31.05.2021
Un voyage dans le temps - le séparateur Flottweg et son histoire
Depuis plus de 20 ans, le séparateur fait partie de la gamme Flottweg . Lors d'un entretien, Frank Giegler, ingénieur procédés chez Flottweg, et Christoph Hobmeier, ingénieur développement chez Flottweg, partagent l’histoire passionnante du séparateur Flottweg et commentent a manière dont les progrès technologiques ont aidé des ingénieurs comme vous à travailler plus efficacement sur la séparation solide-liquide.
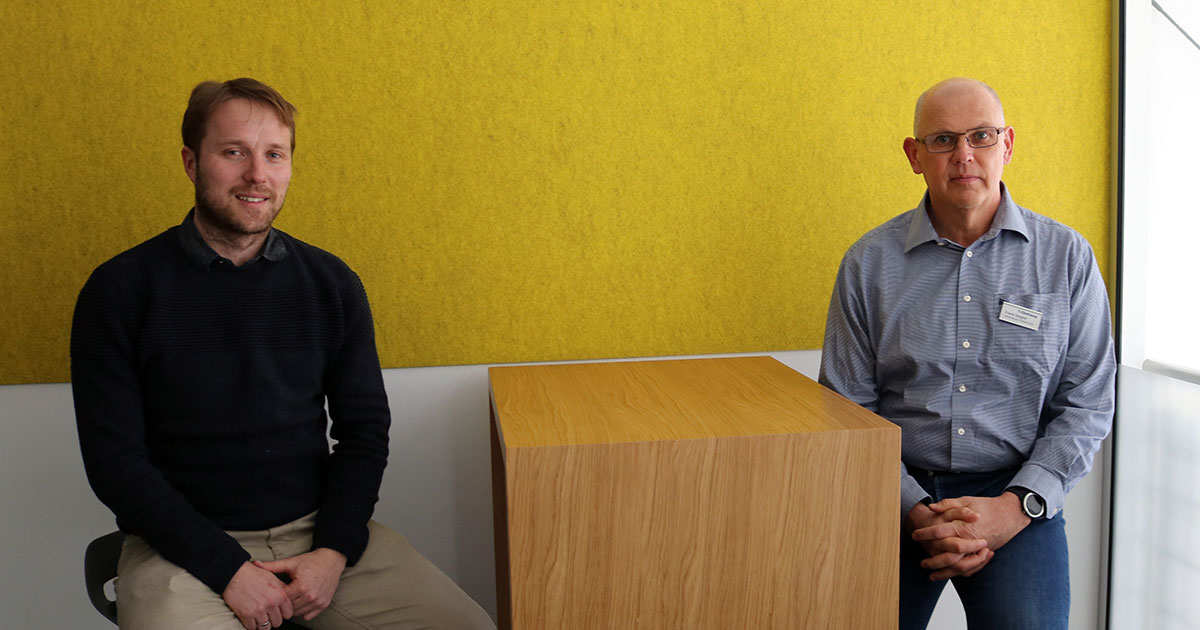
Le séparateur fait partie de l'offre produits Flottweg depuis plus de 20 ans. Comment tout a commencé ?
Frank :
L’histoire des séparateurs chez Flottweg est un peu plus longue que ce que la plupart des gens pensent. Dans les années 1960 et 1970, des études initiales ont eu lieu sur le séparateur. Vers la fin des années 1980, Flottweg a commencé à collaborer avec Veronesi situé à Bologne, en Italie. Veronesi est ensuite devenu une filiale de Flottweg. Avec l'apport des séparateurs Veronesi, Flottweg a pu élargir son offre de produits afin de proposer des solutions de séparation en aval des décanteurs. Le site de production Veronesi n'était pas adapté à la nouvelle machine AC2500 en projet (machine de plus grande capacité), c’est pourquoi, en 1998, il a été décidé de transférer la production à Vilsbiburg. C’est ainsi que mon histoire a commencé à Flottweg. L'AC2500 a été développé pour répondre aux besoins du marché des jus de fruits et du vin. Un an plus tard, et après avoir surmonté quelques obstacles, un prototype fonctionnait dans notre centre technique. La machine a ensuite été fiabilisée en 1999 et 2000. En 2001, le moment était enfin arrivé : Notre directeur actuel, M. Fritz Colesan, a vendu, à une cave vinicole, le premier séparateur construit par Flottweg où il est en service depuis septembre 2001.
Qu’est-ce qui a changé depuis vos débuts jusqu'à aujourd'hui ?
Christoph :
Les gammes de produits ont été considérablement élargies. Nous avons commencé avec le modèle AC2500. Le modèle AC2000 est ensuite arrivé . Cette machine est légèrement plus petite et convient pour des débits deux fois moindres. Nous avons ensuite développé des modèles plus petits : l’AC1500, et enfin l’AC1200. De plus en plus de déclinaisons de séparateurs ont été développées, mais tout a commencé par un clarificateur à 2 phases pour les jus de fruits. Nous avons progressivement mis au point différents séparateurs pour la séparation en 3 phases, de même que des machines dotées de joints hydro-hermétiques, particulièrement adaptées pour la production de bière. Nous pouvons désormais proposer une large gamme de séparateurs pour les différents besoins. Par exemple, nous avons des machines avec une résistance à la corrosion plus élevée, pour des densités de solides plus élevées ou pour des produits à viscosité plus élevée. Les versions avec composants électroniques et certifications ATEX ont été développées pour une utilisation dans des zones potentiellement explosives. Ils sont équipés de notre système d'inertage. Cela peut être utile non seulement pour prévenir les explosions lors du traitement de produits potentiellement explosifs, mais aussi pour empêcher l’oxydation de certains produits alimentaires. Notre portefeuille n’a cessé d’être élargi depuis l’introduction initiale d’un grand clarificateur. Aujourd'hui, nous disposons de systèmes modulaires qui peuvent être adaptés à environ 70 configurations différentes.
Dans quelles applications les différentes conceptions de machines sont-elles utilisées ?
Frank :
Le trop-plein sur la phase liquide légère (huile ou graisse) est surtout utilisé à des températures élevées, par exemple pour de la graisse animale ou de l’huile de poisson. Le trop-plein sur la phase liquide lourd (eau) est par exemple utilisé pour de l’huile d’olive. Nous utilisons une garde hydro-hermétique principalement pour la bière ou parfois pour le vin. Cela dépend entièrement des besoins du client.
Nos séparateurs sont désormais utilisés dans de nombreuses applications. Comme mentionné précédemment, le premier séparateur est en service dans une cave vinicole depuis plus de 20 ans. Il a été suivi de séparateurs pour le traitement de jus de fruits, de pectine d’agrumes, de café, de caféine, de thé, de lait de soja, d’huile d’agrumes, de jus d’orange, de pectine de pomme, de bière, de lactosérum, d’huile d’olive, d'huile de poisson, de biodiesel, de graisses animales, d'alcools de bouche, d'huiles usagées, de produits pharmaceutiques, etc., et pour la récolte de micro-algues.
Christoph :
En principe, c’est ainsi : Nous disposons actuellement de quatre tailles différentes pour différentes plages de débit. Celles-ci sont essentiellement indépendantes du domaine d’application. Le produit entraîne les considérations techniques selon la façon dont il doit être modifié : dois-je choisir un clarificateur pour la séparation en 2 phases ou un séparateur pour la séparation directe en 3 phases ; dois-je choisir une machine avec une résistance à la corrosion renforcée ou un matériau standard ; dois-je utiliser une version pour des densités de solides plus élevées ? Nous avons adapté les machines pour qu’elles puissent traiter une grande diversité de produits, indépendamment de la densité des matières sèches qui s'y trouvent ou du risque de corrosion.

Comment démarrer un projet et y a-t-il une équipe spéciale "Séparateur" dédiée chez Flottweg ?
Christoph :
Officiellement, il existe, au sein du service R&D, une équipe de développement pour les séparateurs. Cependant, tous nos ingénieurs ont suivi une formation polyvalente et sont capables de concevoir ces systèmes. L’équipe "Séparateur" se compose de plusieurs ingénieurs et fait partie des quatre équipes de développement Flottweg fonctionnant avec une approche hautement interdisciplinaire. Outre les membres permanents du projet, le personnel du développement, de la conception et de l’ingénierie des processus est fortement impliqué pendant la phase de conception. C'est à ce stade que nous déterminons les caractéristiques du produit que la machine traitera et conceptualisons la conception du système. Les achats, la gestion de production et la planification de projet sont également des membres permanents des projets en développement. En outre, certains membres temporaires de l'équipe ne sont pas nécessaires pendant toute la durée du projet, mais jouent néanmoins un rôle important. Le service commercial, par exemple, est impliqué au tout début et à la fin du projet lorsqu' il s’agit de tester les prototypes sur site. La production et l’assemblage sont principalement impliqués dans le projet lorsque les prototypes sont fabriqués ou assemblés. Une bonne communication est cruciale. Le contrôle et la documentation sont également inclus dans certaines phases d’un projet. Le département de documentation est généralement amené à intervenir à la fin du projet pour créer des instructions et des manuels adaptés afin que le produit puisse être mis en œuvre sur le terrain et entretenu correctement. En fin de compte, un nouveau projet implique presque toute l’entreprise, lorsqu'on tient compte des diverses et nombreuses sollicitations. Le développement d’un projet peut prendre entre 1 et 2 ans, voire trois ans s’il est entièrement nouveau.
Comment se passe un processus d’achat de séparateur ?
Christoph :
Ni le développement, ni l’ingénierie des processus n'est impliqué pour des machines normales produites en série . Si l’application est déjà éprouvée, le service commercial peut la vendre de manière indépendante.
Lorsqu'un séparateur est commandé, le service commercial collabore avec le service conception pour spécifier la machine, puis rend le projet à la logistique de commande. Un ordre de production est généré pour l’assemblage, qui est utilisé pour construire et approuver la machine. La machine est ensuite livrée au client ou va dans notre usine pour être installée sur une plateforme (skid), recevoir une armoire de commande, etc.
Quelle est la fréquence des demandes pour des applications spécifiques ?
Frank :
Les besoins ou spécifications uniques sont assez courants, en particulier dans les secteurs chimique et pharmaceutique. Souvent, des exigences particulières doivent être respectées, telles qu’une résistance plus élevée, une densité supérieure ou des normes de qualité ou de séparation du produit. Nous sommes là pour aider sur tous ces points.
Christoph :
Les tests de faisabilité sont au centre de nos recommandations. Le service commercial peut se trouver confronté à une demande de client qu'il ne peut satisfaire avec l'une des 70 déclinaisons actuellement disponibles. Le service commercial soumettra alors une demande de faisabilité au service Technologie. Les ingénieries de processus et de développement estiment les efforts nécessaires pour répondre aux exigences de ce client. Il est ensuite décidé d’approuver ou non cet effort et de s'engager au près du client.
Quels ont été les projets les plus passionnants ou extraordinaires jusqu'à présent ?
Frank :
Un projet-test vraiment passionnant s’est déroulé dans une brasserie à Munich. Il était assez difficile de mettre la machine physiquement en place . Nous espérions tous que nous n’aurions jamais à ressortir la machine des profondeurs de la cave, car cela aurait été encore plus difficile que de l’y installer. Nous avons d’abord testé toutes leurs recettes de bière courantes avec le séparateur. La bière transformée a été mise en bouteille, avec et sans utilisation du séparateur. Des échantillons ont ensuite été prélevés pendant trois mois pour déterminer s’il y avait un changement de goût. Ce n’est qu’après avoir validé qu’il n'y avait pas d'altération du goût que le séparateur a été remis en service. Il nous a fallu trois mois de plus pour vendre la machine, ce qui nous a permis de lever un verre et porter un toast au festival de la bière local.
Nous avons connu la même situation avec un fabricant de pectine de pomme. Lorsque je leur ai rendu visite pour la première fois, il n'y avait que des séparateurs de la concurrence. Depuis, le client a remplacé presque toutes les unités de séparation par des machines Flottweg.
Christoph :
Pour moi, le projet de développement le plus passionnant était l’AC1200, car nous avions la liberté d’imaginer de nouvelles approches ou des approches différentes dans de nombreux domaines. Cette machine a été repensée de fond en comble, avec une nouvelle conception et une nouvelle construction du séparateur. C’était également la première fois qu’une approche interdisciplinaire était rigoureusement suivie. C’était un très bon projet pour l'apprentissage, en particulier pour moi.
Dans certains domaines, le séparateur Flottweg est encore considéré comme un nouveau venu. Pourquoi pensez-vous que c’est le cas ?
Christoph :
D'une manière générale, nous disposons de nombreuses conceptions de machines et disposons de séparateurs fonctionnant efficacement dans de nombreuses industries et applications. Cependant, d’autres entreprises sont présentes depuis plus de 20 ans d'existence. Nous restons donc toujours les nouveaux venus dans certains domaines.
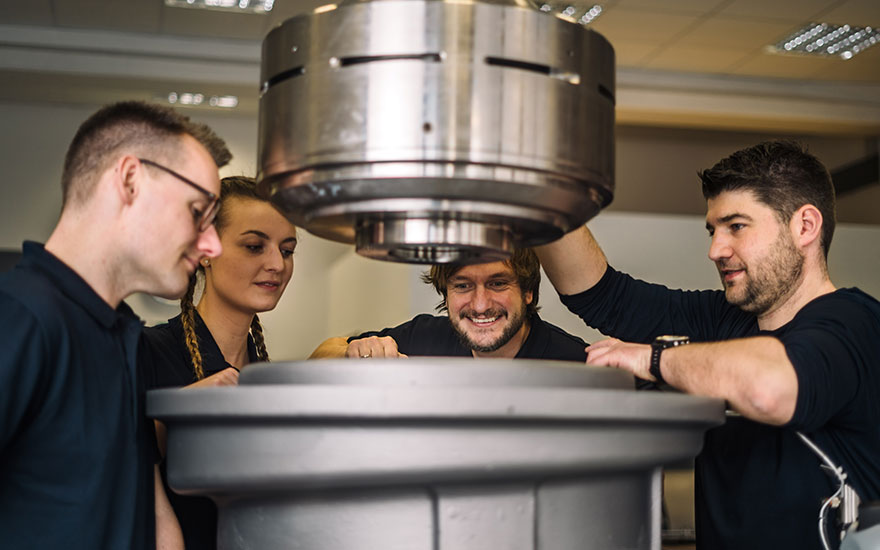
Qu’est-ce qui distingue le séparateur Flottweg ? Quels sont nos avantages par rapport à la concurrence ?
Frank :
En premier lieu, nos séparateurs sont extrêmement robustes dans leur traitement. Ils sont également très performants pour faire face aux fluctuations de processus. Comme mentionné précédemment, le client qui produisait de la pectine avait auparavant des séparateurs de nos concurrents. Ce client a demandé leur avis à ses techniciens de maintenance et ils se sont montrés clairement favorables à notre séparateur. Ils ont déclaré que nos séparateurs sont beaucoup plus faciles, moins chers et plus rapides à entretenir. Ses opérateurs ont également déclaré que notre machine était mieux adaptée que d’autres modèles aux fluctuations ou perturbations pouvant intervenir en amont du processus.
Christoph :
Notre machine est très robuste et très facile à entretenir. Deux personnes qualifiées peuvent rapidement démonter le séparateur en ses principaux composants, jusqu'à un niveau où il est possible de poser un diagnostic et de remplacer les pièces éventuellement défectueuses. Nous avançons assez vite à cet égard. Pour de nombreux clients, pouvoir effectuer des travaux de maintenance rapidement et facilement et faire redémarrer la machine rapidement est une préoccupation.
Nos séparateurs Flottweg se caractérisent également par leur système de débourbage. Outre sa conception simple et sa facilité d’entretien, le système offre également l’avantage de SoftShot®, qui réduit considérablement le bruit de décharge. Les mécanismes qui le permettent sont beaucoup plus simples que ceux de nombreuses machines concurrentes, mais ils offrent toujours la possibilité de déclencher un débourbage partiel ou total.
À quoi devons-nous nous attendre à l’avenir ?
Christoph :
Nous avons actuellement de nombreux projets intéressants en développement . L’un de ces projets est l’AC1500, dont la refonte intégrera une partie de la conception de l’AC1200, avec un changement de certains composants et assemblages. Nous sommes également sur le point de terminer le développement d’une nouvelle taille intermédiaire. Il s’agit de l’AC1700, qui, en termes de taille de machine, se situe entre les AC1500 et AC2000. Grâce à cette nouvelle taille de machine, nous pouvons répondre plus spécifiquement aux exigences de rendement des clients.
Le développement d’un séparateur à buses est un autre projet très prometteur. Pour Flottweg, il s’agit d’une nouvelle unité de séparation. Lorsque nous avons parlé de séparateurs jusqu'à ce jour, nous avons parlé de séparateurs auto-débourbeurs dotés d’un mécanisme hydraulique d’ouverture du bol . Le séparateur à buses dispose d’un grand nombre de buses installées sur la circonférence du bol au travers desquelles les solides sont évacués. Différents tests sont actuellement réalisés sur le terrain sur des prototypes . Les premiers tests sont très encourageants, c’est pourquoi les premières machines ont déjà été commercialisées. De plus, nous travaillons à compléter la modularité de la gamme. Nous prévoyons une nouvelle version de l’AC1500 pour pouvoir traiter des solides plus denses. Nous sommes également en train de développer l’AC2500 et l’AC1200exp (inerté pour les besoins ATEX). Nous avons donc une série de projets intéressants en développement .
Frank :
Des développements et améliorations mineurs sont également en cours, tels que la réduction de la consommation d’énergie de nos machines ou de petites adaptations qui découlent de demandes de faisabilité.
Christoph :
Pour résumer, vous pourriez dire : Nous complétons notre portefeuille de produits, l’élargissons pour inclure de nouvelles tailles, et avec le séparateur à buses, nous innovons même.
À propos de nos experts
Christoph Hobmeier
A rejoint Flottweg en 2015
Ingénieur de développement au sein de l’équipe MDS (Machine Development Separator)
Frank Giegler
A rejoint Flottweg en 1998
A commencé aux tests et travaille maintenant au développement de l’ingénierie de processus

Souhaitez-vous en savoir plus sur Flottweg ?
Appelez-nous ou écrivez-nous !