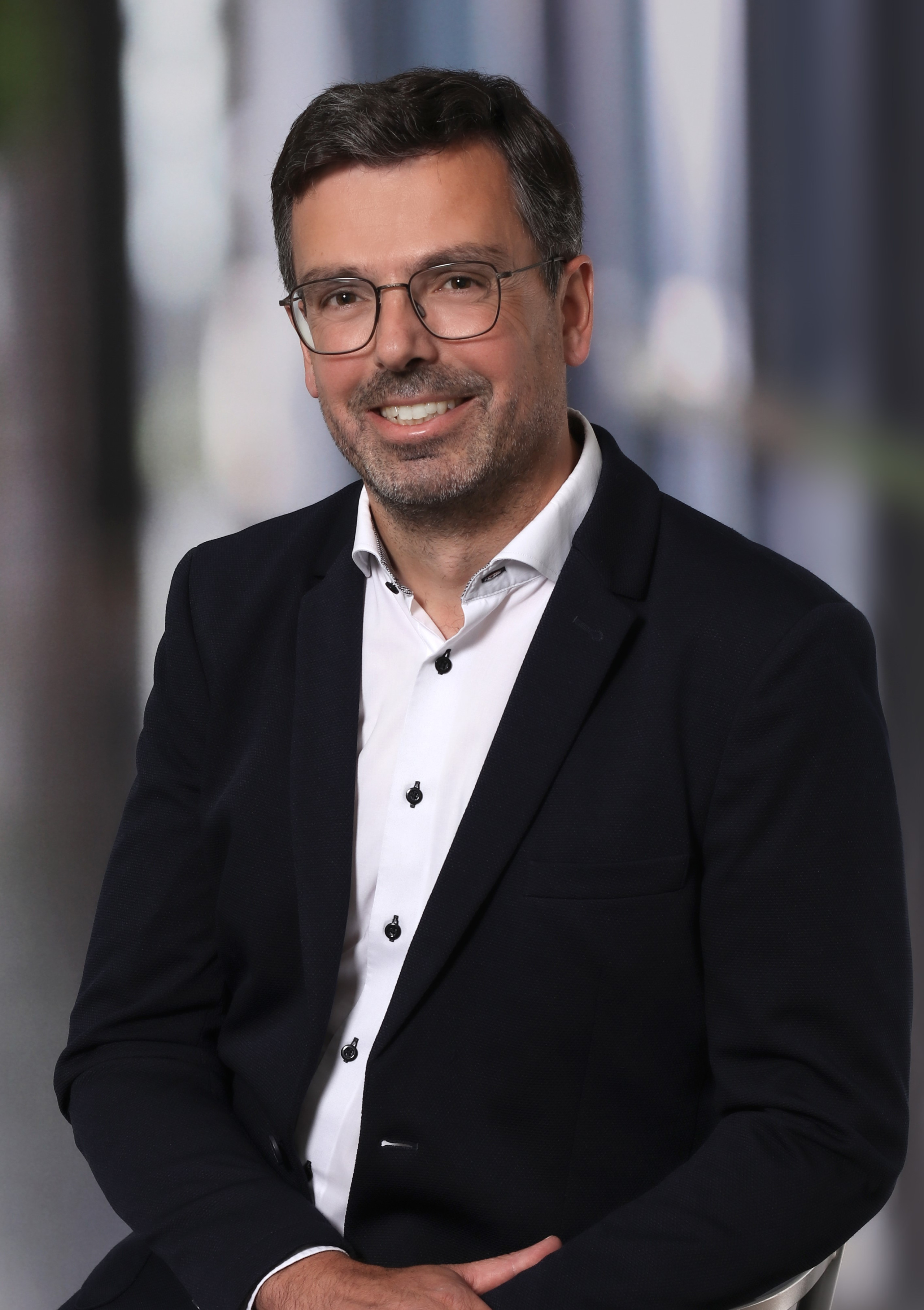
The customer was always at the center of our considerations during the planning phase. On the one hand, we want to process the diverse products and applications in the best possible way in order to optimally serve the needs of our customers.Stefan Bichlmeier Stefan Bichlmeier, Head of Process Engineering at Flottweg and a key player in the development of the process center.
In the summer of 2024, separation technology specialist Flottweg started a new major project with the construction of its new process center. As an extension of Plant 2, which was opened in 2021, the new process center will allow the company to design even more targeted, customer-specific solutions on an area of around 2,000 square meters. Flottweg’s process center will accommodate the laboratory, a pilot plant for testing, a warehouse, and modern office space.
Stefan Bichlmeier, Head of Process Engineering at Flottweg and a key player in the development of the process center, took the time to answer some questions about the process center and the current construction progress.
What is the current state of progress on Flottweg’s new process center?
The construction work, which began in mid-August last year, is progressing very well and is on schedule. The shell was completed before the end of the year. After the roof sealing and the installation of the windows, work on the interior and the facade can now commence in January. We are pleased that, as things stand right now, there is nothing in the way of our planned start of use in October 2025.
What makes the new process center so special? What were the main considerations during planning?
The customer was always at the center of our considerations during the planning phase. On the one hand, we want to process the diverse products and applications in the best possible way in order to optimally serve the needs of our customers. On the other hand, we need to ensure that we can generate meaningful data and results from the tests for our later machines and plant design. In addition, it was essential that the planning address not only current requirements. For instance, the flexibility required for the operation of a pilot plant was and remains a key focus, particularly with regard to the technical equipment.
A key difference to our current facilities will be our ability to have a stricter spatial separation for the different application areas, both in the laboratory and especially in the pilot plant area. This means that intermediate products from the food and pharmaceutical industry are processed in specially designed test areas. In addition, a permanently installed CIP system will further expand our possibilities. These include structured development trials with new machines and more efficient cleaning of the technical equipment. From the customer’s point of view, however, there was another important aspect that was a decisive factor in their investment in the plant: the possibility of extending a Factory Acceptance Test to validate the cleaning results. This will enable us to offer this in a more targeted manner and under standardized conditions where required.
The design of the pilot plant will also allow us to conduct multiple tests side-by-side in the future. This will put us in a position to increase our focus on the availability of the products and the scheduling possibilities of our customers.
Modern workplaces will provide added value, as will the future proximity of the laboratory, technical center, and the office space for process engineering.
Why did Flottweg opt for this investment?
Requests for laboratory tests and in-house trials have grown steadily in recent years. Overall expectations and demands regarding the test results have also increased. In addition, we want to intensify the development and ongoing enhancement of processes and sub-processes. The collection of all consumption data and the associated optimization are of crucial importance in this regard. This also necessitates the mapping of these processes on a pilot plant scale where possible.
The equipment and, above all, the current premises would no longer have been sufficient for all this in the short to medium term. Consequently, we decided to implement a complete, future-proof solution.
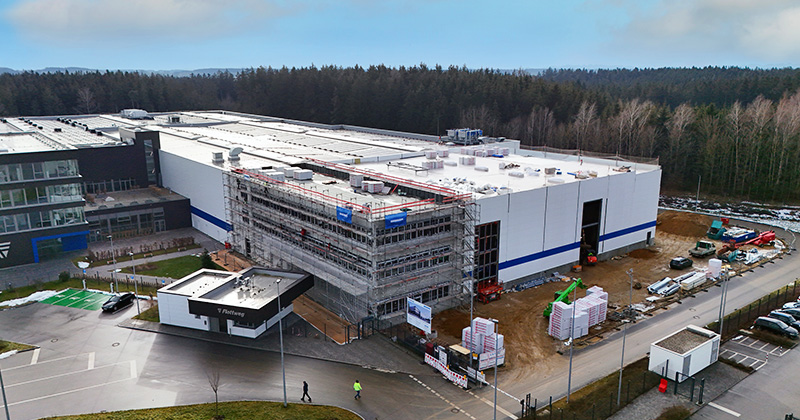
How will Flottweg’s customers benefit from the new building?
The customer stands to benefit in many ways. The most obvious benefits are the scheduling flexibility, the extended scope of process equipment, the possibility of targeted application developments the collection of consumption data, as well as the option of joint cleaning validation.
The proximity to the laboratory also makes it possible to analyze the samples promptly during test operation. This allows us to evaluate and optimize the test settings in a more targeted manner during the actual test phase.
The targeted selection of machines suitable for the test material is and remains crucial to our success and will continue to be covered by our extensive stock of test and rental machines.
What sustainability and environmental aspects were included in the planning?
With the new construction, we will be moving into a building that is designed according to the latest standards and will therefore in itself bring about significant energy savings. Particularly with regard to the ventilation systems, our energy recovery will be massively improved over the current state.
The CIP system is designed as a closed-loop system, thus minimizing losses. Wastewater disposal also covers all relevant aspects by means of a buffer tank, neutralization facility, and coalescence separator.
In addition to the building itself, however, another sustainability issue was also an important consideration for the construction project.
While on-site customer testing will continue to be of great importance in the future, we can and do intend to make use of the expanded in-house possibilities. Thus, more tests will be carried out at our own site where possible and appropriate. This means that we will not travel to the customer with machines, system equipment, and technicians, but instead bring the test batch to our premises. Under the right conditions, this option can save resources and costs for both transportation and travel.
What innovations or new technologies will be integrated into the process center?
Some information on this has already been discussed. Another thing that bears mentioning is a fixed and multi-stage extraction process, which will be a central and innovative component. The first few years will have a strong focus on protein applications. We would like to further expand our already extensive experience through targeted development and offer added value to customers in particular. They can provide us with flour samples, which will then be processed using a previously coordinated process sequence. The system itself is sufficiently flexible to allow complete processes, sub-processes, known or new procedures as well as the process-relevant machines to be tested. As already mentioned, this also involves collection of the relevant consumption values.
Product samples can be created, which the customer can then use for further processing, analysis, or tasting purposes.
More information on the process center can be found on our overview page.