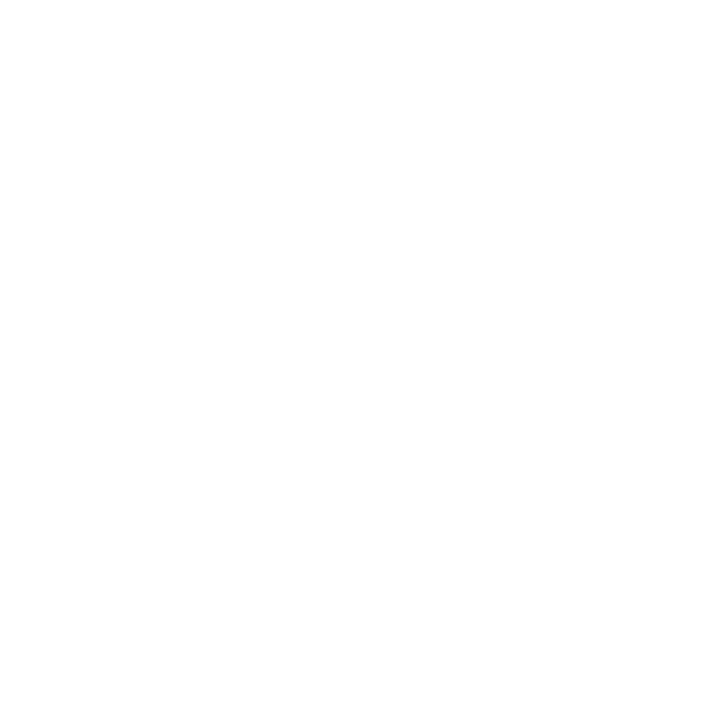
Decanters in a hygienic production environment
In comparison to non-food processing, production processes in the food, animal feed, pharmaceutical and cosmetics industries place increased demands on hygiene.
The challenge of creating a hygienic production environment is to design machines and processes so that they can be cleaned to the highest possible standards, while at the same time complying with all the necessary standards and achieving the required separation results. Here Flottweg guides and supports you with more than 60 years of experience and know-how in the field of mechanical solid-liquid separation.
Production safety through reliable cleaning
When designing a cleaning process, the focus is always on achieving the best possible reproducible result. With increasing resource and personnel costs, it is important to include economic aspects in the considerations. From the outset, engineering must ensure that cleaning cycles are designed efficiently.
During the design of hygienic decanters and the associated peripherals, the focus is on avoiding dead zones in machines and systems, i.e. areas where difficult-to-remove contaminants and product residues accumulate.
The designers adjust the quality and form of the product contact surfaces in order to quickly achieve the desired cleaning result. Depending on the product and requirements, the quality and form of the surfaces in contact with the product can be mutually agreed upon and designed accordingly.
Depending on the product to be processed, the hygienic Flottweg decanters are equipped with cleaning nozzles in different positions. Cleaning can be individual or fully integrated into the automatic CIP process of a complete system. The cleaning system can be designed as a non-recirculating cleaning system or as a stacked system with recirculation of the cleaning media. Flottweg hygienic decanters can be integrated into existing or new processes in a configuration specific to the customer and the process.
The parameters required for CIP cleaning are stored separately in the control unit so that the cleaning process can be reproduced. The parameters can also be adapted to changing process conditions. Our automated and remote-adjustable impeller can make the CIP process much easier. If the pond depth of the decanter is changed, each area within the centrifuge can be rinsed and cleaned sufficiently and purposefully without intervention by operating personnel.
- The surfaces in contact with the product are optimally designed in terms of quality and form.
- Cleaning nozzles positioned specifically for the product.
- Can be integrated into existing or new process environments.
- Automated CIP cleaning by means of remotely adjustable impeller.
Hygienic design of machines
For machines, apparatus and plants used in hygienic production environments, compliance with all the necessary framework conditions is already taken into account during the design and construction process.
In addition to a variety of other aspects, the USDA design notes and the EHEDG guidelines are implemented as comprehensively as possible. For example, the surfaces in contact with the product are identified, the appropriate materials and auxiliaries are selected for the application, and dead zones are avoided by design. These instructions and guidelines are also defined in Flottweg’s own company standards.
- Implementation design notes from all applicable guideline documents, incl uding EHEDG, USDA.
- Expert advice throughout the project.
Many possibilities for validation
In the manufacturing of hygiene-sensitive products, it is important to know which critical control points are of essential importance for effective level control or for a HACCP concept.
In principle, machine and plant engineering can create the necessary foundation by designing the equipment and configuring the plant to meet hygiene criteria.
Working with the customer, a validation process can be carried out at Flottweg for separator systems intended for use in hygienic production processes. Here we use the classic riboflavin test. By request, other procedures can be carried out or contamination can be simulated based on the subsequent process.
All Flottweg machines can be integrated into the process in such a way that it is possible to take samples directly from the incoming product or cleaning agent flow, as well as directly from the outgoing media. This means that, for example, the cleaning procedure can be adapted during commissioning or at a later date if the customer changes the product or application.
- Suitable for integration into customer-provided step control systems.
- Riboflavin tests and further verification can be carried out to evaluate the cleaning success.
- Ability to sample all product streams.
The right choice of material
To ensure that no undesirable impurities are transferred to the product during the manufacturing process, only carefully selected materials are used in Flottweg's hygienic decanters. All contact surfaces are made of austenitic or austenitic-ferritic stainless steels. Elastomer seals and connectors meet the requirements of international regulations and standards, such as EC 1935/2004, FDA and EHEDG recommendations.
All lubricants used are food grade and have H1 approval.
- Use of high-quality stainless steels.
- All seals and connectors comply with international hygiene standards.
- Exclusive use of food-grade lubricants.
Success is ... Collaboration that leaves no questions unanswered.
Flottweg works alongside its customers from the initial idea to the successful commissioning and the acceptance of the machines. We support and advise in the design of new process peripherals and in the complete implementation of customer-centric specifications. We have over 60 years of experience in centrifugal separation technology. During this time, we have been able to gain experience across a wide range of demanding applications and process conditions. We use this know-how for every one of our customer projects, because for Flottweg only one thing counts: the success of our customers.