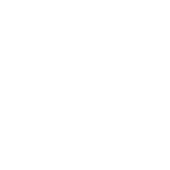
The Flottweg Separator Centripetal Pump: Discharging the Liquid Phase(s)
Centripetal Pumps are used in disc stack centrifuges when the liquid to be clarified or separated
- Should come into contact with the air as little as possible
- Should not be sprayed
- Should not be allowed to foam
- Evaporates easily
- Is poisonous
- Should be discharged under pressure
The separated liquids are discharged from the Centripetal Pump under pressure. How the Centripetal Pump works can also be compared with a centrifugal pump or rotary pump.
Clarifying separator (2-phase separation)
A Centripetal Pump transfers the clarified liquid out of the separator under pressure.
Purifier (3-phase separation)
A dual Centripetal Pump transfers both the heavy and the light liquid phases out of the separator under pressure after separation. A combination of single Centripetal Pump and free drain (drainage of one liquid phase without pressure) is also optionally possible.
The Structure and Functionality of the Centripetal Pump
The Centripetal Pump (also called an impeller) is a cylindrical disk with multiple channels. These channels follow a curved path from the outer rim of the disk to a central drain pipe. The Centripetal Pump's outer rim dips into the rotating liquid. The channels guide ("peel") the clarified or separated liquid into the central drain pipe. The rotational speed of the liquid is converted into pressure. The liquid pressure generated depends on the bowl speed, the diameter of the Centripetal Pump, and the immersion depth.
Advantages/Features of the Centripetal Pump
- The Centripetal Pump acts like a pump and can provide the pressure needed for downstream processes
- The separated liquids are guided out of the bowl without air or foam
- When separating liquid mixtures, fine regulation of the separation zone is possible using the counterpressure