29.07.2024
L'impianto di riciclo dell'acqua dell'Ohio migliora l'efficacia e consente di risparmiare sui costi operativi
Avere una torta di solidi uniforme è solo uno dei vantaggi del passaggio alle tecnologie di separazione per un impianto di trattamento delle acque reflue che serve quasi 50.000 persone nel nord-ovest dell'Ohio. Il vantaggio aggiuntivo è un significativo risparmio sui costi, essendo necessarie meno sostanze chimiche durante il processo, che includeva l'aggiornamento da una pressa a nastro a una centrifuga decanter.
Nei primi due anni di funzionamento, l'impianto di recupero delle acque della città di Middletown, Ohio, dotato di un decanter altamente efficiente, ha ridotto i tempi di produzione di due giorni a settimana, aumentato l'efficacia e consentito di risparmiare migliaia di galloni di prodotti chimici all'anno, con un conseguente notevole risparmio in termini di costi.
Contesto
La divisione Trattamento delle acque reflue della città di Middletown, in Ohio, gestisce e cura l'impianto di trattamento da 26 milioni di galloni al giorno. La divisione protegge l'ambiente e la salute della comunità, recuperando in media 14,5 milioni di galloni di acque reflue al giorno da tutte le fonti domestiche, commerciali e industriali.
Questo processo genera due prodotti riciclati: acqua pulita che viene scaricata nel Great Miami River e circa 1.500 tonnellate secche all'anno di biosolidi lavorati, che vengono applicati sui terreni agricoli per le loro proprietà nutritive e fertilizzanti. La portata di progetto dell'impianto di riciclo dell'acqua è pari a 26 milioni di galloni al giorno. Grazie al sistema combinato, la portata può raggiungere picchi di 50 milioni di galloni al giorno.
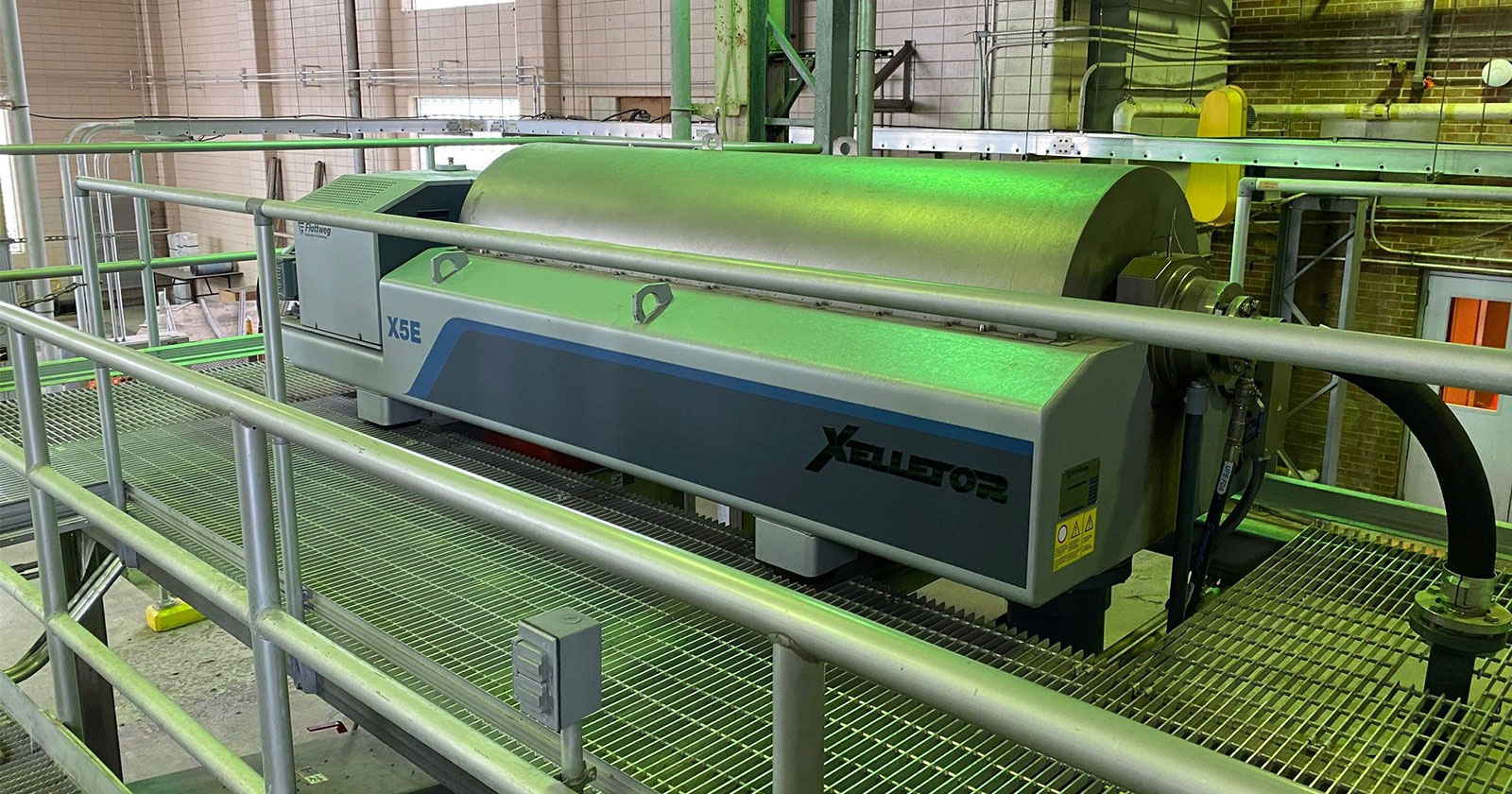
La sfida e la soluzione
In precedenza, l'impianto di riciclo dell'acqua utilizzava una pressa a nastro e una centrifuga che non funzionava correttamente. Nel 2018, hanno rimosso la pressa a nastro perché per i tecnici era difficile manovrarla e produceva solo dal 15 al 18% di solidi. Solo due anni dopo, la centrifuga produceva circa il 30% di solidi e l'efficacia continuava.
"Volevamo una torta di solidi più uniforme, in modo da ridurre i costi di trasporto", ha affermato il responsabile Gerry Burris. "Volevamo qualcosa di simile alla macchina che avevamo già, ma la nostra macchina aveva numerosi problemi meccanici e il servizio assistenza offertoci dal produttore non ci soddisfaceva."
Nel 2018, lo stabilimento ha installato una centrifuga Flottweg Xelletor ed è stato in grado di ridurre i tempi di produzione da cinque giorni a tre giorni a settimana (da 8 a 10 ore al giorno). La vecchia centrifuga è stata conservata come macchina di riserva ed è stata eliminata la pressa a nastro.
"Abbiamo smerciato il nostro prodotto anche con l'orario di lavoro ridotto, risparmiando sui costi operativi e dei prodotti chimici, che erano più elevati quando l'attività era organizzata su cinque giorni a settimana", spiega Burris. "Rispetto al passato, ora lavoriamo con consumi ridotti e una maggiore efficacia."
Stando a quanto dichiarato da Burris, si è ottenuto un notevole risparmio installando la macchina autonomamente, cosa che si è svolta senza problemi. "Abbiamo avuto alcune difficoltà di avvio, perché gli operatori credevano che la nuova macchina funzionasse come la vecchia", ha dichiarato. "Erano abituati ai comandi dell'altra macchina, ma Flottweg ha fatto un ottimo lavoro di integrazione degli schermi, rendendoli simili a quelli che gli erano più familiari. Questo ha semplificato molto la transizione."
Inoltre, il decanter più efficiente ha offerto all'impianto l'opportunità di apportare diverse modifiche al funzionamento complessivo e all'utilizzo di sostanze chimiche. "La situazione è cambiata radicalmente", ha affermato Burris. "Dopo l'installazione del decanter Flottweg, è stato possibile ottenere notevoli risparmi sull'uso di sostanze chimiche.Ora utilizziamo una quantità estremamente ridotta di polimero o cloruro ferrico."
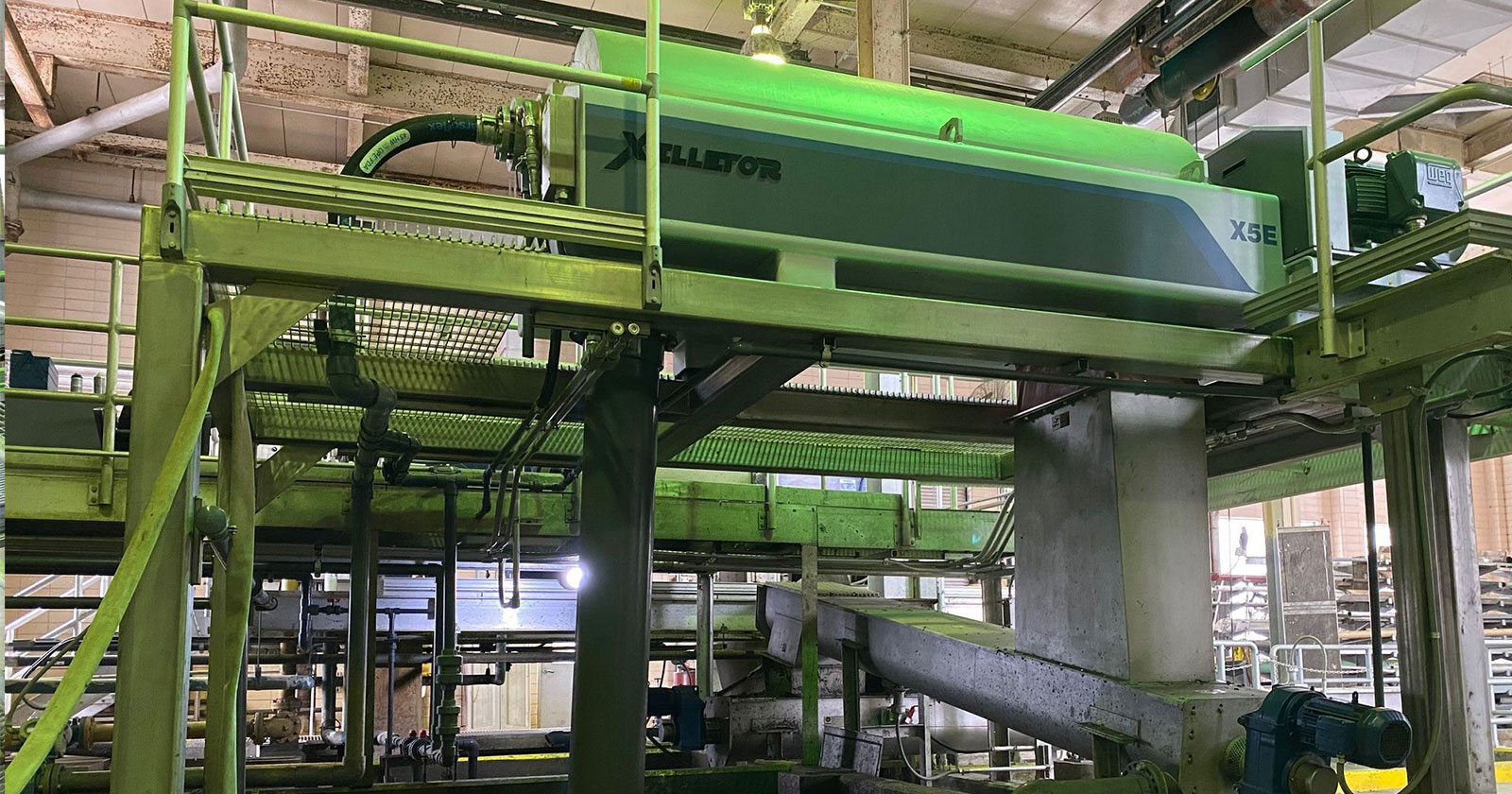
In precedenza, l'impianto di riciclo dell'acqua utilizzava una pressa a nastro e una centrifuga che non funzionava correttamente. Nel 2018, hanno rimosso la pressa a nastro perché per i tecnici era difficile manovrarla e produceva solo dal 15 al 18% di solidi. Solo due anni dopo, la centrifuga produceva circa il 30% di solidi e l'efficacia continuava.
"Volevamo una torta di solidi più uniforme, in modo da ridurre i costi di trasporto", ha affermato il responsabile Gerry Burris. "Volevamo qualcosa di simile alla macchina che avevamo già, ma la nostra macchina aveva numerosi problemi meccanici e il servizio assistenza offertoci dal produttore non ci soddisfaceva."
Nel 2018, lo stabilimento ha installato una centrifuga Flottweg Xelletor ed è stato in grado di ridurre i tempi di produzione da cinque giorni a tre giorni a settimana (da 8 a 10 ore al giorno). La vecchia centrifuga è stata conservata come macchina di riserva ed è stata eliminata la pressa a nastro.
"Abbiamo smerciato il nostro prodotto anche con l'orario di lavoro ridotto, risparmiando sui costi operativi e dei prodotti chimici, che erano più elevati quando l'attività era organizzata su cinque giorni a settimana", spiega Burris. "Rispetto al passato, ora lavoriamo con consumi ridotti e una maggiore efficacia."
Stando a quanto dichiarato da Burris, si è ottenuto un notevole risparmio installando la macchina autonomamente, cosa che si è svolta senza problemi. "Abbiamo avuto alcune difficoltà di avvio, perché gli operatori credevano che la nuova macchina funzionasse come la vecchia", ha dichiarato. "Erano abituati ai comandi dell'altra macchina, ma Flottweg ha fatto un ottimo lavoro di integrazione degli schermi, rendendoli simili a quelli che gli erano più familiari. Questo ha semplificato molto la transizione."
Inoltre, il decanter più efficiente ha offerto all'impianto l'opportunità di apportare diverse modifiche al funzionamento complessivo e all'utilizzo di sostanze chimiche. "La situazione è cambiata radicalmente", ha affermato Burris. "Dopo l'installazione del decanter Flottweg, è stato possibile ottenere notevoli risparmi sull'uso di sostanze chimiche.Ora utilizziamo una quantità estremamente ridotta di polimero o cloruro ferrico."
Come funziona la tecnologia
La disidratazione dei fanghi di depurazione offre un enorme potenziale di risparmio agli operatori degli impianti di depurazione. I costi di trasporto e smaltimento dei fanghi di depurazione disidratati rappresentano spesso l'80% dei costi operativi. A seconda della capacità dell'impianto, l'1% in più di sostanza secca nei fanghi di depurazione disidratati può consentire di risparmiare somme da cinque a sei cifre.
In una centrifuga tradizionale, la miscela liquida da separare viene introdotta nella macchina attraverso un tubo fisso. La miscela entra nella parte cilindrica del tamburo attraverso i fori presenti nel corpo della coclea e viene quindi accelerata. Grazie alla forza centrifuga, all'interno della macchina si forma un anello liquido. Lo spessore dell'anello è detto "spessore dell'anello liquido". I solidi, o fase pesante, formano uno strato concentrico sulla parete del tamburo. Per mezzo della coclea, i solidi vengono scaricati dalla macchina attraverso la parte conica. I liquidi separati vengono scaricati attraverso uno sbarramento presente all'estremità opposta.
L'angolo conico, lo sbarramento e il corpo della coclea limitano la profondità dell'"anello liquido". Un livello piatto è ideale per disidratare miscele contenenti solidi granulari, mentre un cono più angolato è più adatto ai materiali con galleggiabilità neutra, che per separarsi necessitano di un tempo d'azione maggiore. La maggior parte delle applicazioni per il trattamento delle acque reflue è adatta ai livelli profondi.
I fori nel corpo della coclea, attraverso i quali la miscela liquida viene scaricata nella centrifuga, hanno superfici dure per aumentare la resistenza all'usura. La geometria dei fori viene adattata per garantire un ingresso delicato del liquido, ma la forza di taglio viene comunque esercitata sulla miscela, riducendo l'efficacia del polimero e, quindi, anche l'efficacia della separazione.
Nel caso delle centrifughe decanter convenzionali, il corpo della coclea limita lo spessore dell'anello liquido. Grazie alla struttura Xelletor, questi limiti non esistono più. Per la prima volta, è possibile ottenere uno spessore eccezionale dell'anello liquido, il che ha un impatto positivo sulla compressione, sulla zona di chiarificazione e, in ultima analisi, sull'efficacia della separazione.
Per la disidratazione ad alto grado dei fanghi di chiarificazione è stata sviluppata un'esclusiva centrifuga. Il cuore del nuovo design, il rotore e la coclea da decanter, sono stati riprogettati da zero. Il risultato è una coclea senza corpo della coclea. Nel sistema Xelletor, il liquido viene scaricato direttamente nell'anello del tamburo della centrifuga. Il liquido viene accelerato con una forza di taglio decisamente inferiore, con conseguente riduzione del consumo di flocculanti. La regolazione completamente automatica del numero di giri del tamburo e delle velocità differenziali produce livelli ottimali di materia secca nei solidi disidratati in qualsiasi momento, anche in caso di condizioni variabili in ingresso.
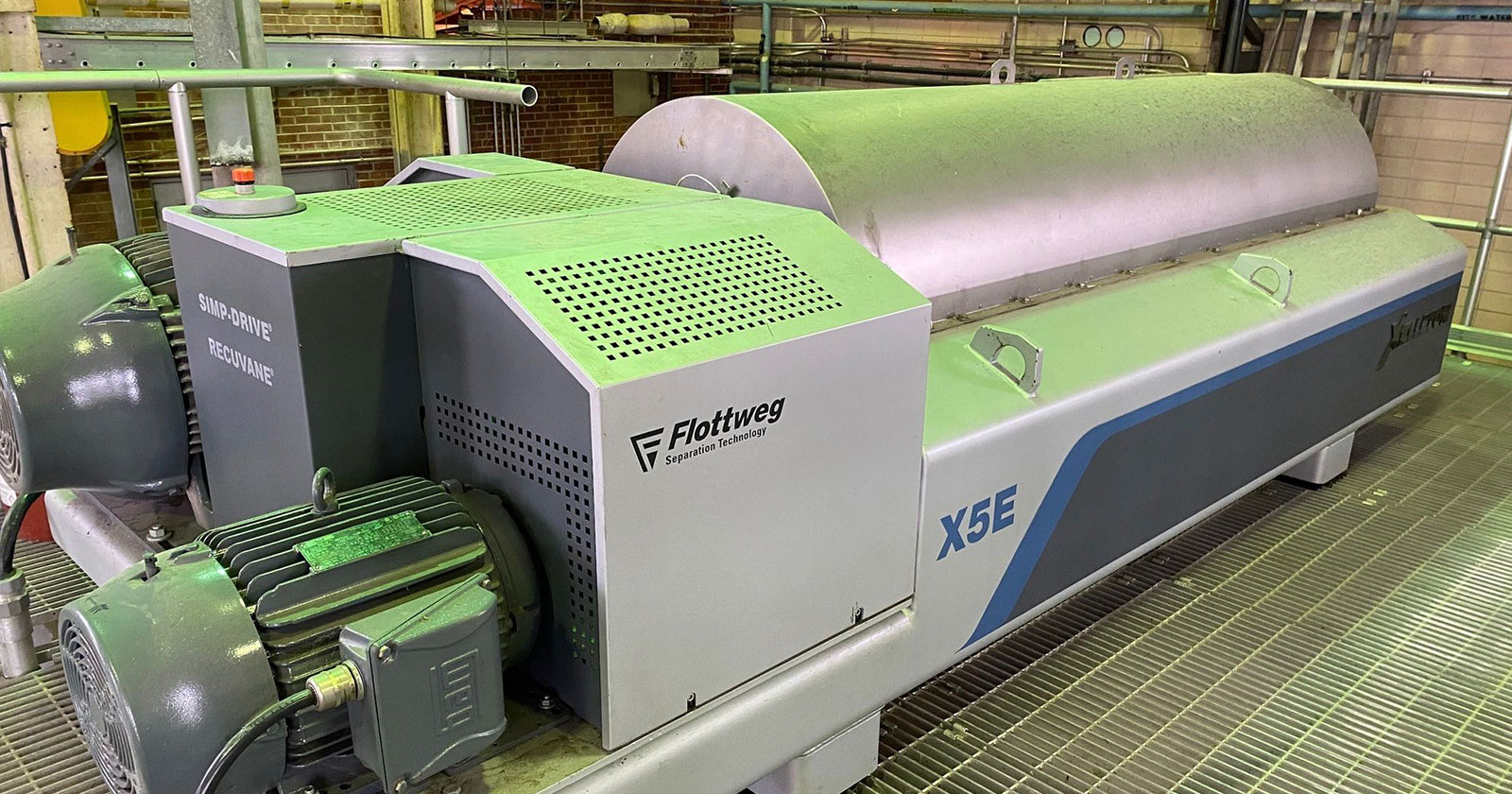
Risultati
La città di Middletown utilizza una centrifuga Xelletor dal 2018 e ha realizzato risparmi sui costi, oltre a una ottimale consistenza della torta di solidi pari al 28-30%.
"C'è stato qualche intoppo, ma il team Flottweg è stato molto reattivo", ha affermato Burris, riferendosi a un caso in cui c'è stato bisogno di un componente speciale. "Quella mattina ci siamo rivolti a Flottweg, che ci ha mandato un tecnico entro un'ora. Il nuovo pezzo è stato installato e la macchina era in funzione prima della fine del giorno. Siamo rimasti molto colpiti".
L'altra macchina forniva una torta di solidi leggermente migliore, ma per ottenere un miglioramento di circa l'1,5% era necessaria una quantità notevolmente superiore di sostanze chimiche.
"Dovevamo chiederci se avevamo davvero bisogno di un intervallo del 30-31% di solidi", ha affermato Burris. "Con Flottweg ora otteniamo costantemente una media tra il 28 e il 30% di solidi, avendo ridotto di molto il tasso di consumo. Passare a Flottweg è stata una buona mossa. L'azienda è sempre pronta a rispondere alle nostre esigenze. Inviano i loro tecnici ogni volta che ne abbiamo bisogno e rimangono fino a quando non ottengono il risultato desiderato. Per noi questo era ed è un grande punto di forza".
Per quanto riguarda la manutenzione, Xelletor non richiede molti interventi. “Dopo ogni ciclo, gli operatori spruzzano del grasso sull'estremità del cuscinetto. Tutto qui", ha affermato Burris. "Siamo molto soddisfatti. Otteniamo dei buoni solidi usando meno sostanze chimiche e lavorando meno giorni. Cosa si potrebbe chiedere di più?"
Informazioni sull'autore
Robert Rhea è Direttore delle vendite presso Flottweg Separation Technology Inc. È possibile contattarlo all'indirizzo rrhea@flottweg.net.