2021-08-05
Separating fish meat and oil on board a fishing vessel
The fishing vessel Starbound is a 300-foot, 1,042-ton catcher/processor that harvests Alaska Pollock in the Bering Sea and processes it on board into boneless-skinless filets, mince and surimi. Three years ago, its owner, Aleutian Spray Fisheries, Inc., decided to cut it in half to expand the processing operation and add a meal plant, oil plant and two surimi lines to the then 240-foot vessel. The retrofit was not just on the ship. It was a complete overhaul of the processing operations and required heavy-duty, highly-efficient Flottweg Decanters and a Tricanter®.
The history
Aleutian Spray Fisheries was established in 1969 by Naval Architect Henry Swasand with the acquisition of the crab vessel Aleutian Spray. As the firm grew during the 1970s, due to the rapid growth in the Bering Sea King crab fishery, other members of the Swasand family joined their father. Today, a third generation of Swasands is active in the management of Aleutian Spray Fisheries. During the crab industry's peak, the Aleutian Spray Fisheries fleet grew to include the fishing vessels Starfish, Nordic Star, Starward and Starlite. Each vessel was built in Pacific Northwest shipyards to the Swasand family's exacting specifications. Today the firm's fleet also includes three Longliner vessels as well as partnerships with two research vessels. The firm was among the pioneers of the Americanization of vast stocks of Bering Sea groundfish that had formerly been harvested, processed and marketed by foreign fleets. Rising prices of fishmeal and oil led to the ambitious retrofit of Starbound in 2016. The upgraded vessel includes onboard fishmeal and surimi processing plants.
The fishing fleet includes the at-sea processor Starbound and the mobile armada of freezer-longline and combination fishing vessels. Aleutian Spray Fisheries products are fully processed and quickly frozen or stored in refrigerated seawater. The firm participates in what are arguably the world's best managed fisheries. The Alaska Pollock Fishery has been certified as sustainable by the London-based Marine Stewardship Council.
The challenge & solution
The company catches Alaska Pollock in the Bering Sea and then processes it in a fully-functional plant onboard the ship. Three years ago, Aleutian wanted to increase productivity and diversify its production. This required installing a meal plant and an oil plant. The challenge led the company to Flottweg Separation Technology, which engineers and manufactures two-phase and three-phase separation equipment.
Onboard Starbound, the Flottweg equipment is used to separate the meat from the liquid. With the surimi lines, Aleutian also separates fish meal and fish oil using a Flottweg Tricanter® to separate the solids from the oil and the meat.
“Before we got the Decanters and the Tricanter®, we only had a recovery line. This means we only took meat off the frame,” said Karl Bratvold, operations manager of Starbound. “Three years ago we cut the boat in half and added a meat plant. We needed bigger Decanters. We changed our whole factory from just a recovery line to a primary and secondary surimi line and also added fish meal and fish oil production. The Tricanter® came into play for the fish oil. The two Decanters are for our primary and secondary surimi line.”
The need for the Flottweg equipment was based on the expansion and a need to increase productivity. “We literally cut the boat in half,” Bratvold explained. “The boat was 240-feet long. We cut it in the middle and stretched it apart and installed a 60-foot midsection in the middle of the vessel. We then added the new factory equipment and the meal and oil plant.”
The expansion project took 10 months to complete. And while Starbound performed water tests, it was impossible to test production without any fish. This meant that the first real test of the equipment happened at sea on the first fishing trip after the construction was completed. Because of this, the equipment had to be reliable. “That’s the tricky part,” Bratvold said. “You can’t test the facility if you have no fish. We re-did the entire factory. Without testing, this equipment had to work, or there was a wasted fishing trip.” The performance of the equipment exceeded expectations. “It went really smooth,” Bratvold said. “We had never used Tricanters®. The Decanters have been great and allowed us to produce even more than we expected. There is a learning curve as you go along, but from startup it’s been very smooth.”
The factory consumes an entire level on the ship. With about 130 people on board, the factory staff is about half of that. The other half is fishing crew, boating crew, cooks and other personnel. “When we return from a 10-day trip we have a 30-hour offload before going back to sea,” Bratvold said. “When we return to shore, everything has been processed. We do primary- and secondary-grade surimi on board and use the Decanters to make fish meal. We use the Tricanter® to separate the solids from the fish oil and then we also make boneless-skinless filets, and mince. When it comes back to the dock it’s ready for market.”
Product is shipped to McDonald’s, Burger King and other major chains worldwide. The meal goes to Asia and most of the oil is used domestically.
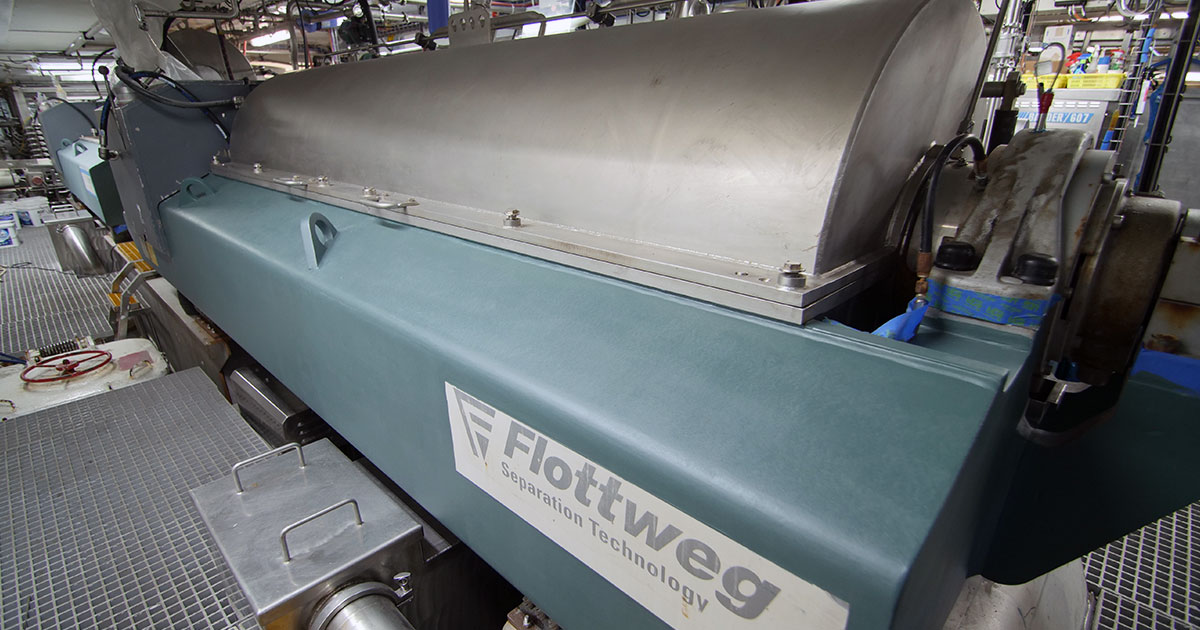
How it works
The modular design of this decanter centrifuge means it is possible to adjust optimally to all kinds of separating tasks. The Flottweg Decanter has an adjustable impeller. Normally, the clarified liquid runs out of a decanter without pressure. As an alternative, it is possible to transport the clarified liquid away using an impeller. This means it runs out in a closed system under pressure. A further development of the impeller is the adjustable impeller. In this variant, an adjustment mechanism alters the position of the impeller. As a result, the liquid can be removed at different diameters, thereby also optimizing the separating performance. An adjustment mechanism causes the position of the impeller to change, therefore changing the separation line of the liquids. The process engineering results can then be influenced to achieve the required separation result.Flottweg
The structure and function of the Tricanter® are similar to those of a decanter (two-phase separation). The decisive difference between these two machines concerns the way that the liquid is discharged. There are two liquid phases in a Tricanter®. A "heavy" liquid phase (higher density and discharged under pressure), as well as a "light" liquid phase (lower density and discharged without pressure). An adjustable impeller discharges the "heavy" liquid phase, which the operator can use to adjust the pond depth of the heavy liquid without difficulty during ongoing operation. An adjustment mechanism causes the position of the impeller to change, therefore changing the separation line of the liquids. The process engineering results can then be influenced to achieve the required separation result. This would usually require a manual adjustment of the wear plates on the rotor, which can be time consuming. Especially if you have to do it repeatedly. It would be like having to take a tire off of a car to fill it with air, then only being able to check the pressure when it is back on the vehicle.
Typical applications for three-phase separation
- Processing of sludges containing oil from refineries, oil ponds, etc.
- Extracting animal/vegetable fats and oils
- Starch manufacture for separating wheat starch and gluten
Advantages and customer benefits
- Greatest possible purity of the liquids to be separated, by using the impeller
- Other processing steps/separating stages can be dispensed with, or are no longer required, thereby offering cost savings for the plant owner
- Adaptation to changing conditions (product in the feed) possible at any time
- Automation is possible
- Produced, manufactured and developed in Germany, for the highest possible production quality
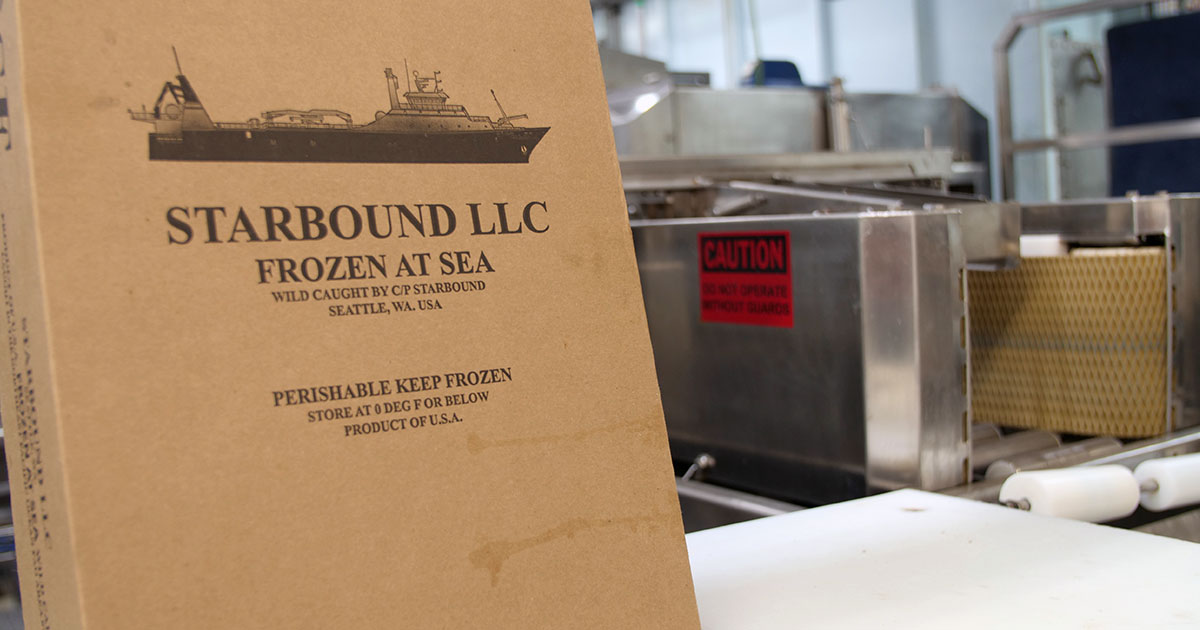
The results
“We went out to find a Decanter and Tricanter® and found Flottweg,” said Bratvold. “They have been fabulous. I appreciate Flottweg so much — from sales to parts to service. They do what they say they are going to do. They show up, and there’s been a tremendous amount of support. They listen to how you are using the machine and then adapt to it and modify it. We are in a remote atmosphere and only have a limited time, so this is a big deal for us to be able to get the parts and the service and have people respond to us. The technical support has also been great. We have questions, and they answer them quickly. We have lots of questions, so it’s been really helpful. If anyone asked me what to put on board, I’d put a Flottweg.”
About the Author
Daniel Lakovic
Daniel Lakovic is the Business Development Manager for Flottweg Separation Technology Inc. Lakovic holds a BS in International Business and an MBA in Finance.
Watch the whole video

Would you like to learn more about our solutions for processing fish?
Talk or write to us!