- Sustainable bioplastics production: maximum yield thanks to innovative separation technology
- 24/7 automated operation for maximum productivity in biopolymer production
- Full-service provider for various bioplastics separation processes with maximum process efficiency
Innovative solutions for the manufacture of sustainable biopolymers
Flottweg separation technology for the industrial manufacture of biobased plastics
Plastics are an essential part of our daily lives. They are found in almost all everyday objects that we come into contact with. However, conventional plastics are made from fossil fuels such as crude oil and pose considerable environmental problems in both their manufacture and disposal.
Bioplastics are sustainable and thus a future-oriented solution. They are produced from renewable raw materials such as maize starch, sugar cane, and vegetable oils using either direct fermentation or fermentation by microorganisms. These bioplastics are a promising alternative as they are biodegradable and consume fewer resources. Bioplastics are an important step towards a more sustainable future in which we can continue to enjoy the benefits of plastics without burdening the environment with the problems associated with conventional plastics: their significant CO2 footprint and the emergence of microplastics.
Flottweg supports producers of bio-based plastics in downstream processing with the most innovative separation technology. Be it the separation of organic acids such as lactic acid from biomass or the separation of biopolymers such as polyhydroxyalkanoates (PHA) as an end product.
Our machines for the industrial production of bioplastics
How is bioplastic manufactured industrially?
Manufacturing of polylactic acid (PLA)
PLA (Polylactic Acid), a polymer derived from lactic acid, is one of the most well-known biodegradable plastics and is made from raw materials such as cornstarch or sugar cane.
In the main process step, fermentation, the starchy raw materials are converted into lactic acid by microorganisms such as bacteria or yeasts. The fermentation solution is then purified in the separator and the lactic acid is extracted. Alternatively, a decanter can also be used for this. If the discarded biomass is washed again after the separator, the remaining lactic acid can be recovered via the Sedicanter® and the overall yield is improved. The isolated lactic acid is converted to PLA by polymerization and subsequently dried. Various additives can be used to give the raw PLA the right material properties, allowing it to have a variety of applications.
Polylactic acid is most commonly used for packaging and is therefore an alternative to classic packaging materials PE and PP. PLA is now also indispensable in agriculture, medicine, and 3D printing.
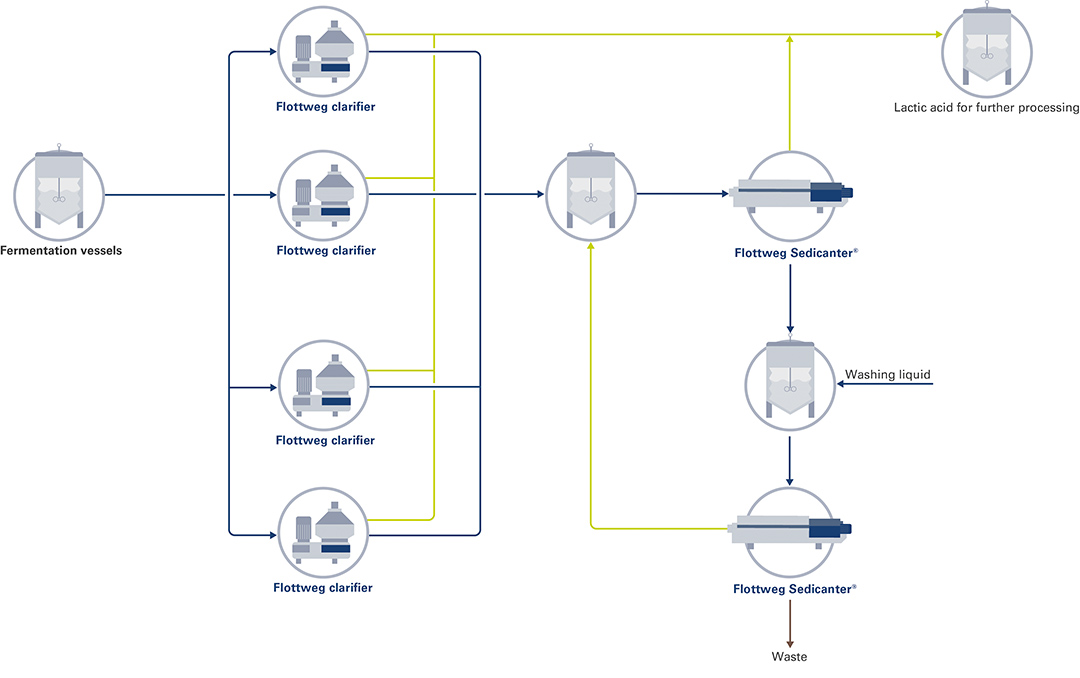
Manufacture of polyhydroxyalkanoates (PHA)
PHA (polyhydroxyalkanoate) denotes a superset of biopolymers that are formed as a reserve substance in microorganisms under defined conditions. As with PLA, natural raw materials are the basis for fermentation. In addition to various starch sources, oils, fats, and carbon gases such as CO2 or Methane can also be used to synthesize PHA.
The selected microorganism is grown in a culture medium until the cell density required for the start of the fermentation process has been reached. The intracellular biosynthesis of PHA is triggered under certain deficiency conditions and when there is an oversupply of carbon (e. g. due to oil). After cultivation, the biomass is separated from the fermentation broth using a nozzle separator specially developed by Flottweg. The biopolymer contained in the cell is released by breaking down the microorganisms (cell lysis) and then washed. In each wash step, a nozzle separator is used to separate the PHA from the remaining cell components, which remain in the liquid phase.
A decanter is used after the final washing step, as the resulting dry mass of the PHA is high enough to warrant subsequent drying. By using different microorganisms and primary raw materials, the chemical properties of PHA can vary and be actively influenced. In general, PHA is used in a similar way to PLA as a substitute for PE and PP.
The unique selling point of PHA is its rapid decomposition under natural environmental conditions. It decomposes within a few weeks in soil or seawater without leaving any residue, which means that the problem of microplastics associated with conventional plastics does not arise.
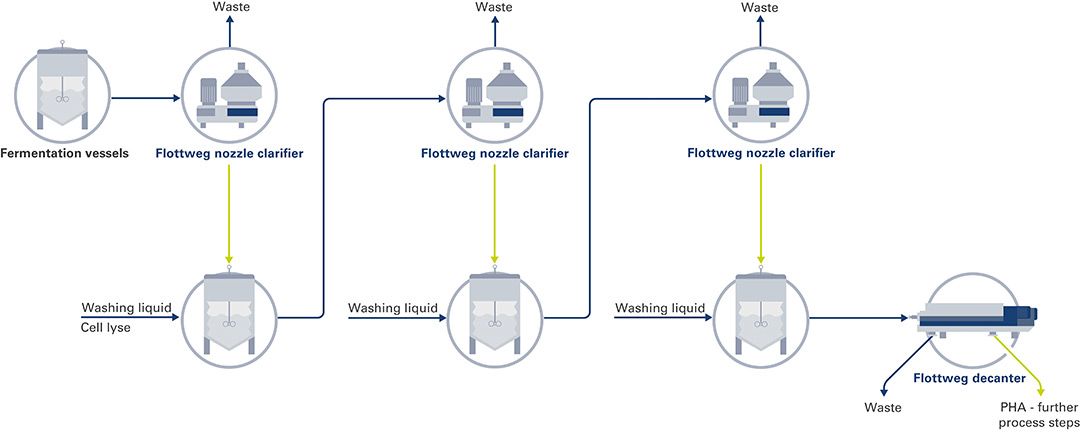
Your advantages in the production of bio-based plastic:
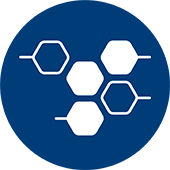
Customized solutions
Flottweg is the only supplier of industrial centrifuges whose product portfolio includes decanters, Sedicanter® and disc separators which feature discontinuous and continuous discharge. To meet a wide range of customer requirements in the manufacturing of bioplastics, Flottweg always has the optimum solution for the best separation results.
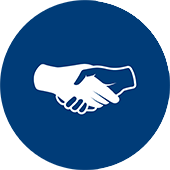
Competent support
We support our customers with comprehensive analysis and advice. In addition to laboratory tests, we offer pilot tests with test machines to determine the exact machine configuration. We also consider the ideal integration into your manufacturing process - from the scope of peripherals to a wide range of automation solutions.
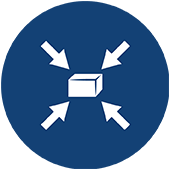
Low space requirement
Space requirements often play an important role. Flottweg offers compact machines that allow efficient use of space with seamless integration into existing plant infrastructure.
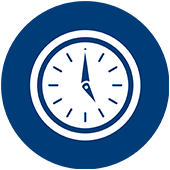
Continuous and automatic operation
Is it necessary to operate 24/7 without supervision? Flottweg centrifuges run autonomously and thus help to increase productivity.