- German-engineered Tricanter® recovers up to 60% of valuable organics from crud
- Eliminate settler cleaning downtime and reduce maintenance costs permanently
- Continuous crud separation eliminates settler downtime and cuts operating costs
Reduce Solvent Losses by up to 60%
3-phase centrifuge for treating crud as part of the copper mining process
Most commercial solvent extraction plants suffer from the formation of crud. With Flottweg Tricanter® centrifuges, copper mines can recover organic from crud and reuse it in their solvent extraction processes.
The solvent extraction (SX) process is a hydrometallurgical procedure in which metals, such as copper, platinum, gold, cobalt, nickel, zinc, or uranium, are recovered through the use of organic extractants.
To separate the organic phase from the aqueous phase of the solvent, they are stored in settlers. Some of the impurities in the system build up in the settlers in the form of crud. The crud that is removed from the settler still contains considerable amounts of organic.
The Flottweg Tricanter® separates the organic and aqueous phase from the crud. This means that the copper mines can reuse the recovered organic in their processes and separated solids can be disposed of, significantly reducing operating costs
Flottweg has many years of experience in mining and solvent extraction. Combining high-quality materials and machines that are exclusively made in Germany, we help you get the most out of your SX process.
Flottweg separation technology benefits:
- Highly efficient extraction process
- Lower operating costs
- Very pure organic phase
The Flottweg high-performance centrifuge for extracting copper crud
Copper mining process and recovery of organic from copper crud
Acids are commonly used to extract the metal from the ore in a production process called leaching. The pregnant leach solution (PLS) is sent to the solvent extraction (SX) plant where in high intensity mixers, the PLS comes into contact with an organic extractant dissolved in an organic diluent. This mixture is referred simply as the organic. The metal ions migrate from the aqueous phase into the organic phase. This procedure is called solvent extraction. The solution flows from the mixers into settlers, where the organic phase is separated from the aqueous phase. Some of the impurities in the system build up in the settlers in the form of crud. This can occur at the surface of the organic phase, between the aqueous and organic phases, as well as at the bottom of the settlers. This crud can be a mixture of wind-blown dust, solids from leaching, impurities in plant solutions, or insects.
If the crud is allowed to build up in the settlers it may start moving into the next mixing stage. This can rapidly cause a ‘crud run’ resulting in severely increased entrainment. This, in turn, causes contamination of electrolytes with the leach solution and organic phase.
If the crud is allowed to remain in the settler, the settler has to eventually be taken offline to be cleaned. This leads to downtime and high maintenance costs. Crud is therefore regularly removed from the settlers, usually on a daily basis.
Operators vacuum the crud layer off and store it in a tank. From this tank, the crud is pumped into the Flottweg Tricanter®, which separates the crud into four phases: the organic phase, the aqueous phase, the solids phase, and the fourth phase. The fourth phase builds up at the organic aqueous interface. By adjusting the variable impeller of the Tricanter® correctly, the operator can ensure that this portion of ultra-fine solids is discharged as part of the aqueous phase. The dewatered solids are taken away for disposal or burning. The organic phase can be used again in the SX process, and the aqueous phase flows to the neutralization tank.
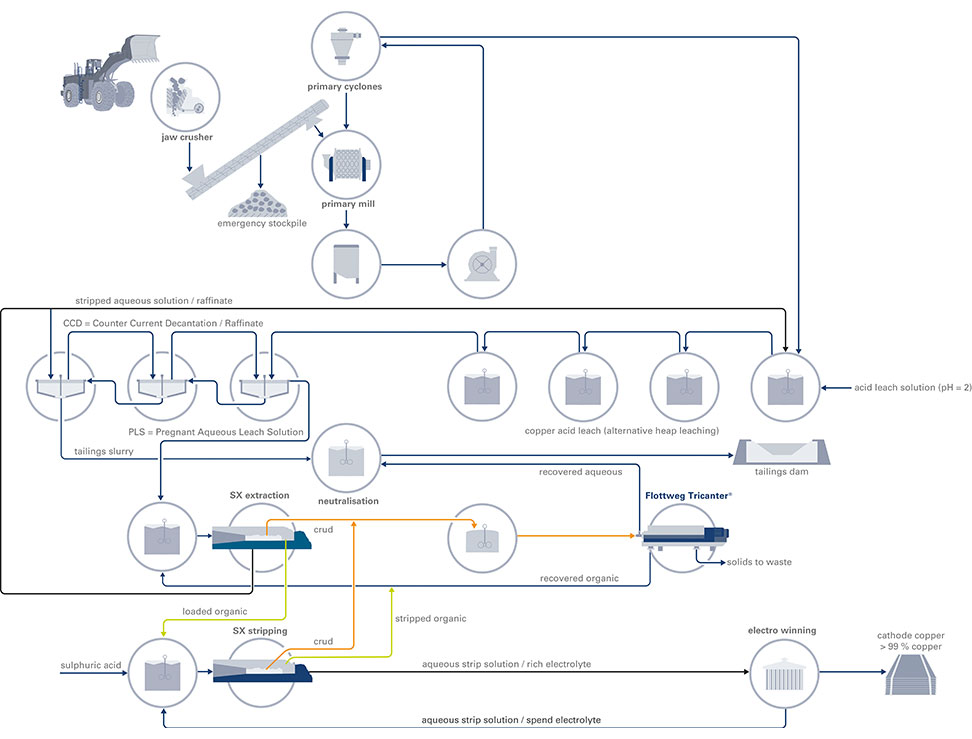
Customer benefits
Payback in almost 6 months
By treating crud, copper mines are able to recover huge amounts of organic. The recovered organic can then be reused in the process, meaning less 'new' organic has to be purchased. The Flottweg Tricanter® ensures crud is kept at low levels in the SX section. This results in lower carry over of solids to the EW section and reduces the load on the dual media filters in the EW section, reducing the cost of replacing filter media and copper losses through frequent backwashes.
Flottweg uses the Simp-Drive® gearbox for the Tricanter®. The Simp-Drive® is a unique drive system with two frequency inverters which allows automatic stepless adjustment of the scroll speed according to the incoming solids concentration in the feed, thus allowing fully automatic running mode. This makes the centrifuge very powerful and economic to use. Combined with strong wear resistance and replaceable wear parts, this can significantly reduce maintenance and operating costs. Payback usually takes less than six months (depending on the individual process).
- Large amounts of organic can be recovered
- Economic and efficient centrifuge drive
- Reduced load on dual media filters thanks to the Tricanter®
- Highly resistant to wear, saves on maintenance costs
- ROI usually between 4 to 6 months.
High-quality Tricanter® centrifuge: Made in Germany
High-quality materials and stainless steel play a very important role in copper production and in the solvent extraction process. Flottweg uses high-quality stainless steel. High-quality stainless steel mean longer machine lifetime and less maintenance. All of our industrial centrifuges are developed and built in Germany. This is how we make sure that our machines are of the highest quality and powerful at the same time. Our engineers are experts in their fields and have many years of experience in engineering and commissioning machinery and equipment in the ore and copper mining industry. The Flottweg Tricanter® is built with special features designed to get the most out of solvent extraction applications. These features, such as the Simp-Drive® gearbox and the adjustable impeller, ensure that centrifuges can be operated efficiently and economically.
- High-quality stainless steel
- Made in Germany
- Extensive process knowledge
- Special features for efficient operation
Easy operation and low downtime
Our 3-phase centrifuge is designed for continuous operation and is also very suitable for batch operation. As the crud can be treated efficiently, it can be continuously extracted from the settlers rather than building up. This eliminates the downtime which would otherwise be necessary to clean the settlers. Combining easily replaceable wear parts, high-quality materials, and an international service network, Flottweg guarantees the shortest possible downtimes and ensures consistent separation results. Manning requirements are also kept low thanks to the low maintenance and automatic operation mode. Ultimately, all of this helps mine operators significantly reduce operating costs.
The Flottweg Tricanter® for SX crud treatment is designed to meet the requirements for explosive atmospheres.
- Reduced downtime
- Continuous operation
- Consistent separation results
- Low personnel requirements
Flottweg centrifuges for the mining industry: a perfect match
Flottweg centrifuges are used in many separation processes in the mining industry. They are used to process ore and minerals, dewater tailings, dewater sand and gravel wash water, and to recover solvents in copper production.
To learn more, see the video explaining the benefits of decanter centrifuges: