18.04.2024
Risoluzione dei problemi idrici per miniere e cave - Utilizzo della tecnologia delle centrifughe con una stazione di chiarificazione e dosaggio dei polimeri
Con l'invecchiamento delle miniere e delle cave, i minatori e gli operatori si trovano ad affrontare problemi idrici derivanti dal lavaggio e dalla lavorazione del prodotto. Questi problemi includono la carenza di bacini e la necessità di estrarre dai bacini esistenti, la carenza di acqua dovuta a restrizioni, le limitazioni imposte dalle specifiche sull'acqua destinata a essere reimmessa nelle acque sotterranee o persino l'eccessiva quantità di acqua contaminata da argille e solidi ultrafini.
Tradizionalmente per risolvere questi problemi si ricorreva a presse filtranti e/o bacini di decantazione. Ma questi metodi non solo richiedono un notevole investimento di capitale, bensì comportano un ingombro elevato, una presenza costante dell'operatore e spese d'esercizio continue associate ai mezzi filtranti. Presse e bacini di decantazione non sono portatili e i costi civili/strutturali che comportano si aggiungono alle spese in conto capitale. In alternativa, semplicemente inviare gli sterili a un bacino di decantazione non è una soluzione ottimale, in quanto questa pratica è rischiosa e spesso determina la messa in quarantena degli impianti di estrazione.
In questa sede intendiamo studiare un'alternativa affidabile ed economica, attraverso l'esame obiettivo di due sperimentazioni condotte con un impianto pilota composto da un'unità di chiarificazione/dosaggio dei polimeri e una centrifuga decanter progettata specificamente per resistere alle difficoltà di un'attività mineraria. L'impianto pilota è stato in funzione in parallelo con una pressa filtrante di dimensioni equivalenti; i due macchinari sono stati utilizzati per un'unica attività per una settimana e poi in due luoghi separati per un'altra settimana. In entrambi i test, il risultato è stato: solidi estremamente secchi, uso minimo di polimeri e centrato pulito.
Introduzione
Nel corso di luglio e agosto 2022, sono state eseguite operazioni pilota in due siti separati e indipendenti di impianti di lavaggio sabbia e ghiaia nel sud-est del Wisconsin. Il Sito Uno si trovava presso la Lisbon Pit di Lannon Stone Products, Inc. nel Sussex WI e viene qui indicato come "Lannon." Com'è tipico della regione, il sito minerario presenta la consueta miscela di formazioni di origine glaciale, inclusi sedimenti, argille e depositi morenici che ricoprono il calcare dolomitico. La pietra calcarea contiene diverse quantità di selce e argille.
La miniera di Lannon produce una pietra dimensionale da costruzione, nonché sabbia e ghiaia. La ghiaia va dal pietrame alla ghiaia fine e a un mix di pietra frantumata e ridotta in polvere. La sabbia è classificata in base a vari gradi a seconda dell'applicazione, ovvero sabbia di calcestruzzo lavato, sabbia per muratura, sabbia per letti di posa, sabbia per campi da golf e sabbia ultrafine lavata. Lannon invia l'acqua di lavaggio usata al suo chiarificatore. Qui si procede al dosaggio del polimero tramite una stazione di dosaggio di Clearwater Industries Inc., quindi l'acqua viene lasciata riposare nel chiarificatore.
Il flusso eccedente del chiarificatore viene inviato direttamente all'impianto di lavaggio, mentre il sottoflusso del depuratore può seguire due diversi percorsi. Quasi la metà del sottoflusso viene inviata direttamente alla nuova filtropressa a camera da 2 metri x 2 metri e la quantità rimanente viene deviata nei tradizionali bacini di decantazione/raccolta. Proprio questo sottoflusso deviato ha fornito l'alimentazione per la centrifuga.
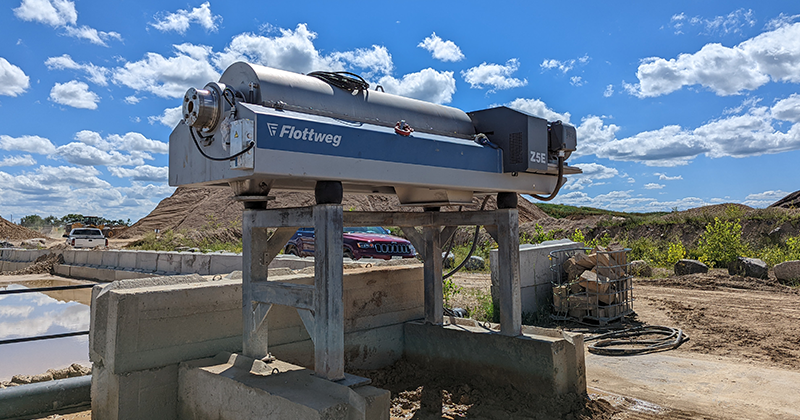
Il Sito Due si trovava presso la struttura di lavaggio centrale di Arlington, Tri-County Paving, Inc., ad Arlington WI, ed è qui indicato come "Tri-County." Esso funge da impianto generale di ricezione, raccolta, miscelazione e lavaggio per numerose cave e miniere, sia all'interno che all'esterno delle operazioni di Tri-County Paving. Di conseguenza, la gamma di minerali sarà leggermente più ampia rispetto a quella di Lannon ma, in base alla geologia del luogo, la miscela di base dello strato di materiale morenico che copre il calcare dolomitico costituisce ancora la maggior parte dei materiali lavorati.
Le sofisticate attrezzature di miscelazione e carico di Arlington consentono a Tri-County di offrire ai clienti dello stabilimento prodotti conformi a specifiche molto precise con tolleranze ristrette. L'acqua proveniente dall'impianto di lavaggio della sabbia viene nuovamente trattata da un'unità di dosaggio dei polimeri di Clearwater Industries prima di essere inviata al chiarificatore Clearwater. L'acqua in eccedenza recuperata dal chiarificatore viene restituita al bacino di raccolta dell'acqua di lavaggio, mentre il sottoflusso viene inviato direttamente a una delle due dighe di decantazione per far fuoriuscire l'acqua in eccesso. Ancora una volta, il sottoflusso del chiarificatore è stato utilizzato per fornire l'alimentazione di ingresso alla centrifuga. Si trattava di una quantità di solidi in ingresso decisamente superiore rispetto a quella del sito di Lannon (generalmente vicina al 55% di DS in massa).

In entrambi i casi (Lannon e Tri-County), esisteva la stessa necessità di separazione: estrarre l'acqua di lavaggio della sabbia dall'argilla e dai sedimenti ultrasottili, in modo da poterla riutilizzare. Tutta la sabbia viene lavata nell'impianto di lavaggio e, a seguito di ciò, l'acqua di lavaggio risulta contaminata da materiale organico, residui di sabbiatura, argille e particelle ultrasottili.
Raccogliere quest'acqua contaminata in bacini evaporitici era dispendioso e lo spazio dedicato a questi bacini poteva essere utilizzato in modo più redditizio per le future operazioni di estrazione. Inoltre, l'acqua non poteva essere reimmessa nelle falde acquifere sotterranee nella sua forma attuale. In entrambi i casi, i proprietari della miniera hanno scelto un chiarificatore alimentato da un'unità di dosaggio dei polimeri di Clearwater Industries per un dosaggio accurato dei flocculanti.
Scopo delle prove pilota
Lo scopo principale dei test pilota era quello di illustrare che la combinazione di una centrifuga con un chiarificatore adeguato e una stazione di dosaggio dei polimeri correttamente calibrata può consentire di
- recuperare l'acqua di lavaggio peril riutilizzo,
- produrre solidi sufficientemente secchi da poter esseremovimentati mediante scarico anziché mediante pompaggio,
- ridurre o eliminare completamente la necessità di ricorrere a un bacino di decantazione, il tutto
- realizzando un processo economicamente conveniente e con una supervisione minima.
L'unità pilota ha raggiunto prestazioni operative ottimali in entrambe le prove entro poche ore dall'installazione, superando i parametri target del test. Si è colta l'opportunità per testare diversi scenari utilizzando diverse velocità di alimentazione e velocità del tamburo e della coclea della centrifuga. L'obiettivo era verificare se fosse possibile ottenere diverse combinazioni ottimali di velocità di alimentazione/velocità differenziale tra il tamburo della centrifuga e i giri/min della coclea.
Sono state esaminate anche le variazioni nel dosaggio dei polimeri, per accertare se vi fosse più di un'impostazione di produzione ottimale per ogni volume/velocità. Per ciascuna impostazione, la limpidezza del centrato risultante (scarico liquido) e il grado di secchezza dei solidi (DS) prodotti sono stati misurati rispetto all'alimentazione in ingresso. Sia la stazione di dosaggio del chiarificatore che la centrifuga possono essere ricalibrate rapidamente, consentendoci di analizzare in ogni sede 18 possibili scenari secondo l'approccio predittivo "what-if".
Metodologia
La centrifuga decanter Flottweg modello Z5E-4/451 selezionata era dotata di un pacchetto antiusura per attività minerarie per garantire che il tamburo, la coclea e tutti i punti di ingresso e uscita dell'unità siano protetti dall'usura da scorrimento che tipicamente insorge a causa del materiale minerario presente nel sottoflusso di un chiarificatore.
I test pilota includevano la centrifuga decanter, il suo supporto di sollevamento in acciaio e il suo pannello di comando. Era compresa anche una pompa di alimentazione dal magazzino dell'OEM, completa di un piccolo serbatoio di alimentazione. La pompa di alimentazione è importante per mantenere una pressione positiva sul flusso di alimentazione. Il piccolo serbatoio di alimentazione (sebbene di solito non necessario per scopi di prova) era pratico in quanto consentiva l'accesso dall'alto ed era comodo per il team monitorare visivamente l'alimentazione, confermando le letture visualizzate dal densimetro.
Il flusso di alimentazione alla centrifuga disponeva della seguente strumentazione in linea in tempo reale: -
- un densimetro che registra la percentuale di solidi sospesi nel flusso in ingresso,
- un rilevatore di volume che registra i galloni statunitensi al minuto del flusso di alimentazione totale e
- un rilevatore di volume che registra i galloni statunitensi al minuto di soluzione polimerica alimentata nel flusso di alimentazione. Quest'ultima linea era monitorata anche dall'unità di dosaggio dei polimeri di Clearwater Industries Inc, che ha erogato il polimero in modo molto accurato in questa linea e quindi nel flusso di alimentazione.
Il pannello di comando della centrifuga è collegato a tutta la strumentazione e monitora tutti gli aspetti del funzionamento. Le regolazioni immediate e automatiche vengono effettuate per tenere conto delle variazioni nel volume o nella densità del flusso in ingresso: i controlli principali selezioneranno tutte le modifiche necessarie nei giri/min del tamburo e/o della coclea, oltre alla loro velocità differenziale, nonché la quantità di dosaggio del polimero per mantenere il prodotto allo stato stazionario. Anche i cuscinetti vengono monitorati per rilevare eventuali variazioni di vibrazione, così come l'alimentazione elettrica.
In caso di perdita di potenza, la centrifuga interromperà automaticamente l'alimentazione in ingresso e svuoterà il tamburo dai solidi. Alla ripresa dell'alimentazione elettrica, l'unità ritornerà automaticamente allo stato di produzione costante, indipendentemente da quale parte del ciclo di spegnimento venga interrotta.
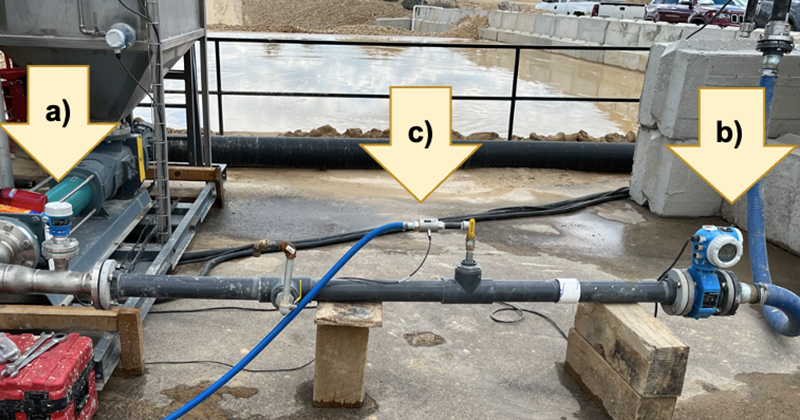
Analisi
In ogni sito è stato istituito un laboratorio sul campo per analizzare i solidi secchi (DS) per i campioni di materiale in ingresso, centrato e cake. Sono stati prelevati campioni doppi per i laboratori Flottweg, dove sono state condotte ulteriori analisi, tra cui quella relativa ai solidi sospesi totali (TSS) dei campioni di materiale in ingresso e di centrato. Per le prove di Tri County, un campione di materiale in ingresso e un campione di centrato sono stati inviati al laboratorio Clark Testing per l'analisi della distribuzione granulometrica negli Stati Uniti, mentre per le prove di Lannon sono stati misurati dal laboratorio di Flottweg in Germania.
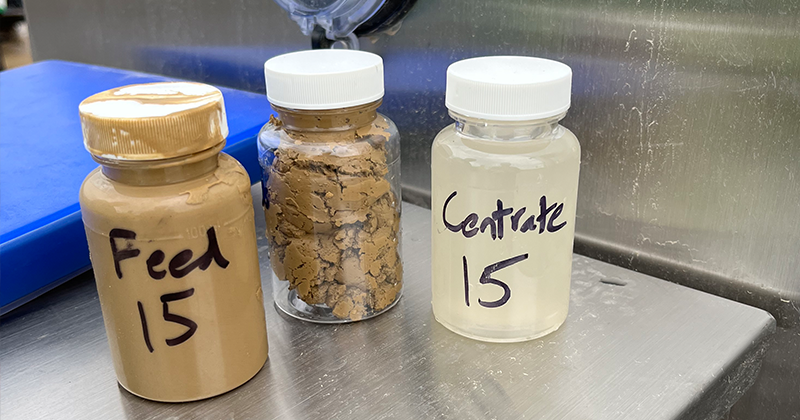
Il sottoflusso è stato convogliato dal chiarificatore ad un semplice serbatoio di raccolta, per consentire all'operatore di ispezionare visivamente il materiale in ingresso. Ribadiamo ancora una volta che questo serbatoio non è solitamente necessario, ma è stato scelto per i test pilota semplicemente perché era presente sullo skid della pompa di alimentazione. Il contenuto di questo serbatoio di raccolta è stato quindi continuamente pompato fuori dal punto di prelievo sulla linea. La pressione di alimentazione era trascurabile; è stata applicata una pressione positiva pari a uno o due bar (15-30 psi), per garantire un'alimentazione sufficiente della centrifuga.
La centrifuga scarica sia i flussi solidi che i flussi liquidi per effetto della gravità. Il campionamento periodico del flusso di alimentazione, oltre che dei solidi e del centrato prodotti, è stato opportunamente effettuato nei punti rilevanti delle prove. I campioni sono stati inviati anche a un laboratorio esterno per ottenere i dati sulla distribuzione granulometrica (PSD) come segue:
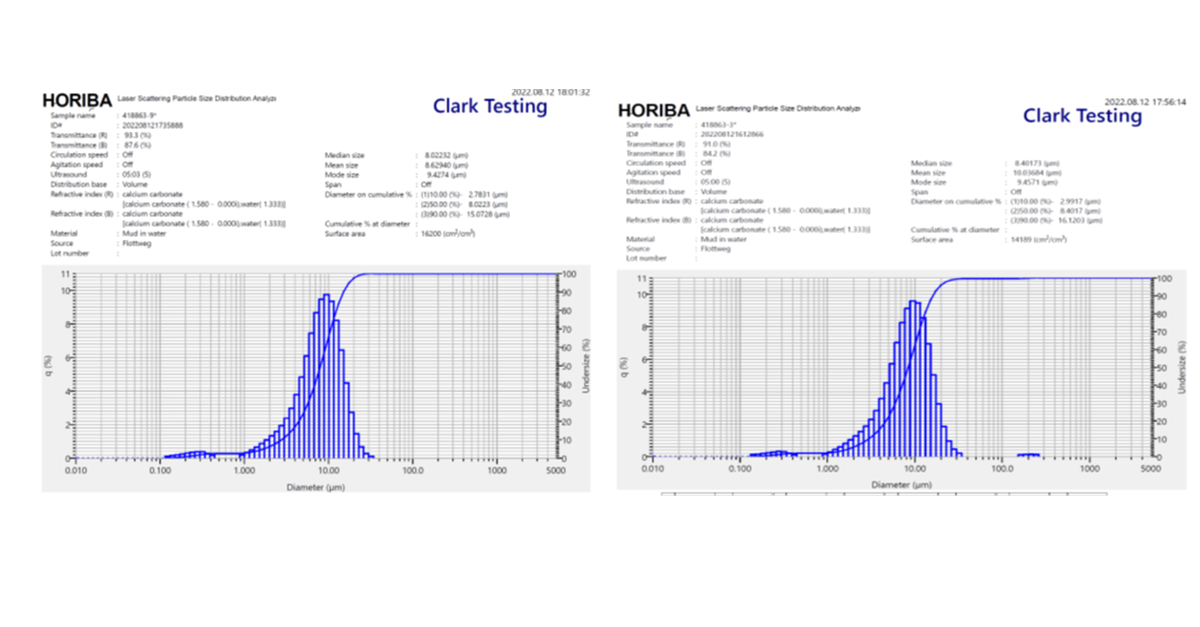
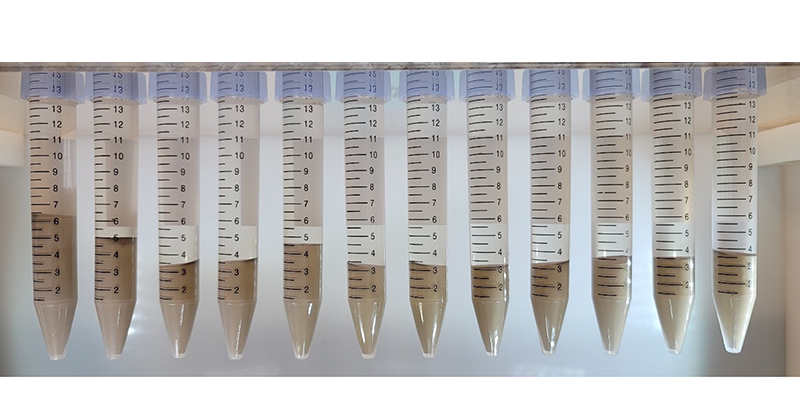
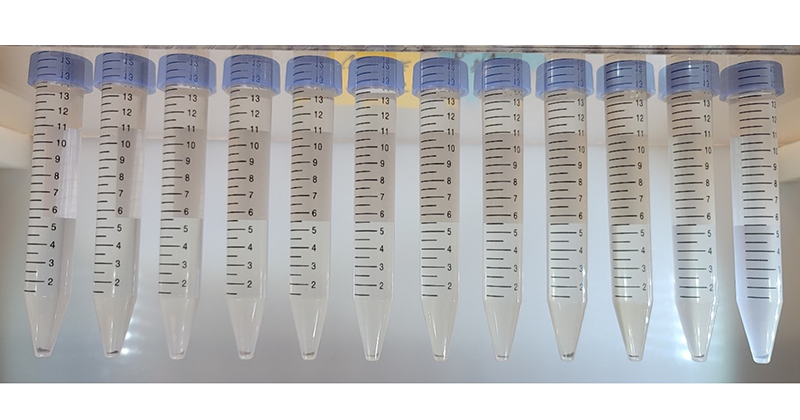
Preparazione dei polimeri
Il polimero è stato preparato utilizzando un sistema di preparazione di polimeri Clearwater. Il polimero secco utilizzato era CW95V a Tri County e CW16 a Lannon. Durante il test pilota è stata preparata e utilizzata una soluzione polimerica con una concentrazione attiva dello 0,25%. Il consumo di polimero è stato quindi calcolato in base alla portata della soluzione polimerica e alla portata dei solidi secchi in entrata. Le unità per il consumo di polimeri sono espresse in libbre di polimero attivo per tonnellata di materia secca solida in entrata (lb. ap/tonnellata di materia secca).
Qualità di separazione
La qualità della separazione viene valutata in base al recupero dei solidi sospesi, alla percentuale di solidi totali nella cake disidratata e al consumo di polimeri. La regolazione dei parametri operativi determinerà la qualità di questi criteri. La qualità del recupero dei solidi può essere valutata visivamente. Questo rapido feedback fa sì che il processo di ottimizzazione possa concentrarsi sulla produzione di solidi caratterizzati dal massimo grado di secchezza e un centrato accettabile.
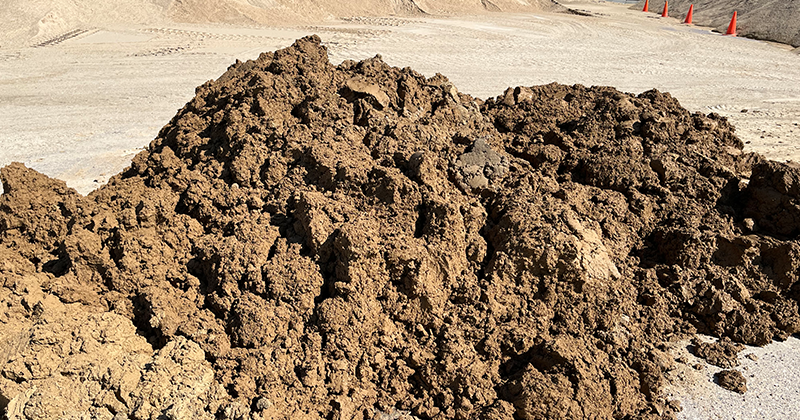
Risultati
Gli intervalli di parametri e le prestazioni ottenute sono mostrati nelle Tabelle 1 e 2. Tutti i risultati delle singole sperimentazioni sono riportati nell'appendice. Si noti che la Prova 8 a Tri County presentava un centrato visibilmente scarso e la Prova 13 nello stesso sito ha mostrato un errore relativo alla lettura della DS, per cui i campioni non sono stati prelevati.
Tabella 1. Intervalli dei parametri operativi.
Velocità/accelerazione del tamburo | 1292 - 1838 | giri/min |
494 - 999 | x g | |
Velocità di alimentazione (min-max) | 26 - 90 | gpm |
1578 – 18,739 | secco lb/h |
Tabella 2. Intervalli di prestazioni raggiunte.
Centrato | 0,040 – 0,221 | % TS |
0,001 – 0,155 | % TSS | |
Cake | 69,3 – 77,1 | % TS |
Recupero (TSS) | 99,9 – 100 | % |
Forza di gravità
L'impatto della forza di gravità sulle prestazioni viene esaminato regolando la velocità del tamburo e mantenendo costanti le condizioni e i parametri di funzionamento. La coppia viene quindi regolata in modo da poter ottenere la cake più secca. I solidi contenuti nella cake variavano da 69,3 a 77,1% in massa di TS e la cake risultava più secca se si applicava una forza di gravità più elevata. I risultati sono riportati di seguito:
Dosaggio dei polimeri
Poiché il polimero lega insieme i solidi, la quantità di polimero dosata influenzerà il grado di separazione ottenibile. È possibile stabilire una curva polimerica variando il consumo di polimero e mantenendo costanti i parametri e le condizioni di funzionamento, che possono essere utilizzati per trovare una finestra di dosaggio ottimale del polimero. Si è accertato che la dose ottimale di polimero corrisponde a 0,20 – 0,27 lb ap/tonnellata di materia secca, mentre l'essiccazione della cake è risultata leggermente inferiore quando il dosaggio del polimero è stato aumentato a oltre 0,35 lb ap/tonnellata di materia secca.
Questo volume molto basso di polimero necessario per produrre costantemente la percentuale di solidi secchi ottenuta è stata una piacevole conferma del fatto che le velocità di dosaggio, solitamente molto più elevate, utilizzate nel settore nelle separazioni assistite sono eccessive e ostacolano la separazione in caso di sovradosaggio. Una prova accurata al momento dell'installazione iniziale garantirà un'eccellente separazione a basso dosaggio.
Conclusione
Una centrifuga decanter combinata con un'unità di chiarificazione/dosaggio dei polimeri è una soluzione molto conveniente ed efficace per risparmiare fino al 90% di spazio, o anche di più, nei bacini di decantazione. Può essere recuperata fino al 90% dell'acqua di lavaggio di processo. Viene prodotto materiale solido prelevabile adatto alla movimentazione con nastro trasportatore o autocarro. Una centrifuga decanter adeguatamente protetta dall'usura, utilizzata in combinazione con un chiarificatore/un'adeguata unità di dosaggio dei polimeri, si dimostra estremamente efficace per il recupero dell'acqua riutilizzabile dal processo di lavaggio di sabbia e ghiaia. I risultati ottenuti in queste sperimentazioni statunitensi sono al 100% in correlazione con i risultati ottenuti nelle tante installazioni odierne presenti in Europa.
Quasi tutti i solidi in sospensione (99,9%) vengono rimossi dall'acqua di lavaggio, la materia solida prodotta è prelevabile e può essere rimossa tramite nastro trasportatore, convogliatore a coclea o autocarro. Allo stato stazionario, il grado di secchezza della materia solida può variare da ≥ 69% fino a un massimo del 77% (massa DS).
Il dosaggio di polimeri necessario per facilitare la separazione è stato minimo. Normalmente ci si aspettano 500 g per 2 kg per tonnellata di materia secca. La centrifuga è stata in grado di ottenere un recupero dei solidi pari al 99,9% e una cake disidratata con TS compreso tra il 69% e il 77% a dosaggi di polimeri di 0,17 – 0,44 lb. ap/tonnellata di materia secca (77 g – 199 g per tonnellata di materia secca). Sono state ottenute velocità di alimentazione costanti comprese tra 26 e 90 gpm (tra 98 e 341 lpm ). Ciò si traduce in un valore compreso tra 5,9 e 20,4 m³/ora.
Il centrato (liquido) prodotto è trasparente e completamente riutilizzabile come acqua di lavaggio dell'impianto; in questo modo la miniera può ridurre il suo fabbisogno di acqua di lavaggio fino al 90%. Il fabbisogno energetico è costante e prevedibile. La supervisione da parte dell'operatore così come la manutenzione periodica sono minime. Inoltre il sistema è a prova di guasto, per prevenire eventuali impatti negativi dovuti a improvvisi picchi di solidi nell'alimentazione, guasti all'alimentazione o interruzioni di corrente.
Eric Gentis, Flottweg Separation Technology e Andrew Gralton, Clearwater Industries Inc.
[Contributi aggiuntivi dell'autore] Stefan Ecker, Joe Lamb, Terry Ostrom, Martin Eckl, Robert Klug, Tony Kramer e Dustin Miller di Flottweg Separation Technology e i proprietari e i team di Lannon Stone Products, Inc. di Sussex WI e Tri-County Paving Inc di DeForest WI hanno contribuito a questo rapporto