2022-08-03
When starch is separated from wheat – Flottweg’s starch process at Viresol
As a versatile raw material, wheat starch is an important natural product for the food industry, for animal feed production and in the paper industry. As the third most important crop following corn and rice, the recycling of the entire wheat grain plays an increasingly important role. Due to the high starch content, the processing of wheat starch is particularly relevant and the production process is becoming increasingly important, particularly in the context of sustainability. This is impressively demonstrated by Viresol, the Hungarian producer of wheat starch: With Flottweg's help, the company is reducing its ecological footprint and optimizing hygienic design at the same time - killing two birds with one stone.
It is impossible to imagine bread or cake, pasta or even beer without wheat. As one of the earliest cultivated grains, wheat originated in Asia Minor and established itself as a high-yielding cereal in Central Europe from the 11th century onwards. Wheat consists of approximately 58 to 62% starch, making it a popular and economical raw material for the production of pure starch. Wheat starch can be used for a variety of purposes due to its stabilizing, thickening, gelling and binding properties. However, there are also a large number of applications for wheat starch in technical processes and in the chemical industry, e.g. in the production of paints or paper coatings.
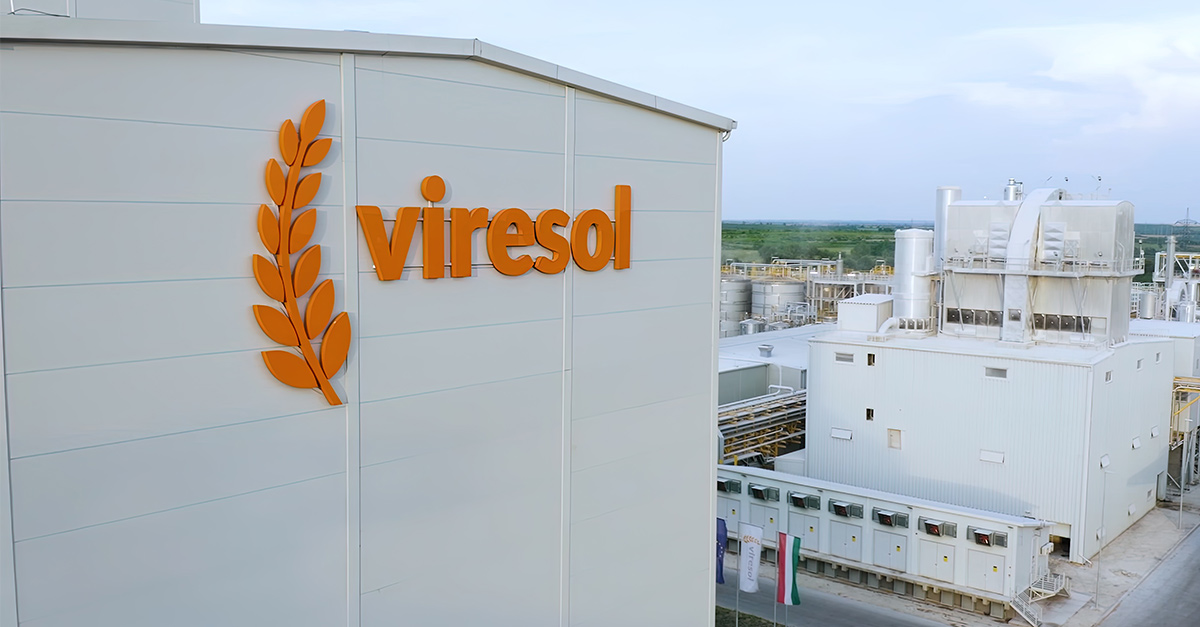
“Separation is everything” - the centrifuge as key equipment in the starch process
For starch production, wheat flour is broken down into its components: A-starch, B-starch, gluten and pentosans. In the processing of wheat, the separation of starch and wheat protein (gluten) is of particular importance. In the so-called wet process, the starch is washed out through the addition of water. Centrifuges serve as key equipment for solid-liquid separation processes and ensure maximum efficiency and high quality of the separation results. This is the only way to obtain a high-quality end product that can be used in both the food industry and in the technical sector. Therefore, all individual steps in the starch process must be perfectly coordinated. Any kind of disturbances, such as unexpected downtimes or contaminated separation results, must be avoided in order not to disrupt the continuous process. The mechanical reliability of all machines and equipment involved in the process is therefore essential.
In addition to wheat, drinking water plays an important role as a raw material in the production process: In the wet process, water is used in various steps to separate and further purify fragments such as A-starch or gluten. The use of fresh water creates waste water, which is discharged into sewage treatment plants where it is processed. This results in cost. Saving or using water more efficiently plays an important role in starch production - it reduces costs and the ecological footprint to improve sustainability. This can be accomplished with an efficient process water system that allows as much water as possible to be used multiple times during the process.
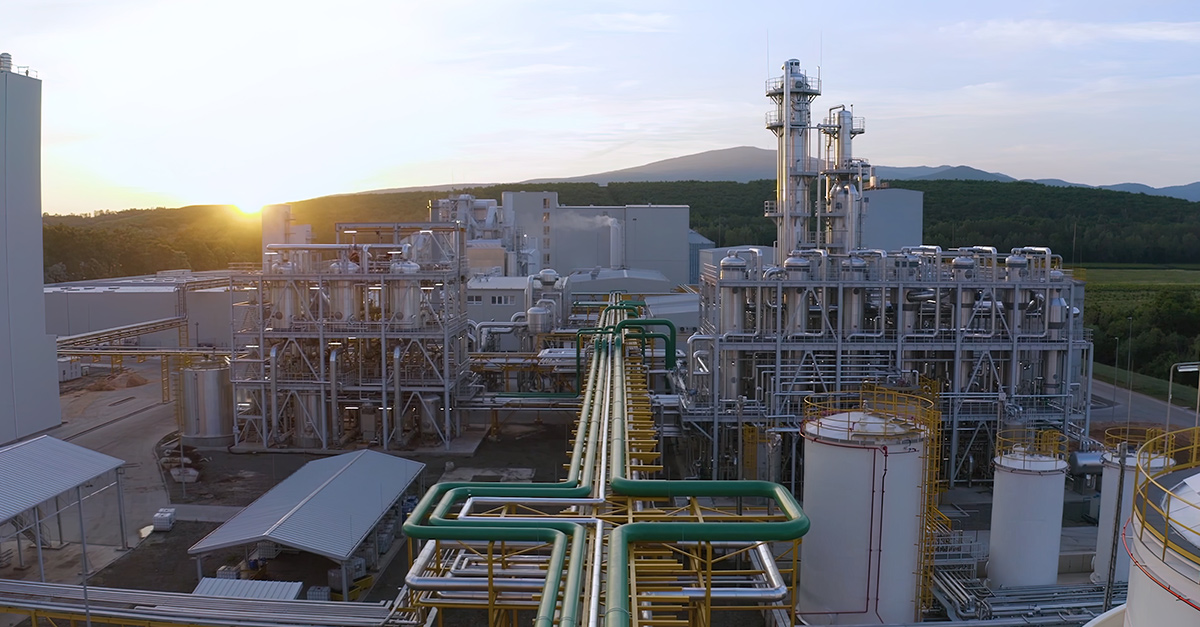
Modern, sustainable and efficient - Viresol, a producer of wheat starch
The Hungarian company Viresol is engaged in the production of wheat starch using a particularly modern and sustainable approach. Founded in 2015, Viresol combines traditional wheat processing methods with innovative and highly efficient technology. The result is the production of high-quality wheat starch with a starch content of 98%. The ecological footprint is also reduced by lowering energy and water consumption, making the entire process more sustainable. "Our company is characterized by our commitment to reducing our environmental footprint", says Gabor Kemenes, Technical Director of Viresol. Viresol uses Hungarian GMO-free wheat and thereby minimizes transport distances and fosters ties with the local region. Viresol processes around 250,000 tons of wheat annually. In addition to wheat starch for the food and paper industries, Viresol also produces wheat protein for bakery products and animal feed, as well as ethanol from B-starch/pentosan for the chemical industry.
Viresol relies on Flottweg's technologies for the long-term reduction of its ecological footprint: The wet process begins with flour dosing and ends with cleaned final products; it uses one starch and two gluten lines made up of two Tricanter® Z8E, four Decanters Z6E, two Sedicanter® S6E, together with the related process equipment. In the three-phase separation process, the Tricanter® separates the A-starch solids, the gluten / B-starch liquid phase and the pentosan liquid phase via the adjustable impeller. This first process step is essential in order to obtain an exact separation result within a few subsequent steps. To achieve the highest possible quality of the end products, the various components (A-starch, gluten and B-starch) are further differentiated and purified in separate washing and separation processes. The overall wet process sequence is precisely coordinated at Viresol in order to obtain high-quality end products and to reduce process costs.
In particular, the consumption of water - which is of great importance for Viresol's sustainability efforts - is carried out as efficiently as possible with the help of Flottweg's separation technology and plant design. A sophisticated process water system helps to ensure that the minimum amount of fresh water is used. In the gluten line, the process water is treated twice, first with the Z6E and then with the S6E. The double clarification means that the process water is particularly pure and can be largely recycled back into the process. This process significantly reduces Viresol's fresh water requirement. Flottweg's plant design therefore ensures the holistic use of water. This is also confirmed by Technical Director Kemenes: "With Flottweg's help, we were able to significantly reduce our water consumption". Viresol has reduced its environmental footprint thanks to the efficiency of the Flottweg machines and associated process water management system. For the company, this is a source of great satisfaction: “Thanks to Flottweg’s work, we at Viresol were able to achieve our goals”.
For Viresol, the use of Flottweg separation technology brings another decisive advantage: Since hygiene requirements common in food processing are also increasingly being imposed in the starch industry, compliance with these standards is essential. Flottweg offers an optimal overall concept here with hygienic design equipment and an adapted “Cleaning in Place” solution (CIP). QHS Manager Dr. Zsolt Barta particularly appreciates the cleaning options: "The CIP helps to remove sediment and residue from the machines". The temperature level, the cleaning fluid, the duration and sequence of the media to be cleaned can be individually defined. Another advantage is that the two gluten lines can be cleaned separately and thus production does not have to be shut down completely. While one gluten line is being cleaned, the capacity of the other line can even be ramped up for a short time to compensate for losses. Flottweg also supports Viresol by providing fully enclosed aggregates to higher safety standards, thereby minimizing the risk of process contamination and the exposure of operators to hazards.
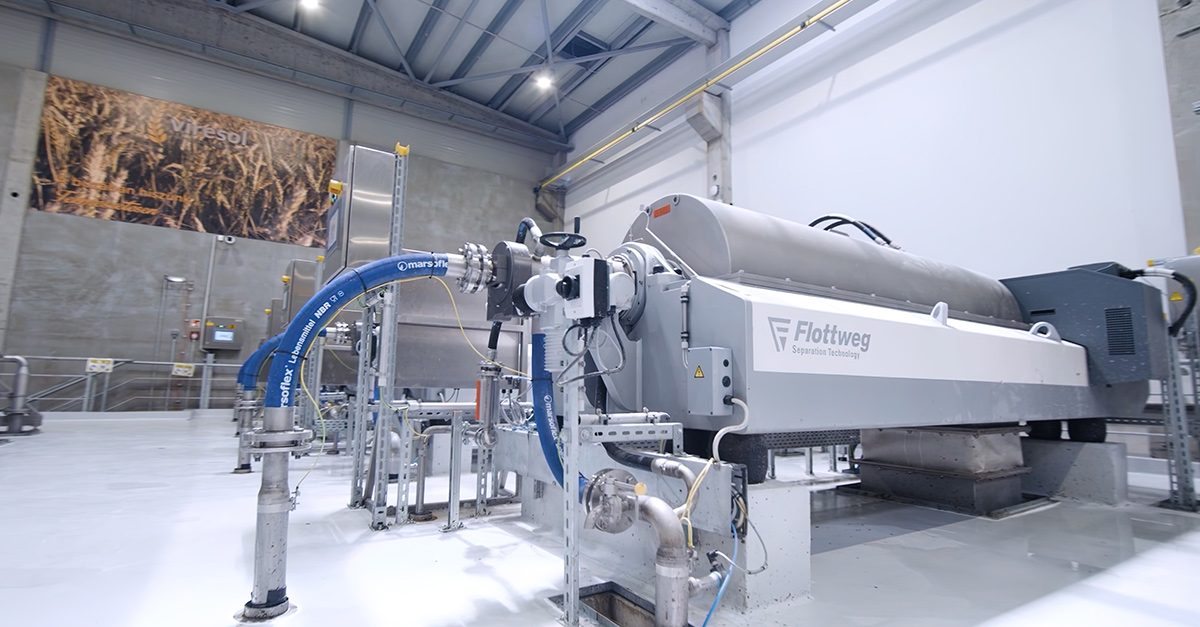
Starch good - everything good?
Wheat is an important source of starch and because of the many and varied uses of wheat starch, the manufacturing process will continue to play an important role in the future. As the Viresol example impressively shows, several different parameters are crucial for modern and efficient production. In particular, the responsible use of raw materials such as wheat and all its components, as well as fresh water, is not only crucial for reducing costs, but is also becoming increasingly relevant in an ecological context. Together with Flottweg, Viresol is a pioneer in this field and impressively demonstrates that a traditional sector such as wheat starch production can still be modern, innovative and sustainable.
Watch the video regarding the case study

Are you interested in Flottweg centrifuges for the production of starch?
Talk or write to us!