2022-07-13
Flottweg's Nozzle Separator - Interview with Flottweg Product Manager Matthias Gaube
Flottweg has developed a new nozzle separator based on decades of experience in separation technology. Matthias Gaube, a Product Manager at Flottweg, played a key role in the development of the nozzle separator. In the following interview, Matthias discusses the application areas in which the new product can be used, the features that received particular attention during development, and how the nozzle separator performed in initial tests.
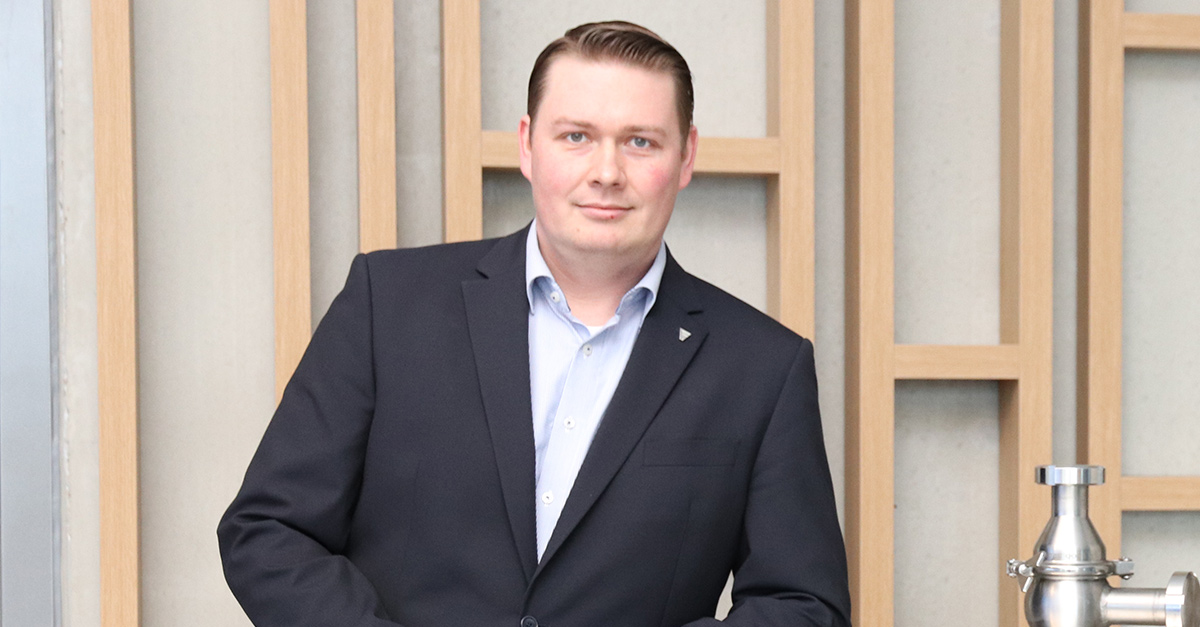
Why did Flottweg develop the nozzle separator?
As a specialist in separation technology, we always strive to offer our customers superior process solutions. As a result of decades of experience with our AC series separators combined with our many requests from customers, we decided to expand our product portfolio to include a high-performance nozzle separator.
What was the main objective when developing the nozzle separator?
At Flottweg, the development of new products is subject to two specific goals: to meet our customers' requirements as best as possible, and to deliver a sustainable separation solution at the same time. Especially in today’s world, when developing such a machine, saving resources is a priority for us and our customers. That is why when designing and constructing our nozzle separator, we paid special attention to a material-saving design that has been optimized for efficiency. This saves resources and also lowers operating costs.
How long did it take to plan and execute the nozzle separator?
From the decision to build a prototype to having the machine ready for testing, we actually only took one year! This shows, once again, how agile and flexible Flottweg is in responding to customer requirements.
Which special feature of the nozzle separator should be addressed?
As already mentioned, we are always eager to satisfy our customers' needs in the most efficient way possible. Low energy consumption combined with high throughput and, of course, excellent separation results, are our customers’ top priorities. I can say with confidence that we have achieved this goal remarkably well with the FDS2000. The low energy consumption of our nozzle separator surprised even our developers.
Which features were particularly important during development?
The bowl of the Flottweg nozzle separator should be mentioned here — after all, it is the heart of the system. The highly innovative design of our bowl combines a variety of positive attributes. Worth mentioning is the particularly smooth running of our system and the maximized energy savings through the specially-controlled discharge from the lower outlet. The rotation of the bowl is supported by the discharge from the lower outlet, thus saving drive energy. In addition, the complete bowl is a compact unit that can be easily assembled and disassembled, thus facilitating maintenance.
Apart from this feature, are there any other technical highlights?
The bowl of our nozzle separator can optionally be equipped with a washing or recirculation device. This was designed with a contactless, and therefore maintenance-free, sealing system. The device makes it possible to rewash the solids in the bowl at operating speed and to compensate for fluctuations in the quality of the product reliably. In addition to this operational benefit, our nozzle separator includes well-known and popular features from the AC series, such as the use of an impeller, the low-maintenance compact spindle drive, and our fully automated lubrication system.
How does a nozzle separator work?
Nozzle separators are used to continuously separate solids from liquids. The product to be clarified or separated flows via a stationary inlet pipe into the inside of the bowl and is gently accelerated to operating speed by the distributor. In the process, larger solid particles are separated directly in the centrifugal field. Finer solids are separated as they flow through the disc stack. The solid particles collect in the bowl's outer solids chambers. From there, they are continuously discharged via the nozzles. The clarified liquid flows from the disc stack and is discharged under pressure via an impeller.
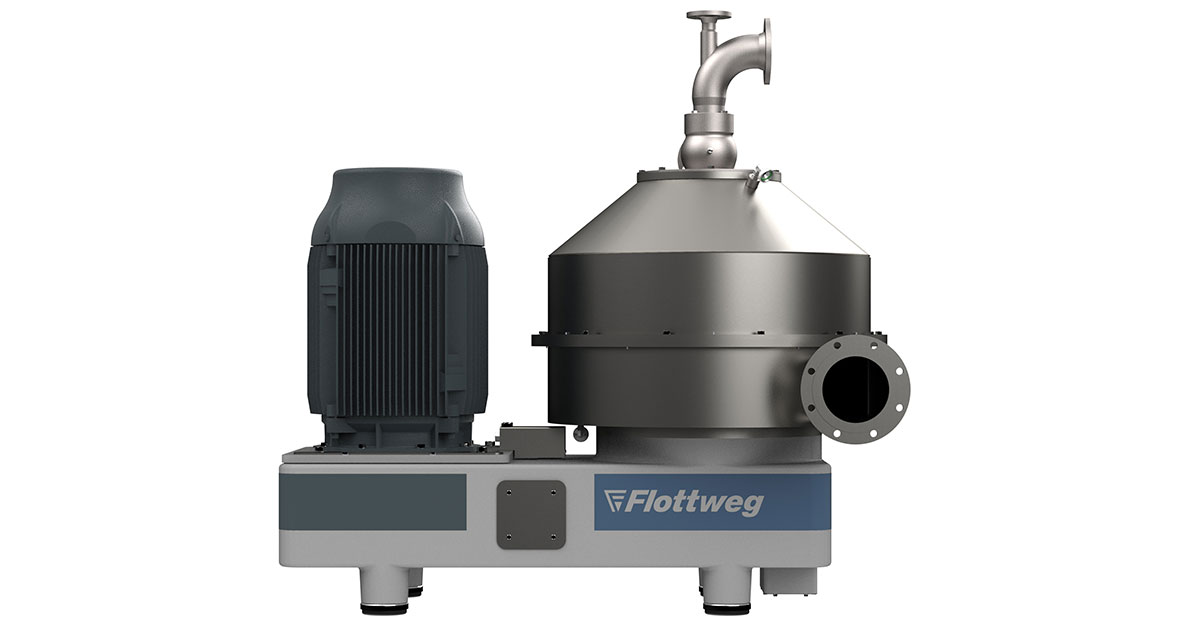
What is the difference between the 2-phase and 3-phase nozzle separator?
In addition to separating solids from liquids, the 3-phase nozzle separator is also used to fractionate different particle sizes. After the separation of solids via the nozzles, the remaining product flow is divided into a middle and upper outlet. Solids with a smaller particle size form the middle outlet flow. The remaining liquid flows through the disc stack, resulting in a nearly clear upper outlet flow. The clear upper outlet flow can then be reused directly in further process steps.
For which application area is the nozzle separator suitable?
We have already tested our nozzle separator extensively and successfully in wet starch production and ethanol manufacturing. However, we are constantly expanding our range of applications and continue to conduct exciting and extremely interesting trials.
What is the capacity of the nozzle separator?
Of course, an exact answer to this question can only be given on a product-specific basis, since different separation tasks have their specific attributes. In general, the throughput of our Flottweg nozzle separator varies from 40 m³/h to 160 m³/h (or between 176.11 gpm and 704.46 gpm).
What about the maintenance of the nozzle separator?
Our separation technology specialists placed great value upon a maintenance-optimized construction during the design phase. "For us, this means not only optimal maintenance but also the general avoidance of parts subject to wear or requiring maintenance," explains Matthias Gaube. Our contactless sealing system, for example, enabled us to significantly reduce potential wear, right from the design stage. Even the required maintenance work has been optimized to the greatest possible degree. For example, the lubrication unit and the flat belt of the drive are easily accessible through maintenance openings in the transmission housing. In particular, I would like to highlight our compact spindle drive. Thanks to our clever design, it can be loosened with just four screws, allowing it to be quickly replaced if necessary.
What do the initial tests reveal?
Since this is a new separator, we were prepared to make some changes during the first tests. But the very first attempts proved us wrong. Within the first hours of operation, we were able to integrate our separation unit into the processes of our test partner, who is now the owner of our first FDS2000. We were delighted to find out that our nozzle separator far exceeds our self-imposed efficiency targets.
What was the customer's first impression?
I think the fact that our test partners chose a Flottweg nozzle separator after the tests shows how enthusiastic our customers are. The results that we were able to achieve in the tests were consistently positive, and this naturally also impresses our customers.
To conclude, can you please describe the nozzle separator in just a few words?
Powerful – Energy-Saving – Maintenance-Optimized