- Minimize manure volumes: More storage capacity, lower transportation costs & environmental impact
- Flexible container solution for mobile use across farms
- Higher nutrient concentration: Valuable fertilizer & optimal biogas use
Less Manure; Increased Storage Capacity
Separating Manure with Decanter CentrifugesIn breeding farms and mast farms considerable quantities of manure are generated. The large volumes often present a challenge to farmers. New regulations (e.g. fertilizer ordinances in Germany) and limited storage capacities usually raise this question in agriculture: Where should the manure be stored?
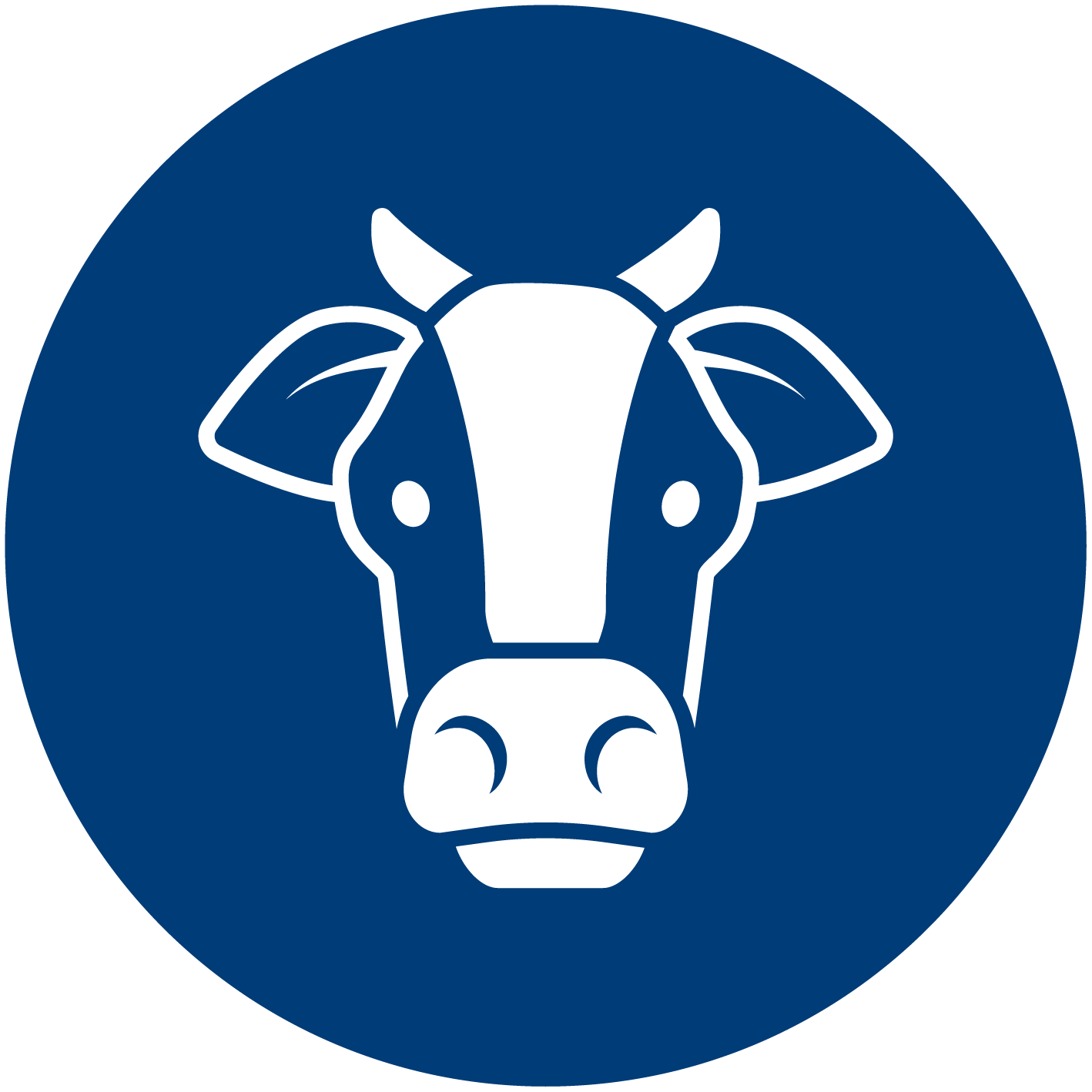
Simple Storage
In certain regions and seasons, restricted periods for the application of liquid manure apply. In order to store the manure, farmers have to create large storage capacities. By separating the manure, the quantity to be stored is reduced.
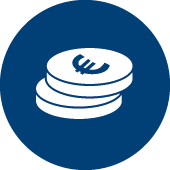
Reducing Transportation Costs
During restricted periods, manure is often transported to other regions. The transportation of manure as a hazardous material is connected to costs and emissions. By dewatering the manure, farmers reduce the quantity to be transported, and the solids also become more worthy of transportation due to increased nutrient loads.
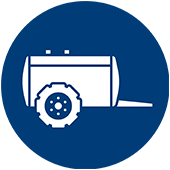
Raw Material for Biogas Plants
Centrifugal dewatering with a decanter shifts significant portions of the slurry into solids. Agricultural farms reduce the generated manure nutrients (mainly phosphate) by nutrient separation. The solid part can be used as raw material for biogas plants.

Increased Safety
The storing of manure is critical, as untreated manure becomes aggressively toxic. In order to avoid the risks of accidents like choking or drowning, operators have to fulfill numerous safety requirements. In addition, there is the issue of high odor and fine dust pollution. Dewatered manure facilitates the compliance with these safety requirements and increases the personal safety of farmers.
Our solution for the processing of liquid manure

Customer Benefits for Manure Treatment and Manure Dewatering
Increased Efficiency
- Centrifuges “Made in Germany”
- Highly efficient wear protection
- Continuous mode of operation and high capacity
- Easy to maintain
In comparison to other methods of manure treatment, centrifuges are extremely efficient and economical. Our centrifuges are “Made in Germany” and are highly effective, and their wear protection makes our Flottweg centrifuges robust against corrosive pig or cow manure. Due to the continuous mode of operation of Flottweg decanter centrifuges, large quantities can be processed within a short period of time. Our centrifuges are designed to be easily accessible and simple to maintain when it comes to servicing them. This reduces maintenance costs and increases the efficiency of the machine.
Mobile Applicable
- On request as a flexible container solution
- Can be used on an interplant basis
- Optimal for smaller companies, machinery rings, and agricultural outfitters
In comparison to stationary manure treatment plants, centrifuges can also be applied mobilely in containers. This makes the plant more flexible, energy saving, and more cost-effective. As a containerized system, the solution can be used on an interplant basis. Using the centrifuges makes the plant perfectly suitable for smaller companies, machinery rings, and agricultural outfitters.
Thin Manure
- Centrate is thin manure (2.0 – 6.0 % dry substance matter)
- Nutrient loads reduced by up to 50%
- Almost double the amount used per hectare
The centrate obtained can be described as thin manure, and it has a dry matter content of only between 2.0 – 6.0 % (depending on the starting material). Due to the significantly reduced phosphorus load as well as the reduced nitrogen load, significantly more manure per hectare can be spread than was possible prior to the treatment.