17.04.2019
Produktion Digital Dirigiert
Smart Factory ist ein großes Schlagwort, das die Digitalisierung der Produktion beschreibt. Auch bei Flottweg sind die Weichen für die Zukunft gestellt. Insbesondere in der datengetriebenen CNC- Fertigung wird dank der Digitalisierung die Produktion immer effizienter. Hier gibt es einen Blick hinter die Kulissen.
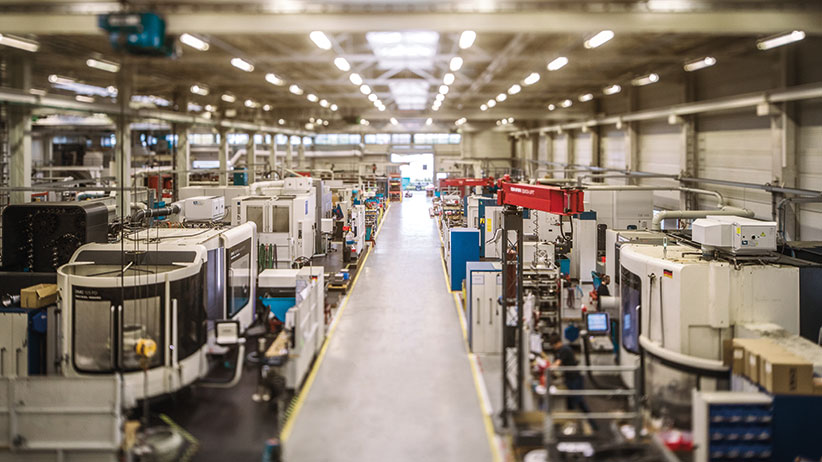
2009 begann Flottweg sich die IT in der Produktion mehr zunutze zu machen als nur für Verwaltung von Produktionsdaten und Auftragsabwicklung. Seitdem hat die Digitalisierung geholfen, die komplexen Prozesszusammenhänge in einer modernen Produktion noch besser zu durchschauen und entsprechend zu optimieren. Entstanden ist ein Weg zur Smart Factory, der aufzeigt, wie wertvoll die intelligente Nutzung der anfallenden Daten im Betrieb geworden ist.
Steigerung der Effizienz
Seit Beginn der Datenerfassung sind einzelne Fertigungsschritte zusammengeführt und Arbeitsschritte effizienter strukturiert worden. Diese Schritte reduzieren die Durchlaufzeiten in der Fertigung extrem. So benötigte die Fertigung eines Trommeldeckels einer großen Dekanterzentrifuge vorher rund 17 Stunden und heute nur 9 Stunden.
Insgesamt lag der Bruttobedarf von Werkzeugumrüstungen bis zum November 2018 bei 120.000 Umrüstungen. Effektiv umgerüstet wurden – dank einer intelligenten Vorausplanung mittels Zugriff auf die Daten aus den Werkzeugmaschinen – allerdings nur 35.000 Werkzeuge. Das bedeutet eine Ersparnis von 70,8 %, verteilt auf alle elf Maschinen. Menschlich betrachtet sind nun auch Tippfehler bei der Eingabe von Umrüstvorgängen ausgeschlossen. Diese Fehlerquelle ist seit Einführung des Systems nicht mehr aufgetreten und reduziert zu früher die Nachbearbeitung.
Daten 2.0
Datentechnisch hat sich Flottweg klar weg von klassischen Datensilos und hin zu vernetzten Datenbanken bewegt. Nun kommunizieren ERP, Programmiersystem, die Werkzeug- und Lagerdatenbank sowie das Zoller-Toolmanagement und die Messtechnik miteinander – und das nur so lange, wie der Auftrag aktiv ist. Danach bereinigt sich das System selbst und man hat keine Vor- oder Nachlagerung von redundanten Daten.
Mehr Produktivität dank Digitalisierung
Betrachtet man bei Flottweg die Veränderung der Prozesse, so hat die digitale Standardisierung mehr Freiräume in der Produktion ergeben. Modifizierte Aufträge und neue Werkzeugintegrationen lassen sich schnell umsetzen. Die laufende Datenpflege und -aktualisierung schafft einen nachhaltigen Vorteil. Damit verbunden ist auch eine Produktivitätssteigerung durch neueste Werkzeugtechnologien und Innovationen, die den Status der Fertigung immer aktuell hält.
Mensch-Maschine-Kooperation verstärkt
Harmonisiert man die Arbeitswelten von Mensch und Maschine, so bildet die Digitalisierung die Brücke. Bei Flottweg sind in der Wertschöpfung die Mitarbeiter nicht mehr mit „suchen“ beschäftigt, sondern gehen gezielt ihrer Fertigungsarbeit nach – ohne Zeitverzögerung. Die Arbeitswelten in der Produktionssteuerung verändern sich durch die digitale Struktur, da die Werkzeuge bei der Betriebsmittelvoreinstellung nun deutlich besser geplant und priorisiert werden können. Im Vergleich dazu kann ein einfaches ERP-System diesen Prozess in der Regel nicht ausreichend abbilden. Zeitgewinn und Effizienz gehen mit der neuen Mensch-Maschine-Kooperation Hand in Hand.
Wichtig für Flottweg ist der Kunden-Benefit mit einer flexiblen und schnellen Fertigung; denn kundenspezifische Ersatzteile lassen sich kostengünstig mit kurzen Lieferzeiten herstellen. Der eigene Vorteil liegt darin, dass kürzere Standzeiten und auf die Hälfte reduzierte Ausfallzeiten die Produktion auszeichnen.
Ausblick 2019
Das Ziel für 2019 geht klar dahin, dass sich mit Smart Data die Maschinen autark mit den Bearbeitungszeiten zurückmelden. Maschinenverfügbarkeit und Standzeiten lassen sich automatisiert und über eine Schnittstelle mit SAP auswerten. Gleiches gilt für die Wartungsanfälligkeit, die Ausfälle frühzeitig detektiert.
Flankiert wird diese Vorgabe mit einem neuen MES-System, das wichtige Kennzahlen zu Bearbeitungs- und Standzeiten sowie Wartungs- und Instandhaltungszeiten liefert. Damit schafft man Transparenz für Produktionszeiten, Verfügbarkeit und Performance. Die Fertigung gewinnt so noch mehr Qualität und Effizienz, da sich unproduktive Zeiten noch besser detektieren und auch Fehlerquellen identifizieren lassen. Geplant ist auch das Update von MR-CM® 2.0 auf ValueFacturing® 3.0, das von der Maschinenfabrik Reinhausen begleitet wird.