2024-09-26
Direct Lithium Extraction Technology Intensifies Mining Operations
With the advancement of DLE technology, lithium can be extracted and processed in two months rather than two years with minimal impact on the environment and minimal water usage.
The electrification movement has forced engineers and miners to find a better way to produce lithium more quickly. Mining lithium is nothing new. It has been intentionally mined since the 1950s. However, global demand for lithium batteries for electric vehicles and renewable energy storage systems has forced the need for the development of a better processing technology. Prior to the mid 20th century, lithium wasn't required in large quantities, but now it has uses that are not duplicatable by any other minerals, and the scale of demand is unprecedented.
While lithium has been mined for many decades for glass and ceramics, the laptop and cell phone demand in the late 1990s and early 2000s provided additional uses for lithium—especially for batteries. The 2010s brought on the electric vehicle phase and produced a lithium boom unlike the global market had ever seen before. Auto makers are limiting production of internal combustion vehicles and may halt production altogether by the year 2050 in favor of electric vehicles.
The technologies required to produce and mine more lithium have advanced to meet that demand. One of these solutions is a process called direct lithium extraction (DLE), a technique that consists of several processes that allow for fast, isolated lithium production into saleable forms of lithium, also known as LCE, Lithium Carbonate Equivalent.
Centrifuges are vital to the DLE process for many reasons. The most notable being, the ability to perform a liquid-liquid separation, via the Tricanter®. In addition, centrifuges are mobile and run continuously. Centrifuges are not batch operated and do not require consistent operator attention 24/7. This robust equipment is efficient and produces the required value material used for further treatment enhancement and the required waste material on the disposal side.
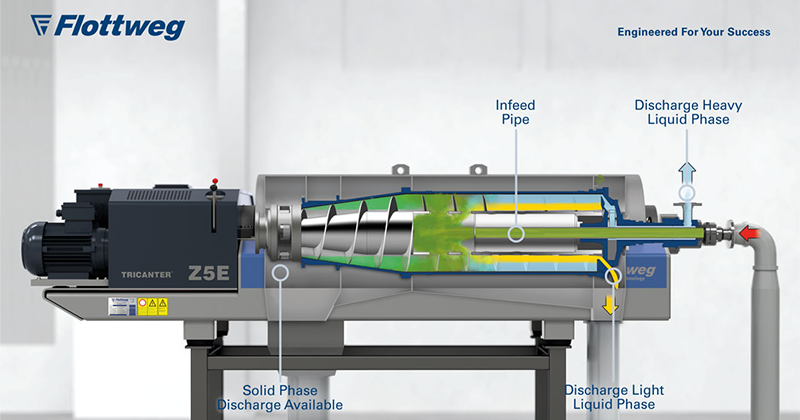
Stages of Lithium Production
Whether the lithium comes from a hard rock mine (where an open pit and blast process is used), or from salt flats (where water is pumped out of the ground and evaporated), centrifuges are a proven technology for both sources. It not only handles the rigors of mining, or the lithium brine, historically evaporated via salt flats, but also the further downstream refining steps. These various stages are indicated below:
Spodumene Lithium Beneficiation & Extraction
In the hard-rock mining of spodumene, or other lithium-bearing ores, the decanter centrifuge is employed at two stages during post-communition/beneficiation. The first stage provides dewatering of slurried tailings. This provides significant water recovery along with a spadeable solid.
The second stage is found in the value stream of further concentration of lithium-bearing slurry—to produce a lithium/spodumene concentrate for additional refinement, while providing additional water recovery for re-utilization.
Lithium-bearing Clay: Dewatering and Processing
Decanter technology accomplishes two crucial stages in lithium-bearing clay processing. Handling a lithium-bearing clay slurry, decanter centrifuges create a further refined, lithium clay concentrate. This step also produces additional water recovery via the centrate output. In refinement steps, the centrifuge handles enriched leachates and post-crystallization.
Refining into Technical and Battery-Grade Lithium
Decanter technology engages in a multitude of stages in the refining of producing technical and battery-grade Lithium. The centrifuge processes lithium carbonate slurry, sodium sulfate slurry, and lithium hydroxide slurry. This produces dewatered salts and thickened value material for additional handling while capturing process water for re-utilization and for promoting water stewardship.
Concentrating Lithium-bearing Brine via Liquid/Liquid Separation
Tricanter® technology separates three-phases from a single feed. In the lithium-bearing brine space, this technology is utilized to concentrate the brine by separating two liquids from a feed of varying densities. A light phase and a heavy phase are produced, permitting further refinement into the final value material. An output of an additional solid phase from your feed can be created to produce three-phases of output from a single feed, if the process requires.
The Two Main Sources for Lithium
Lithium is mined from two sources—hard rock and salt flats. The hard rock process blows up the ground to extract the lithium. For salt flats, a geothermal brine is pumped from below the earth’s crust. The traditional process for extracting geothermal brine is to pump it out and then transport it to the giant salt flat, where it sits for two years. The water evaporates underneath the Sun, leaving salt crystals that contain lithium. The salt crystals then reach a level of purity, which permits transport to a refinery where it's turned into battery grade material used for automobiles. That technology is called a “salar pond evaporation,” or salt flat evaporation. This historic process is effective; however, it takes two years and requires more water than is used for any other mining activity—making the process time intensive and water intensive.
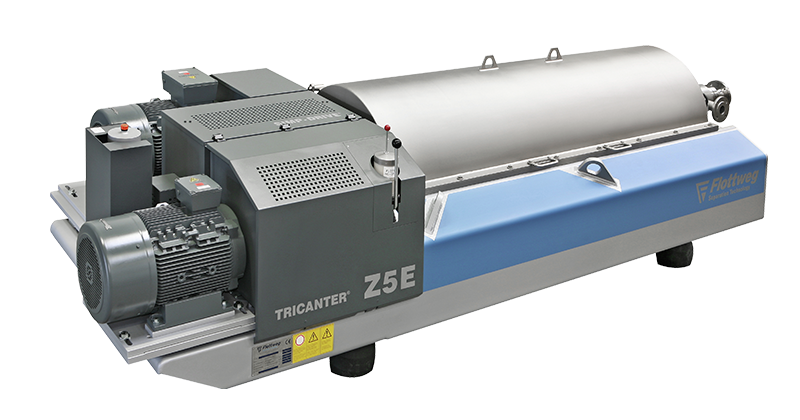
Advantages of Using Centrifuges for DLE and other Lithium applications
Direct lithium extraction (DLE) using centrifuge technology speeds that process from two years to two months. The process involves pumping the lithium out of the ground and instead of throwing it onto a salt flat and then waiting two years, it is pumped out of the ground and processed through the DLE technology, which significantly advances the timeframe for this brine to be concentrated enough to be sent for further refining.
There are many advantages of using centrifuges in Lithium Extraction and Recovery, including:
- Centrifuges are used for the liquid-liquid separation required in the DLE process, reducing 99 percent of water uses in lithium production in historic salt flat evaporation.
- Centrifuges play a key role in separating process water from slurry, enabling recycling and reuse. A key advantage is the continuous recovery that the centrifuge creates, as opposed to alternative technology. This contributes to sustainable water management while reducing the environmental impact.
- Centrifuges require minimal infrastructure for installation, offering practical advantages for lithium producers. With their compact design, centrifuges are easily installed in confined spaces, making them suitable for operations with limited space availability. This design permits additional maneuverability of the unit, to ensure the perfect placement for process flow.
- Lithium centrifuges separate fine tailings from the slurry, contributing to safer and more stable tailings storage facilities, while also extending the life of the site’s TSF, or ponds, delaying costly construction and investment.
- Designed to exacting specifications to ensure the highest purity of separated phases at required cutoff points ensures consistency of quality for additional downstream refining and handling.
- During the lithium brine concentration process, recovering valuable liquid, known as a pregnant liquor, is crucial for increasing overall yield and minimizing waste. The Tricanter® offers the potential for a highly efficient extraction process, ensuring high purity of the separated phases.
- Lithium centrifuges are designed for user-friendly operation and require minimal downtime, ensuring continuous and uninterrupted production.
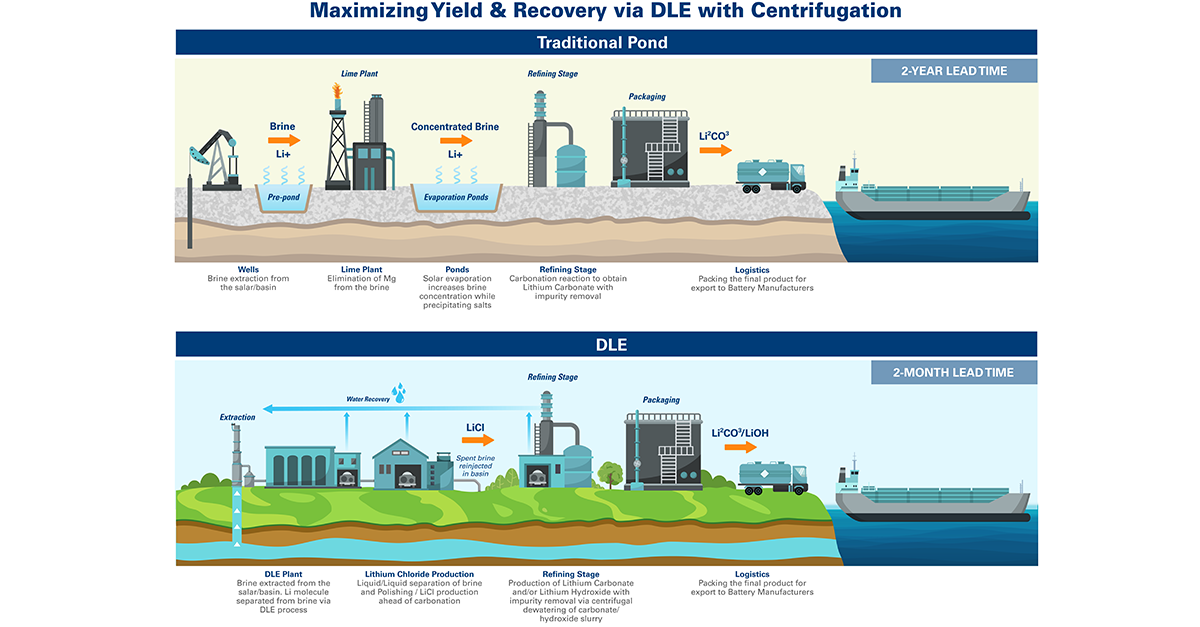
Conclusion
The individual steps and processes in lithium production require different approaches. With the advancement of DLE technology, lithium can be extracted in two weeks rather than two years with minimal impact on the environment and minimal water usage. Centrifuge technology continues to innovate alongside the advancing methods of improved production, that is required for our continuation into the 21st century and beyond.
Author: By Stephen L. Benyo, Flottweg
Stephen L. Benyo is a Global Mining executive for Flottweg Separation Technology. He is engaged in placing the “puzzle-piece” of innovative technology in its most needed locations—striving toward more efficient utilization of our world’s natural resources. Stephen resides in Pittsburgh, Pennsylvania USA with his wife, daughter, and German Shepherd dog.
For more information about Lithium Processing.