2021-11-23
Centrifuge system decreases required manpower, increases sludge quality
For a major wastewater treatment facility that serves five large chemical plants in West Virginia, the sludge can vary daily. This creates difficult challenges in creating a consistent sludge. After using chamber presses for decades, Solvay’s wastewater treatment plant switched to a Flottweg centrifuge system that decreased production time from 24/7 to just one 12-hour shift per day. The system also improved the quality of the sludge, reduced costs, reduced landfill mass, and provided the company with effective, automated, easy-to-use equipment and a net annual savings of approximately $214,000.
The Challenge
Wastewater produced by chemical plants contains very few fibers, so dewatering the sludge is difficult.
“We have a lot of different batches here, which change day-to-day and month-to-month,” said Brian Smith, maintenance and wastewater treatment superintendent. “This makes it difficult to keep a healthy biomass. The biomass is constantly changing. We see many different food groups. The food can swing very quickly, which makes it very difficult to develop a consistent sludge. When we go out to start the centrifuge every morning, you just don’t know what we will have. It’s different every day.”
This is a common challenge for treatment plants when there are batches from multiple sources and very little, if any, equalization. The manufacturing plant discharge, will hit the treatment plant within an hour of its discharge, and Smith said his facility does not have large equalization ponds.
To make a consistent sludge requires a consistent waste. “If everyone sends a consistent waste, then the bugs would acclimate to it,” Smith said. “You could grow a healthy bug that would settle. But when you constantly change the pH and the chemical feed, you have some bugs that are dying and other bugs that are increasing in population. This type of sludge is extremely difficult to dewater.”
Solvay previously used two chamber presses, but they could not always handle the capacity. Smith was forced to rent an additional chamber press for six months of every year, running all of them 24 hours per day, seven days each week. This created a need for an additional operator, as well.
“This created a huge stress on our manpower,” Smith said. “We had operators who focused solely on the presses. Since our sludge is so difficult, for every ton of sludge we produced we had to add one ton of fly ash. This increased the amount of tons that we had to send off to the landfill. It was a very dry material. We could get close to 50% solids, but when you take into account that you are adding a huge amount of fly ash, that accounts for a lot of the solids.”
The chamber presses were installed in the late 1980s. During this time, the company used a hazardous waste incinerator. During the 1990s, the facility shut down the incinerator and made many changes to the manufacturing processes.
“We couldn’t dewater fast enough, so we basically just stopped wasting. That would back up all the sludge into the wastewater treatment plant, causing problems,” Smith said. “Every six months or so, we were forced to get a rental press, which would help us to bring the sludge levels back down. This put an extra cycle on the wastewater treatment plant. So, not only was our feed swinging, but now we were cycling the amount of biomass in the wastewater treatment plant. We were holding nothing steady.”
When the solids level rises in a wastewater treatment plant, costs also rise. Smith said his facility added polymer to make the sludge settle in the secondary clarifier. To prevent the solids from entering the river, they would use more polymer for thickening, which was expensive.
The Solution
Smith and his team began to research different technologies, including rotary screen filters, but the product from these machines was not acceptable. The company rented a centrifuge system, but the manufacturer was unable to provide effective service when the equipment broke down. Smith was back to square one.
In the winter of 2017, Smith connected with Flottweg Separation Technology and worked within its pilot program on a rental agreement for centrifuge equipment with a service agreement.
“The pilot unit originally came with a solid scroll, it was then exchanged for an open-bodied scroll,” Smith said. “We saw a huge improvement. The pilot unit was giving us solids at 19% to 20%. It was easy to run. You hit the start button and it began producing product right away. We began to run the open bodied scroll from April to August and it was a step change. The product was flaky and it was much easier to keep the centrate clean. It was at least 21% solids. That 1% or 2% makes a physical change in the way the sludge looks and the way it behaved. The free water was removed, and it didn’t look wet at all.”
From the beginning, Flottweg worked with Solvay on a long-term lease and was able to install the new scroll design once it was available.
“Now, it’s almost a non-issue,” Smith said. “We installed it and never have had a moment’s problem with it. It was installed in less than 8 hours. It just dropped into the same bearing housing. The solids are about 1% to 1.5% better. The operators have no issues at all. Because our sludge is so different, we just baseline the amount of polymer we are putting in it and then run the sludge feed as hard as we can until the centrate gets dirty. Then we back it off a little.”
During the day, Smith said he will start running it at around 50 gal per minute (gpm), and as the thickener pulls the sludge down—thinning the sludge in the process—he will increase it by an additional 10 gpm.
“We set our sludge wasting at 35 gal per minute, for example. It runs all day, feeds into the thickener, and the thickener dewaters,” Smith said. “So when the guys come in in the morning, they may have 10 ft of material in the thickener. They start the centrifuge and let it run 8 to 12 hours. Then they shut it down for the night. The next morning there is another 6 or 8 or 10 ft. It’s not unusual to make changes because you are batch operating the thickener. When it starts in the morning it may be 3% solids. Right before quitting time, the solids may be 1% to 1.5%.”
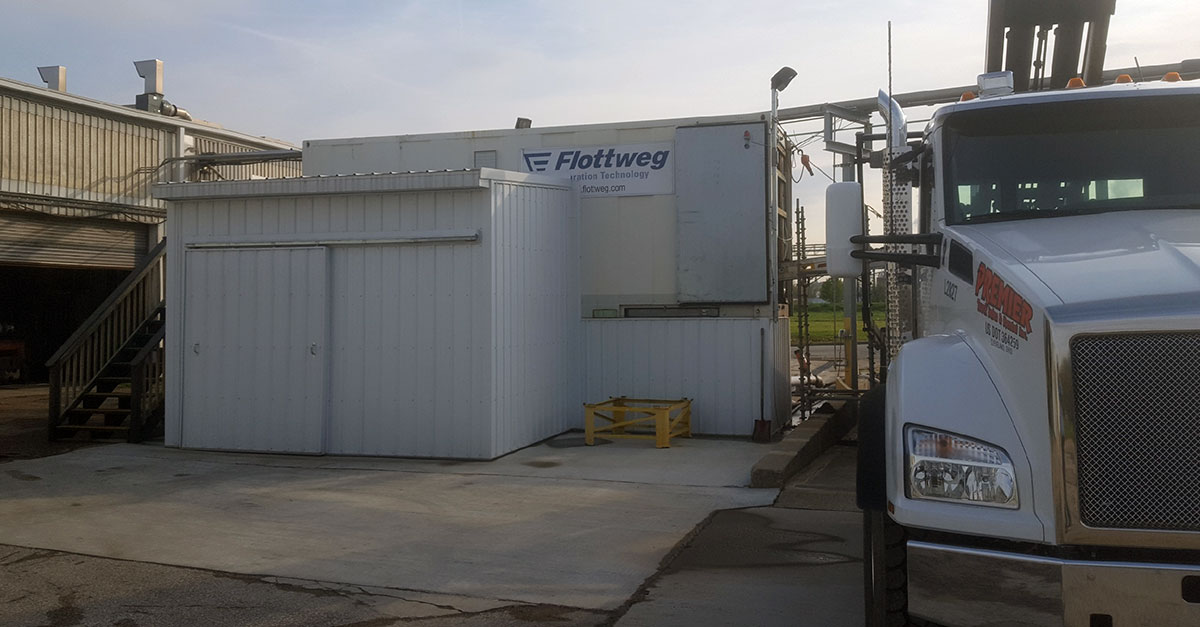
How It Works
Depending on the size of the wastewater treatment plant, there may be a variety of processes used. Although Solvay only uses centrifuges for dewatering, thickening also is possible with decanter centrifuges.
All wastewater treatment plants have some kind of thickening process. This means concentrating the surplus slurry produced in the biological stages from 5 to 10 g/L total dry solids to 5% to 8%, before it is pumped into the digestion tower. The slurry volume is reduced by 90% to 95% in this process. Solvay currently uses settling clarifiers, but also could use a centrifuge to perform this step, which is then followed by a dewatering process.
Whether the solids are transported after dewatering, reused as fertilizer, disposed of in landfills or incinerated, maximum dryness is the most critical factor. The other key factors are cost efficiency in terms of consumption of polymers, energy, water spare parts, as well as continuous, automatic operation at minimal costs.
A decanter centrifuge can be viewed as a settling pond wrapped around an axis. In the settling pond, solid particles, which are heavier than the liquid, settle to the bottom driven by gravity and build up a sediment layer on the bottom of the pond. In the rotating bowl of the centrifuge, solid particles, which are heavier than the liquid, move to the inner diameter of the bowl driven by centrifugal force and build up an annular sediment layer on the inner surface of the centrifuge bowl. Since the centrifugal force in the decanter is approximately 3,000 x g instead of 1 x g in the settling pond, separating solid particles from a liquid in a centrifuge becomes faster and more efficient.
The bowl shell of a decanter centrifuge has a cylindrical, conical shape. It rotates at a high speed, creating the centrifugal force needed for the separation. Inside the bowl, there is a scroll conveyor for the continuous discharge of the sediment, which is packed on the inner surface of the bowl wall. The scroll conveyor rotates at a speed relative to the bowl speed. This differential speed is created by a rotating gear box at the drive end of the bowl. The sludge to be separated enters the bowl via a stationary feed pipe. From the feed pipe it enters the separation zone in the scroll body. In the separation zone, it separates into a sediment layer and a liquid layer. The sediment is scraped off the bowl wall via the scroll conveyor and delivered out of the pond on the conical end of the machine before it leaves via discharge ports on the conical end of the bowl. The separated liquid flows to the cylindrical end of the bowl where it is discharged by gravity via an overflow weir.
These critical design features have been considered since the beginning of the 1970s. Today, the result of this continuous development is the complete Flottweg HTS decanter portfolio for sludge dewatering which includes equipment to handle capacities of 40 to 800 gpm.
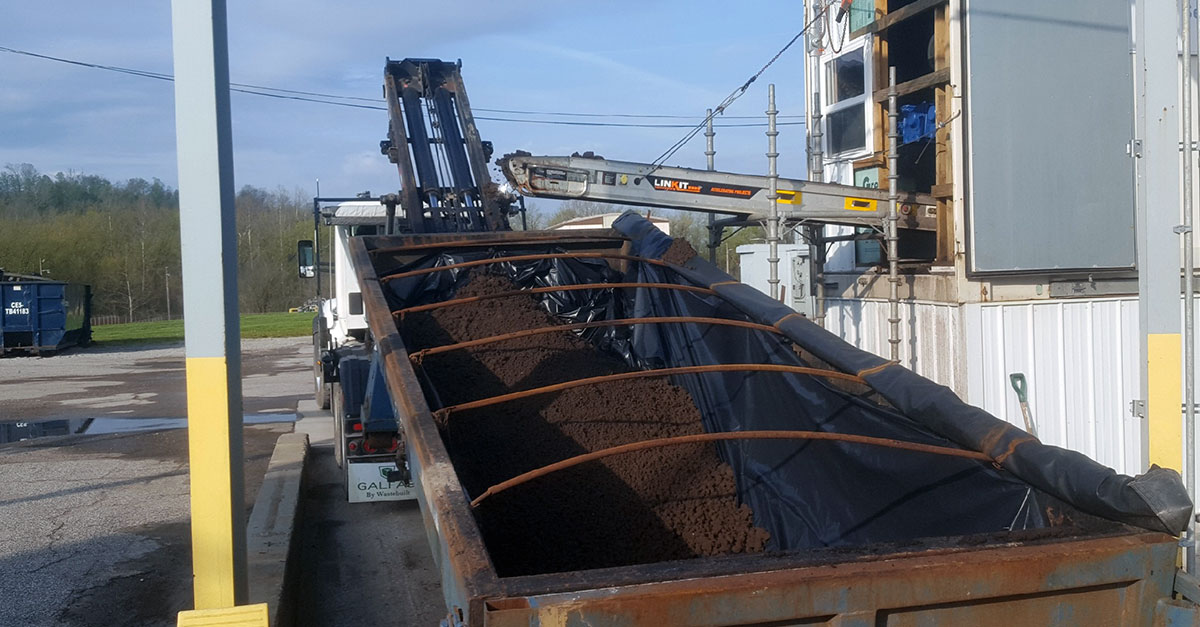
The Results
The centrifuge system allowed the Solvay Wastewater Treatment Plant to reduce man-hours used with the dewatering equipment, reduce operation time and tons of landfilled material, increase sludge consistency, and reduce energy.
“Our unit right now is a rental, but we hope to own it one day,” Smith said. “I tease the guys that it’s a rental, but they would kill me if I take this away from them. They would guard it at the gate. They could never go back to the old technology after using the Flottweg centrifuge. This technology has been proven at least 15 years, and we are just happy that we finally discovered it.”
The system allowed Solvay to decrease operation time from 24/7 with full-time dedicated operators, to just one 12-hour shift per day. Chamber presses required a lot of physical work, namely scraping and moving the plates, Smith said. This caused shoulder injuries and upper body strain. The centrifuge system decreased the need for additional manpower and also reduced the risk of injury for the operators.
“It was nice to get rid of the overtime,” he said. “We redirected the extra man-hours to other parts of the wastewater treatment plant, improving our operations and effluent quality. Once we got it started and going, it’s been very easy. Solvay and Willow Island is a site for growth. We want to expand. Before, we were concerned that the wastewater treatment plant couldn’t handle additional loading. Now, this is a non-issue. The centrifuge and the fact that we now have control of the wastewater treatment plant just confirm that this site is open for growth.”
The plant no longer needs to add fly ash to the centrifuge, which saves the cost of fly ash, hauling cost and tipping fees. In total, the plant was able to see a return on investment within a few months. After the first year in operation, the system proved its worth by saving Solvay more than $214,000 annually. This number includes costs for ash, ash transport, landfill transport, disposal, polymer, rental, rental labor, rolloff boxes, a rolloff truck, a plastic liner, maintenance and electrical expenses.
“The major benefit is I get to control the wastewater treatment plant,” Smith said. “We don’t allow those solids to go really high. We set them where they need to be. My polymer costs on the wastewater side has really fallen. Our operator only needs to start the centrifuge in the morning and move the dumpster with only a few minor adjustments.”
About the Author
Daniel Lakovic
Daniel Lakovic is business development manager for Flottweg Separation Technology.

You would like to know more about our solutions for waste water treatment plants?
Talk to us or write us!