- German-engineered separation technology maximizes instant coffee extract yield and quality
- Complete solution: from thin extract clarification to coffee oil recovery
- Smart, low-maintenance design ensures long-term reliability and easy operation
Economical, all-in-one solution for the manufacturing of instant coffee
Instant coffee has long since evolved from its niche existence as a coffee substitute and has become a lifestyle product. However, as its popularity increases, so do the requirements: Consumers don't just want to be surprised with new recipes, they also want to be impressed by their quality. Instant coffee producers are faced with the challenge of meeting these demands while making their production methods more and more efficient at the same time.
Flottweg separation technology supports many processing steps in the production of instant coffee. Our machines and systems are designed to meet the special requirements of the coffee industry. Various adjustment possibilities make it easy to adapt the machines to various raw materials and product properties.
Optimize several process steps in instant coffee production with Flottweg
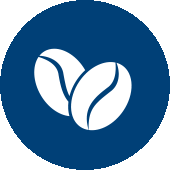
Increased yield of recyclable material
Flottweg provides powerful key technology for separating the insoluble components of the coffee beans from the valuable coffee extract. This increases the purity and quality of the finished instant product.
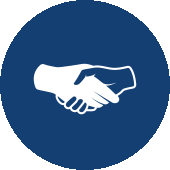
Customized solutions
We support our customers with comprehensive advice and laboratory tests. We also offer pilot tests for the precise design of the machine, commissioning at the customer’s premises as well as process optimization and integration into the overall system. As a specialist, Flottweg focuses on separation technology with the aim of optimum particle separation and yield.
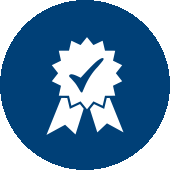
Made in Germany
Decanter centrifuges are developed and manufactured in Germany and stand for the highest quality, reliability, and compliance with international standards. The robust construction also ensures an above-average service life of the machines.

Smart machine design and easy maintenance
Flottweg machines are characterized by their intelligent design. Thanks to the optimized and reduced number of components, maintenance is uncomplicated and can also be carried out by your own personnel.
Our complete solution for coffee processing
The roasted and ground beans are extracted under pressure on an industrial scale. The resulting coffee extract contains some insoluble components. Separators remove these particles from the thin extract and from the thick extract after concentration. The solid separated in the thin and thick extract (the separator sludge) still contains small quantities of high-quality extract. The Flottweg decanter separates it from the solid phase with the addition of water.
The solids can be used for thermal recycling, while the separated extract is fed back into the process. Residues are produced when the coffee is extracted using percolators. These coffee grounds, which are still moist, are usually pressed out to make them thermally usable. The Flottweg Tricanter® simultaneously separates the resulting press water into three phases: de-oiled and clarified press water, coffee oil, and solids.
Various processes in the industrial manufacture of instant coffee
- Processing of thin and thick extracts
- Large clarification surface area for maximum particle separation
- Speed settings and separation resolution are adjustable
- Maintenance-friendly and robust design
- High performance despite variations in product
- High hygienic standards
- Soft Shot® for precise discharge with minimal loss of extract
Soluble coffee or instant coffee blends are obtained by extracting roasted coffee. The coffee extract solution contains certain undesired, insoluble components. Flottweg separators are used at precisely this point in the production process: These separators remove all visible particles, thus improving the quality of the finished product.
A customizable control concept adapts the separation resolution to customer requirements and the desired flavor carriers remain in the product.
At the same time, coffee particles pose a major challenge in processing. Reliable and repeatable discharge is ensured by specially adapted design features.
- Flottweg Simp Drive® drive for consistent high dry solids content and recovery rates
- High added value with improvement of overall coffee extract yield
- No foam formation, due to closed discharge under pressure
- Easy retrofitting and integration of the machine, even in existing processes
- High degree of automation
Depending on the process, degree of clarification, and the number of clarifiers used, a considerable amount of solids are discharged. This solid material contains valuable coffee extract. Therefore, further separation of the solid-extract mixture using a decanter is worthwhile. The resulting very dry solid matter (up to 50% DS) can be directly thermally recycled. The extract obtained is then returned to the process. This minimizes loss of product and increases efficiency.
- thermal recycling of the compressed coffee grounds
- higher efficiency in the subsequent coffee oil processing
- highly durable stainless steel
- straightforward design and easy access for cleaning and operation
After pressing, the residue from percolators or extractors, the so-called coffee grounds, can be used for thermal recycling. Fossil energy sources are substituted.
Depending on the overall process, the press water contains different amounts of coffee oil and residual extract. Both valuable products can be recovered in a two-stage process using a downstream Tricanter®.
- optimum separation results due to easy adaptation of the separation zones, even during operation
- cost-efficient yield of coffee oil
- discharge of the de-oiled, clarified press water
- efficient use of resources by achieving the maximum possible total yield of extract
The three phases contained in the press water can be separated in one process step with the Flottweg Tricanter®. Solids are separated and can also be forwarded for thermal recycling. The coffee oil, a valuable raw material, is separated from the residual extract. Depending on the quantity and purity of the oil obtained in this way, a separator can also be connected downstream to polish the oil phase.
If residual extract is to be recovered, the de-oiled and clarified press water can be fed back into the main product flow.
Increased efficiency even with small production volumes: Cold Brew and Co.
In contrast to the fully automatic production systems of large companies, smaller manufacturers are increasingly producing liquid coffee in batch mode. By adding hot water (or cold water, in the case of cold brew), the coffee extract is removed from the ground coffee beans batch by batch. The extract obtained in this way is usually extracted from the tank via sieve bottoms and then filtered. However, as the extraction residue in the tank contains valuable coffee extract, this can also be done more economically. In this process, the extract is lost with the residue.
At the same time, direct filtration of the valuable product is often difficult, as solids minimize the performance.
The Flottweg decanter can also increase the overall yield and product quality in such production environments: It permits the solids to be continuously separated from the coffee extract. High solids contents can be easily processed in the centrifuge. Due to the high dry matter of the discharged solid, the extract yield is significantly higher than the yield produced with the sieve tray method.
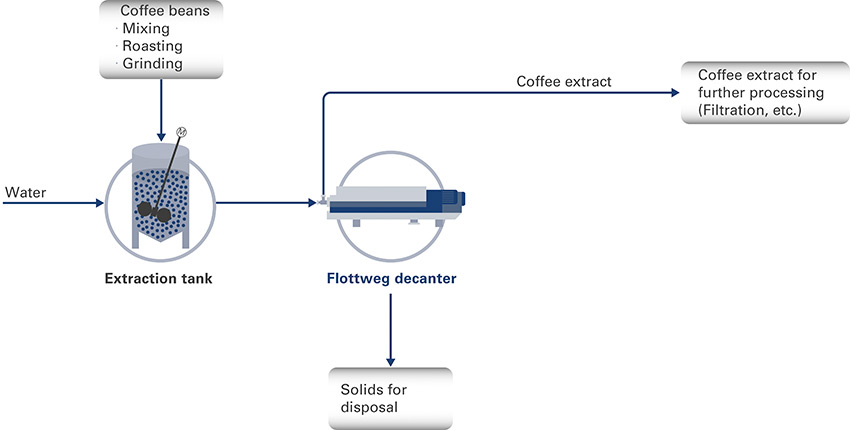