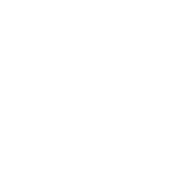
Flottweg Lubrication Systems At A Glance
Different applications and customer requirements require different lubrication systems to ensure a long service life for the decanter centrifuges in use. Maintenance overhead (operating modes such as continuous operation, seasonal use, etc.) is the determining factor in the selection of a lubrication system. The availability of the different lubrication systems also depends on the centrifuge model.
In a decanter centrifuge, the gears, scroll bearings, and rotor bearings are supplied with lubricants. For rotor bearings, there is a difference between grease lubrication systems (manually using a grease gun, central lubrication system, or automatic central lubrication system) and oil/air lubrication systems. Flottweg scroll bearings are lifetime lubricated or can be relubricated.
Manual Lubrication With a Grease Gun
This lubrication procedure permits direct relubrication at both rotor bearing blocks of a Flottweg decanter centrifuge using a grease gun.
Manual Lubrication and Its Advantages
- Simple design (the simplest construction and low costs of procurement)
- Very simple to use the grease gun
- Lowest maintenance costs, since the grease gun can be used for multiple decanter centrifuges
Central Lubrication Systems From Flottweg
Central lubrication systems supply multiple lubrication points with lubricant simultaneously. This is done using a manually operated pump that precisely distributes lubricant to the lubrication points of the Flottweg decanter centrifuge (using a piston distributor).
The Advantages Of a Flottweg Central Lubrication System
- Very precise metering of grease
- Simplest possible handling with a single pump
- Little time needed for relubrication
Automatic Central Lubrication System
In comparison with a central lubrication system, an automatic central lubrication system ensures that grease automatically reaches the necessary lubrication points at defined intervals.
Automatic Central Lubrication Systems and Their Advantages
- No overlubrication and no excess greasing
- No personnel overhead for lubrication
- Lubrication quantity and grease reserves are monitored
Flottweg Oil/Air Lubrication System
An oil/air lubrication system is a minimum-quantity lubrication system in which oil droplets are transported to the lubrication points using a stream of compressed air. The operational reliability of a Flottweg oil/air lubrication system is due to continuous monitoring. A pneumatically driven variant permits its use in areas at risk of explosion (areas in which explosive atmospheres can occur)
The Advantages Of an Automatic Oil/Air Lubrication System
- Permanent lubrication and cooling of the rotor bearings
- No oil changes needed ► oil consumption reduced to a minimum
- Slight overpressure at lubrication points prevents the penetration of gases or aerosols into the rotor bearings
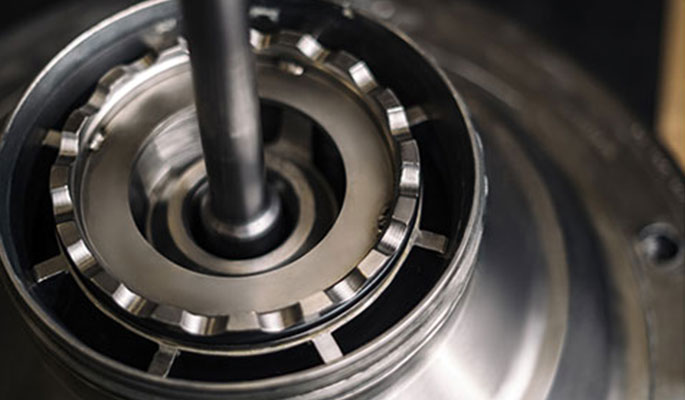
The Flottweg lubricant duo: Endrive & Sympact
As different as Flottweg machines are, they all have one thing in common: They are robust and durable. To help maintain this, Flottweg offers its own lubricants, which are specially tailored for use with Flottweg products.
Endrive
On one hand, we have our gear oil 'Endrive'. Its name comes from the combination of "enduring" and "drive", because that’s exactly what this oil does: It drives gears for as long and hard as you need.
Endrive is particularly suited for use in the food and pharmaceutical industries, which must meet high standards for hygiene and quality. As such, Flottweg uses only high-quality raw materials and advanced additives for its gear oil.
Benefits of Endrive at a glance:
- Perfect for lubricating Flottweg Simp Drive® gears
- Exceptional wear protection for gears and roller bearings
- Superb shear stability for reliable formation of lubricating film
- Broad operating temperature range thanks to excellent viscosity-temperature behavior
- Save energy thanks to optimized friction behavior
- Certified according to NSF ISO 21469 -> compliance with your company's hygiene requirements
Sympact
Flottweg also offers the Sympact roller bearing grease, which forms a perfect symbiosis with your Flottweg machine. This grease is used at friction points that require high mechanical damping and good adhesion. The result: smooth workflows, protection against wear, and a longer service life for roller bearings.
What's more, Flottweg's Sympact is also NSF-H1 certified. This means that no impurities are created as a result of unforeseeable contact with products and packaging in the food, cosmetics, pharmaceutical, or animal feed industries.
Benefits of Sympact at a glance
- Increased ease of operation thanks to lubricant damping of friction points
- Optimal functionality of your component thanks to excellent adhesion behavior and associated retention at the friction point
- NSF ISO 21469 certification